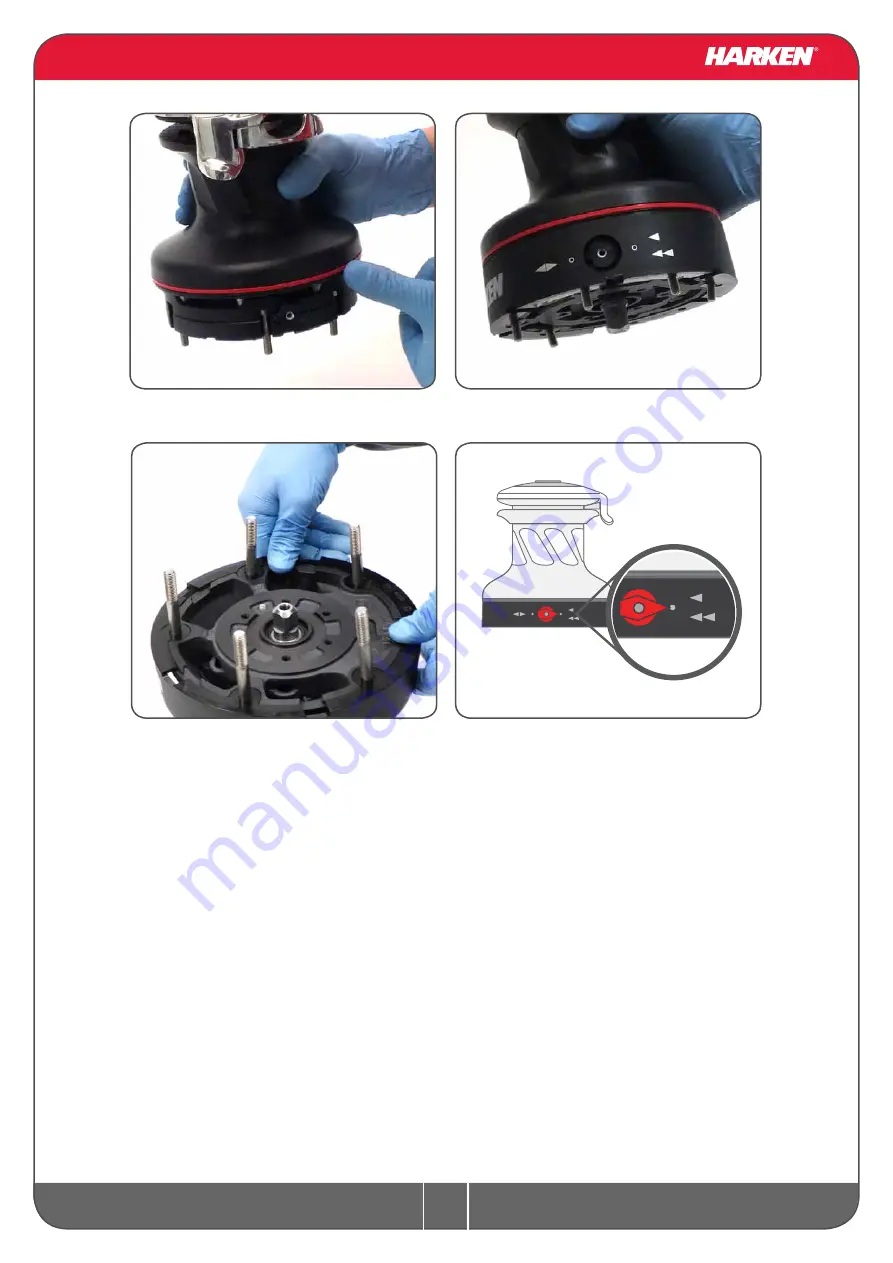
8
40 Rewind ™ Radial Winch
Installation and Maintenance Manual
NOTICE
Make sure the skirt is correctly clipped on to the base of the winch.
Install the winch on the deck in the position you have chosen, keeping in mind the limits described
on page 4 and using hexagonal headed bolts.
(See paragraph on winch installation)
3. Position the 5 M6 hexagonal headed
bolts in their holes
5. Press down the skirt to position it correctly
4. Reposition the skirt n°2 in its housing
6. Reposition the knob in the Rewind position
(see figure)