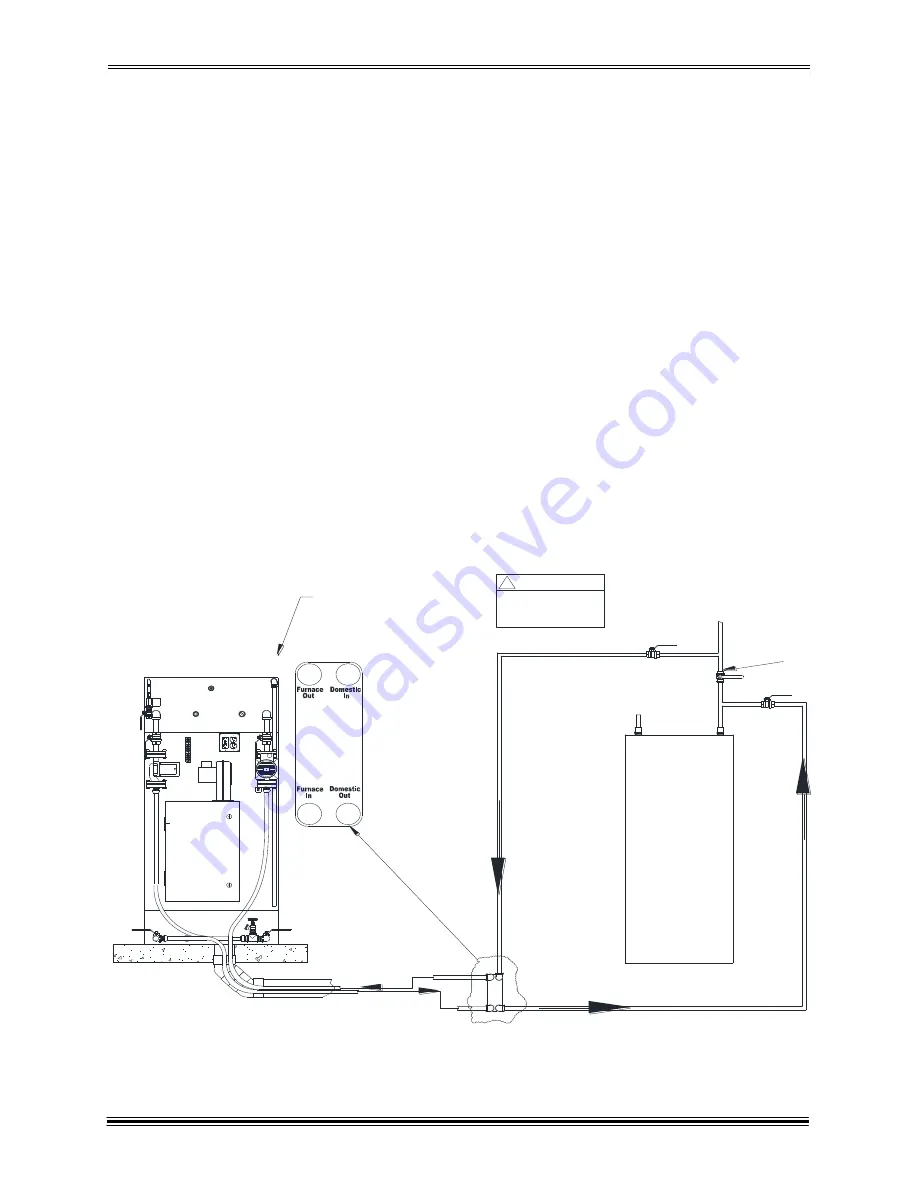
HARDY MANUFACTURING CO., INC (MODEL KB165) PAGE 19
Cold Water Supply
Water
Heater
Hot Outlet
Cold Inlet
!
DANGER
Water Temperature
over 125 degrees
can cause severe
burns instantly
Heater with hull and stacks
removed to show connections
P/N H300.02
20 Plate
Heat Exchanger
w/ 3/4" fittings
Close this
valve
SECTION V
PLUMBING OPTIONS FOR DOMESTIC WATER
5-1
Plate Heat Exchanger for Domestic Hot Water
To add domestic hot water to the KB165 hydronic heater, a plate heat exchanger and
pump can be added. This plate heat exchanger will provide preheated water to the
domestic hot water. The preferred method is to mount a plate heat exchanger at the
water heater and connect it as shown in the following drawing. The pump will circulate
heater water through the plate continuously. The cold water supply will need to be
connected to the opposite side of the plate heat exchanger and flowing in the opposite
direction for maximum efficiency. The alternate method would be to mount the plate
heat exchanger on the back of the wood heater and connect the water heater to the
plate the same way as in the preferred method with the water flowing in opposite
directions.
Summary of Contents for KB165
Page 2: ...THIS PAGE INTENTIONALLY LEFT BLANK ...
Page 6: ... MODEL KB165 iv THIS PAGE INTENTIONALLY LEFT BLANK ...
Page 12: ......
Page 64: ...THIS PAGE INTENTIONALLY LEFT BLANK ...