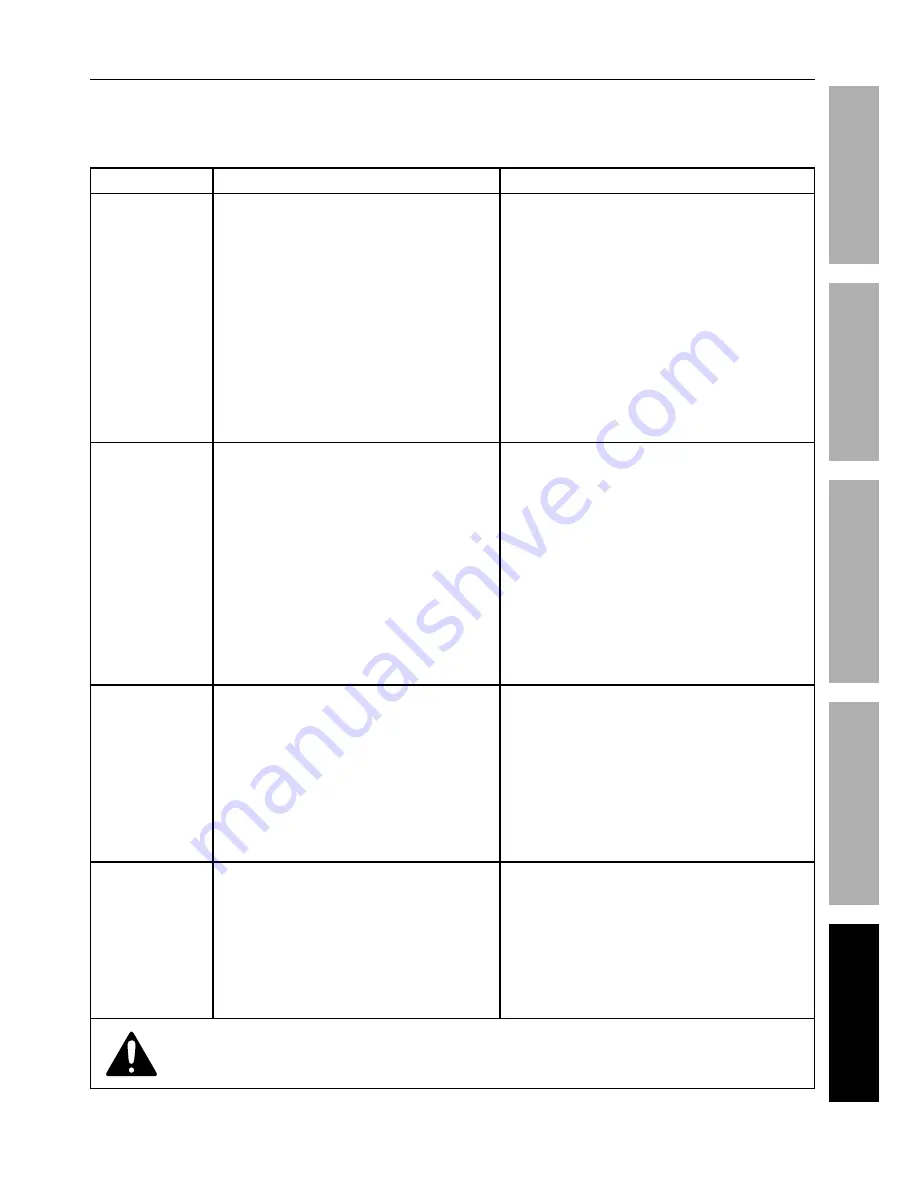
Page 29
For technical questions, please call 1-888-380-0318.
Item 63617
SAFETY
MAINTENANCE
BASIC WELDING
WELDING TIPS
SETUP
Problem
Possible Causes
Likely Solutions
When switched on,
Power ON Indicator
lights but Welder
does not function
1. Tripped thermal protection device.
2. Faulty or improperly connected Trigger.
3. Machine is in low- or
over-voltage protection.
4. Machine is in the incorrect mode.
1. If the Voltage Input/Thermal Overload Indicator
is illuminated, Welder has overheated and shut
down. Stop and wait with the Power Switch ON
for the Welder to cool. The Welder automatically
returns to service after cooling off. Reduce
duration or frequency of welding periods to
help reduce wear on the Welder. Refer to Duty
Cycle (Duration of Use) on page 18.
2. Ensure the gun connection is properly
seated on machine. Qualified technician
must check and secure/replace Trigger.
3. Check input voltage and ensure it falls within
the specified range. If input voltage is correct,
press Reset Button on back of machine.
4. Ensure the Process Selection Knob is
switched to the correct process.
Power ON Indicator
does not light when
Welder is switched on
1. Unit is not connected to outlet properly.
2. Outlet is unpowered.
3. Circuit supplies insufficient input voltage or
amperage.
4. Plug does not have correct rating.
5. Circuit breaker has tripped due
to high input amperage.
6. Input Power Cord is not seated properly.
1. Verify the voltage at the outlet and
the connection to the outlet.
2. Check circuit breaker/GFCI devices; if any are tripped,
determine and remedy cause before resetting.
3. Verify that the circuit is designed to supply the
required input voltage and amperage as detailed on
the Specifications table. If the Voltage Input/Thermal
Overload Indicator is illuminated on machine, check
the input voltage to ensure it is within specified range.
4. Make sure installed plug is correct rating.
See Specifications on page 7.
5. Press Reset Button on back of
machine to reset circuit breaker.
6. Ensure the twist lock input Power
Cord is fully secured.
Wire feeds, but arc
does not ignite
1. Improper ground connection.
2. Improperly sized Contact Tip.
3. Excessively worn Contact Tip.
4. Dirty Contact Tip.
1. Make certain that the workpiece is contacted
properly by the Ground Clamp and that
the workpiece is properly cleaned near the
ground clamp and the welding location.
2. Verify that Contact Tip is the proper size
for welding wire. If needed, replace
Contact Tip with proper size and type.
3. Check that the hole in the tip is not
deformed or enlarged. If needed, replace
Contact Tip with proper size and type.
4. Properly clean Contact Tip.
Porosity in the
weld metal
1. Shielding gas bottle is empty.
2. Not enough or too much shielding gas.
3. Dirty workpiece.
4. Gun is being used too far away from workpiece.
5. Polarity is incorrect for the application.
6. Dirty welding wire is introducing
contamination into the weld.
1. Check gas bottle and replenish as necessary.
2. Check gas regulator to ensure proper flow.
3. Clean workpiece down to bare metal.
4. Check CTWD (contact tip to work
distance) for the proper procedure.
5. Check the polarity and ensure it is DCEP
for MIG and DCEN for Flux-Cored.
6. Make certain that welding wire is clean
and free of rust and residues.
Follow all safety precautions whenever diagnosing or servicing the equipment.
Troubleshooting (continued)
IMPORTANT!
Be CERTAIN to shut off the Welder, disconnect it from power, and discharge the MIG Gun to
ground before adjusting, cleaning, or repairing the unit.
Summary of Contents for Vulcan Migmax 215
Page 1: ......