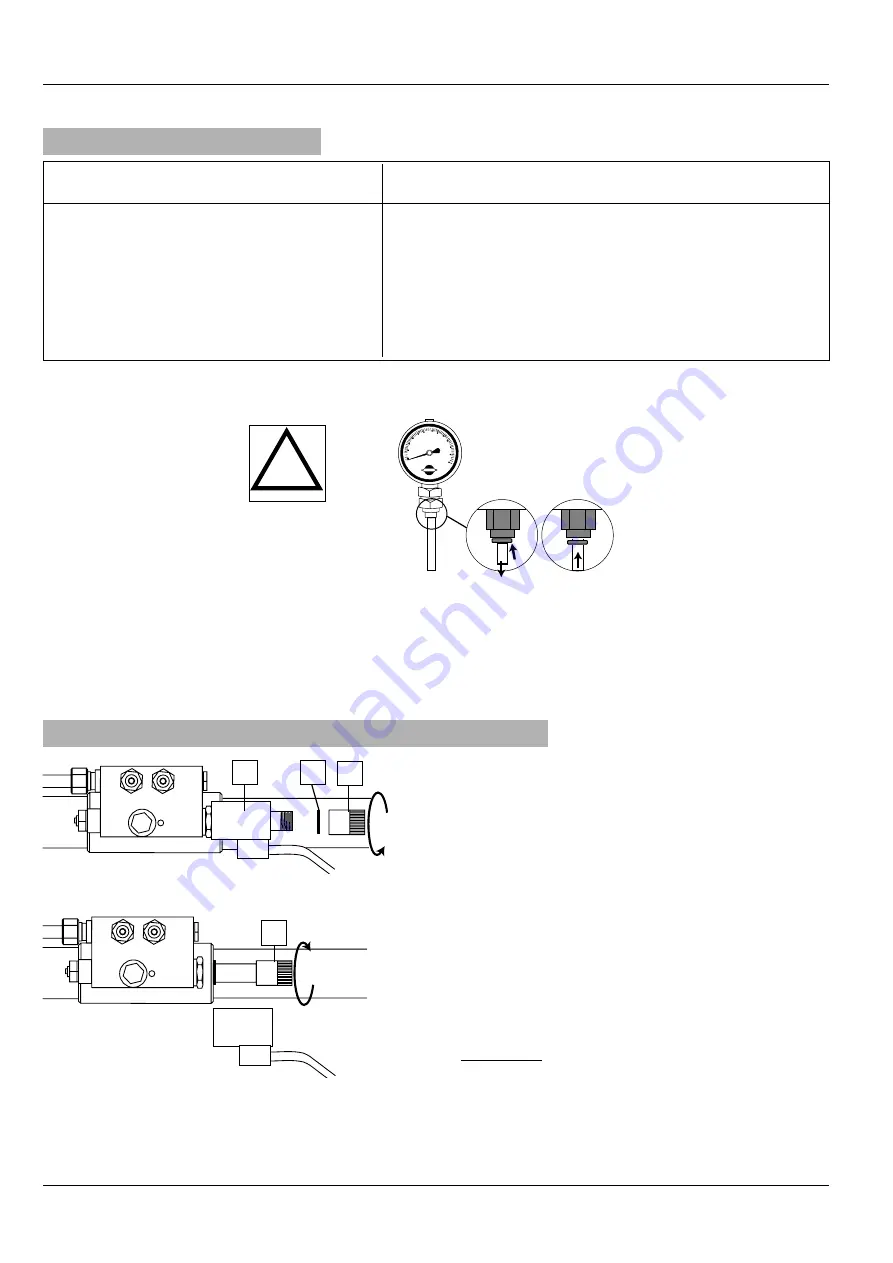
ALPHA PLUS HARDI NOVA
F
F A
A U
U LL T
T S
S II N
N O
O P
P E
E R
R A
A T
T II O
O N
N
CHAPTER
6
6- 12
False reading
Does not rest to zero
N
N..B
B.. :: T
Th
he
e o
op
pe
erraatto
orr m
maayy b
be
e ssp
pllaassh
he
ed
d w
wiitth
h lliiq
qu
uiid
d u
un
ne
exxp
pe
ecctte
ed
dllyy
- Check pressure gauge and circuit- Bleed the circuit
- Bleed the circuit with clean water
- Replace by a new pressure gauge if necessary
0
2
4 6 8
12
16
HARDI
284831
!
PROBLEMS
SOLUTIONS
REMOVAL
REASSEMBLY
6
6-
3
3
-
1
11
1
P
PR
RE
ES
SS
SU
UR
RE
E G
GA
AU
UG
GE
E
In case of power failure the pendulum device can be loc-
ked as follows :
1. Unscrew nut A
A
2. Remove O’ring B
B and coil C
C
3. Screw completely nut A
A to lock the pendulum.
C
A
B
A
LOCK position
6
6-
3
3
-
1
12
2
M
MA
AN
NU
UA
ALL O
OP
PE
ER
RA
AT
TIIO
ON
N O
OF
F P
PE
EN
ND
DU
ULLU
UM
M LLO
OC
CK
K
Summary of Contents for ALPHA PLUS 3500
Page 11: ...ALPHA PLUS TWIN FORCE 1 1 6 F F O O R R E E W W O O R R D D ...
Page 12: ...ALPHA PLUS TWIN FORCE 1 1 7 F F O O R R E E W W O O R R D D ...
Page 13: ...ALPHA PLUS TWIN FORCE 1 1 8 F F O O R R E E W W O O R R D D ...
Page 47: ...ALPHA PLUS HARDI NOVA P P R R E E P P A A R R A A T T I I O O N N CHAPTER 3 3 8 ...
Page 85: ...ALPHA PLUS HARDI NOVA M M A A I I N N T T E E N N A A N N C C E E CHAPTER 5 5 28 ...