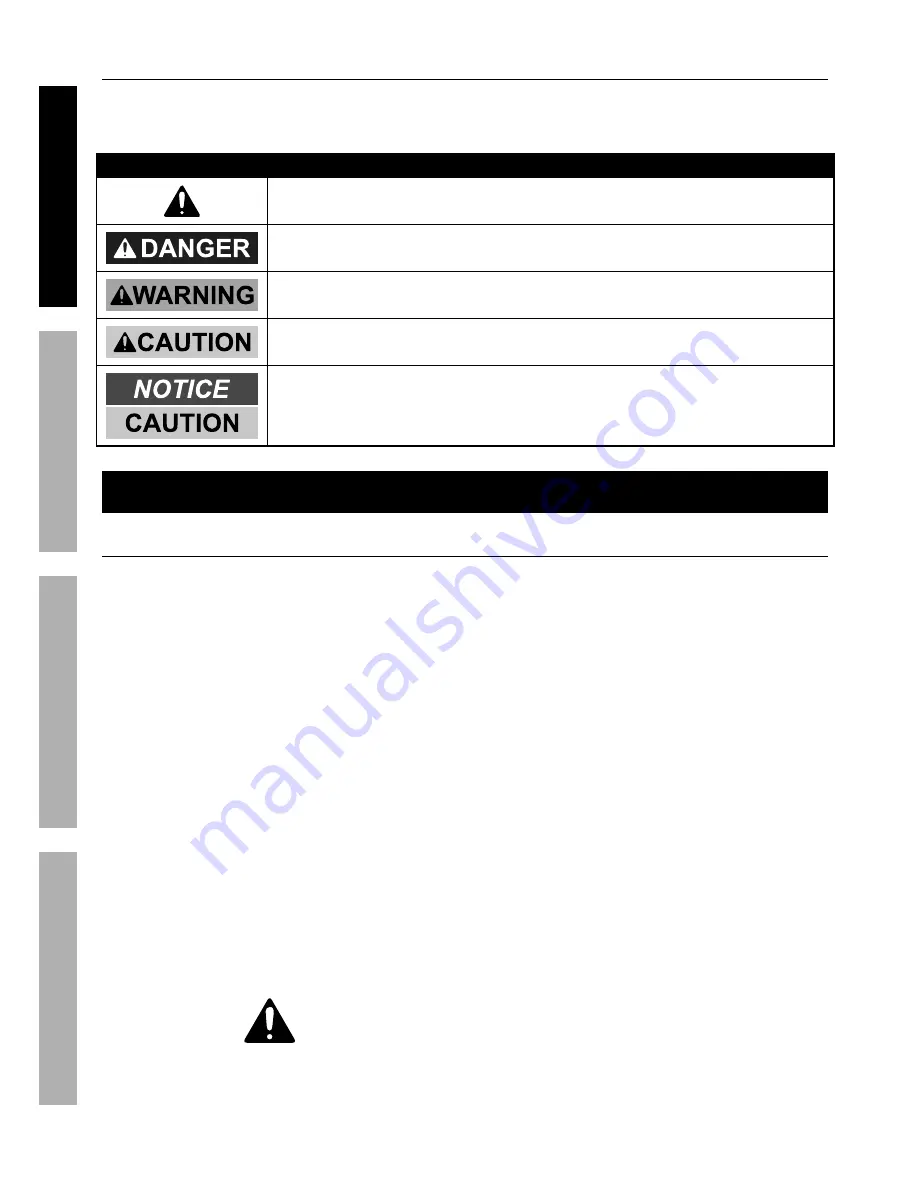
Page 2
For technical questions, please call 1-888-866-5797.
Floor Jack
Table of Contents
Safety ........................................................................2
Setup .........................................................................3
Operation ...................................................................4
Maintenance ..............................................................6
Parts Lists and Assembly Diagrams ..........................8
Warranty ...................................................................11
WARNING SYMBOLS AND DEFINITIONS
This is the safety alert symbol. It is used to alert you to potential personal injury hazards.
Obey all safety messages that follow this symbol to avoid possible injury or death.
Indicates a hazardous situation which, if not avoided,
will result in death or serious injury.
Indicates a hazardous situation which, if not avoided,
could result in death or serious injury.
Indicates a hazardous situation which, if not avoided,
could result in minor or moderate injury.
Addresses practices not related to personal injury.
IMPORTANT SAFETY INFORMATION
Floor Jack Safety Warnings
1. Study, understand, and follow all instructions
before operating this device.
2. Do not exceed rated capacity.
3. Use only on hard, level surfaces.
4. Lifting device only. Immediately after lifting,
support the vehicle with appropriate means.
5. Do not move or dolly the vehicle while on the jack.
6. Failure to heed these markings may result in
personal injury and/or property damage.
7. Lift only areas of the vehicle as specified
by the vehicle manufacturer.
8. No alterations shall be made to this product.
9. Never work on, under or around a load
supported only by this device.
10. Do not adjust safety valve.
11. Wear ANSI-approved safety goggles and
heavy-duty work gloves during use.
12. Keep clear of load while lifting and lowering.
13. Lower load slowly.
14. Apply parking brake and chock
tires before lifting vehicle.
15. Lift vehicle only at manufacturer
recommended locations.
16. Inspect before every use; do not use
if parts are loose or damaged.
17. Do not use for aircraft purposes.
18. The warnings, precautions, and instructions
discussed in this manual cannot cover all
possible conditions and situations that may occur.
The operator must understand that common sense
and caution are factors, which cannot be built into
this product, but must be supplied by the operator.
19. The Handle socket may be held down by a clip
under tension. Wear ANSI-approved safety goggles
before freeing Handle socket. Remove clip carefully.
IMPORTANT! Before first use:
Check hydraulic oil level and fill to 1/4″ below
the fill port as needed as stated on page 4.
Thoroughly test the Jack for proper operation.
If it does not work properly, bleed air from its
hydraulic system as stated on page 4.
SAVE THESE INSTRUCTIONS.
SAFETY
OPERA
TION
MAINTENANCE
SETUP