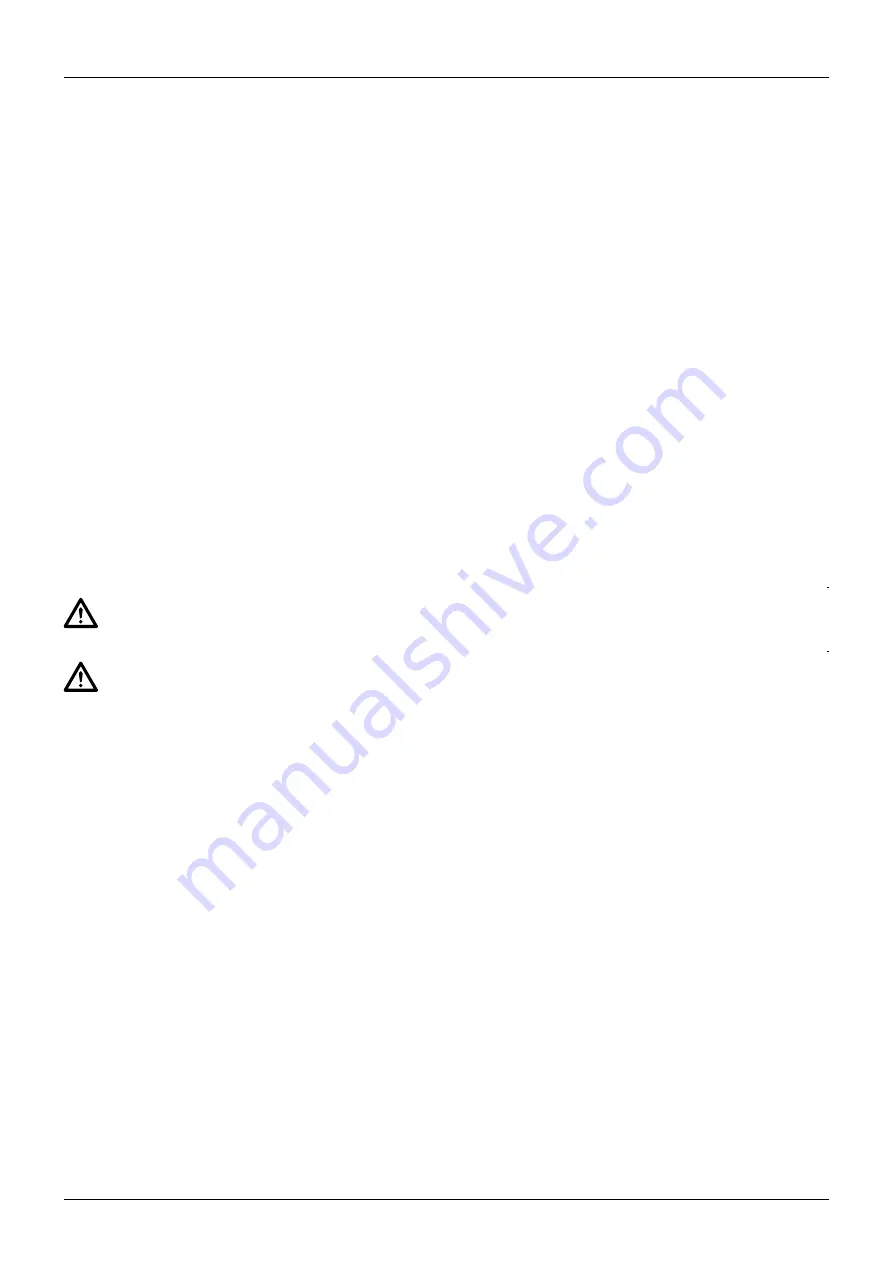
6 - Maintenance
6.14
DANGER! Non observance of mounting instructions will result in the bad seating of the tyre on the rim and could
cause the tyre to burst leading to serious injury or death!
DANGER! Never mount or use damaged tyres or rims! Use of damaged, ruptured, distorted, welded or brazed rim
is not allowed!
Should it be necessary to replace tyres, it is recommended to leave this to a specialist and follow the mentioned rules.
1. Always clean and inspect the rim before mounting.
2. Always check that the rim diameter corresponds exactly to the rim diameter moulded on the tyre.
3. Always inspect inside of the tyre for cuts, penetrating objects or other damages. Repairable damages should be repai-
red before installing the tube. Tyres with unrepairable damages must never be used.
4. Also inspect inside of the tyre for dirt or foreign bodies and remove it before installing the tube.
5. Always use tubes of recommended size and in good condition. When fitting new tyres always fit new tubes.
6. Before mounting, always lubricate both tyre beads and rim flange with approved lubricating agent or equivalent anti-
corrosion lubricant. Never use petroleum based greases and oils because they may damage the tyre. Using the appro-
priate lubricant the tyre will never slip on the rim.
7. Always use specialised tools as recommended by the tyre supplier for mounting the tyres.
8. Make sure that the tyre is centred and the beads are perfectly seated on the rim. Otherwise danger of bead wire tear
can occur.
9. Inflate the tyre to 100-130 kPa (14.5-19 p.s.i.) then check whether both beds are seated perfectly on the rim. If any of
the beads do not seat correctly, deflate the assembly and re-centre the beads before starting inflation of the tyre. If the
beads are seated correctly on the rim at 100-130 kPa inflate the tyre to a maximum of 250 kPa (36 p.s.i.) until they seat
perfectly on the rim.
10. Never exceed the maximum mounting pressure moulded on the tyre!
11. After mounting tyres adjust inflation pressure to operation pressure recommended by the tyre manufacturer.
12. Do not use tubes in tubeless tyres.
Change of tyre
Summary of Contents for RANGER PRO
Page 1: ...RANGER PRO www hardi international com 67009400 Version 1 01 GB 11 2006 Instruction book ...
Page 8: ...1 CE Declaration 1 2 ...
Page 46: ...5 Operation 5 16 Spray Technique see separate book Optional extras see separate books ...
Page 48: ...6 Maintenance 6 2 Trailer lubrication oiling plan ...