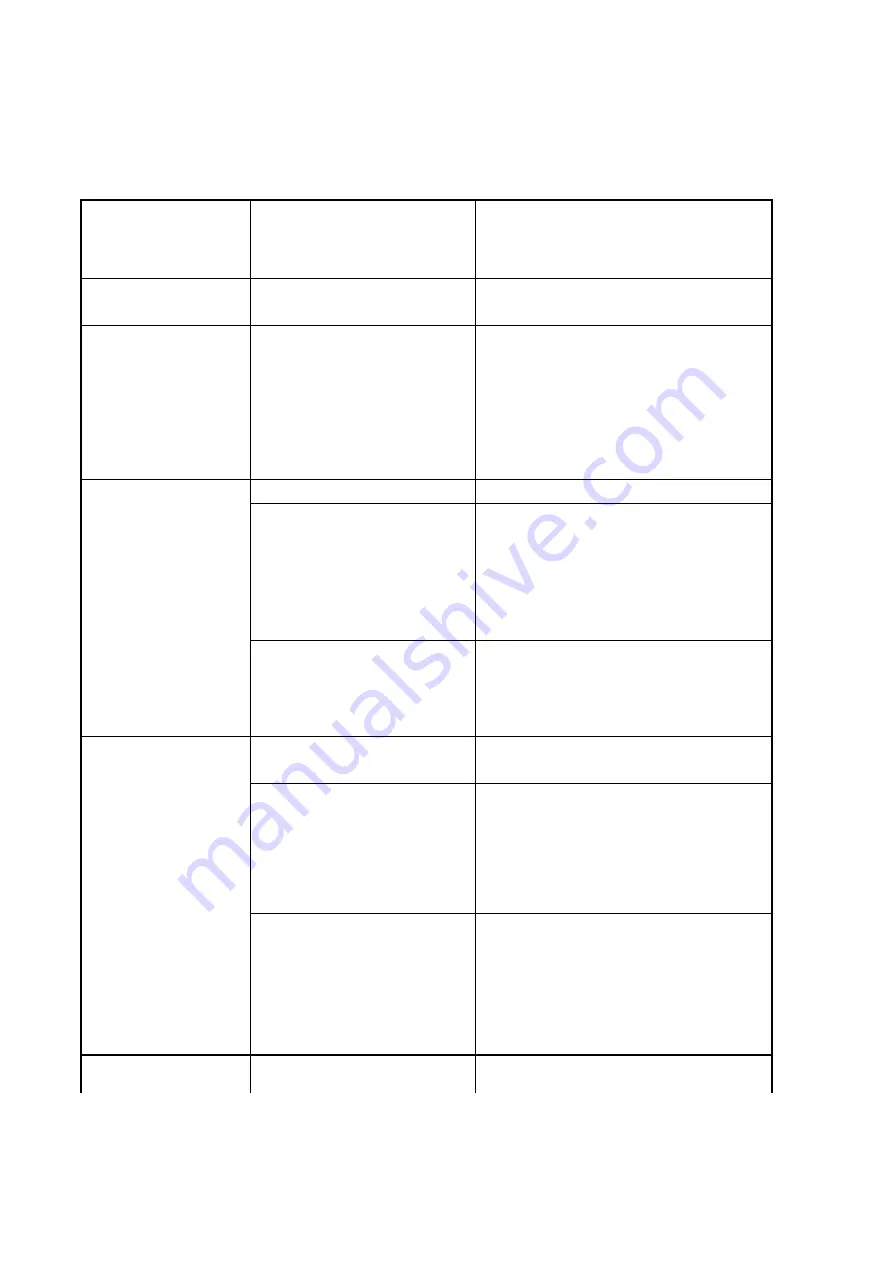
Scissor lift
Happ10
Version 4.0
©HAPP Australia Pty Ltd
Page 25
Chapter 8 Trouble shooting
A list of possible troubles and solutions is given below:
Failure Phenomena
Cause and Phenomena
Resolutions
The motor does not
Connection of power supply
wires is not correct.
Check and correct wire connection
running lifting operation.
The AC contactor in the circuit of
the motor does not pick up.
If the motor operates when forcing the
contactor down with an isolation rod, check
the control circuit. If the voltage at two ends
of the contactor coil is normal, replace the
contactor.
In lifting operation, th
motor runs, but there is
n lifting movement
The motor turns reverse.
Change the phases of the power supply
Lifting with light load is
normal ebut no lifting with
heavy load. o
The set safe pressure of the over-flow
valve may be increased by turning the set
knob right ward slightly.
The spool of the lowering solenoid valve is
stuck by dirt. Clean the spool.
The amount of hydraulic oil is
not enough.
Add hydraulic oil.
When
button, the m
lowered
press “Lower
achine is no
The safety pawl are not
released form the safety teeth.
First lift a little and then lowering
The safety pawl is not
”lifted.
The air pressure is not enough, the safety
pawl is stuck or the air pipe is broken off,
adjust pressure, check the air pipe and
replace it.
The lowering solenoid valve is
energized but does not work
Check the plug and coil of the lowering
solenoid valve and check the right turn
tightness of its end copper nut and so on.
The
machine