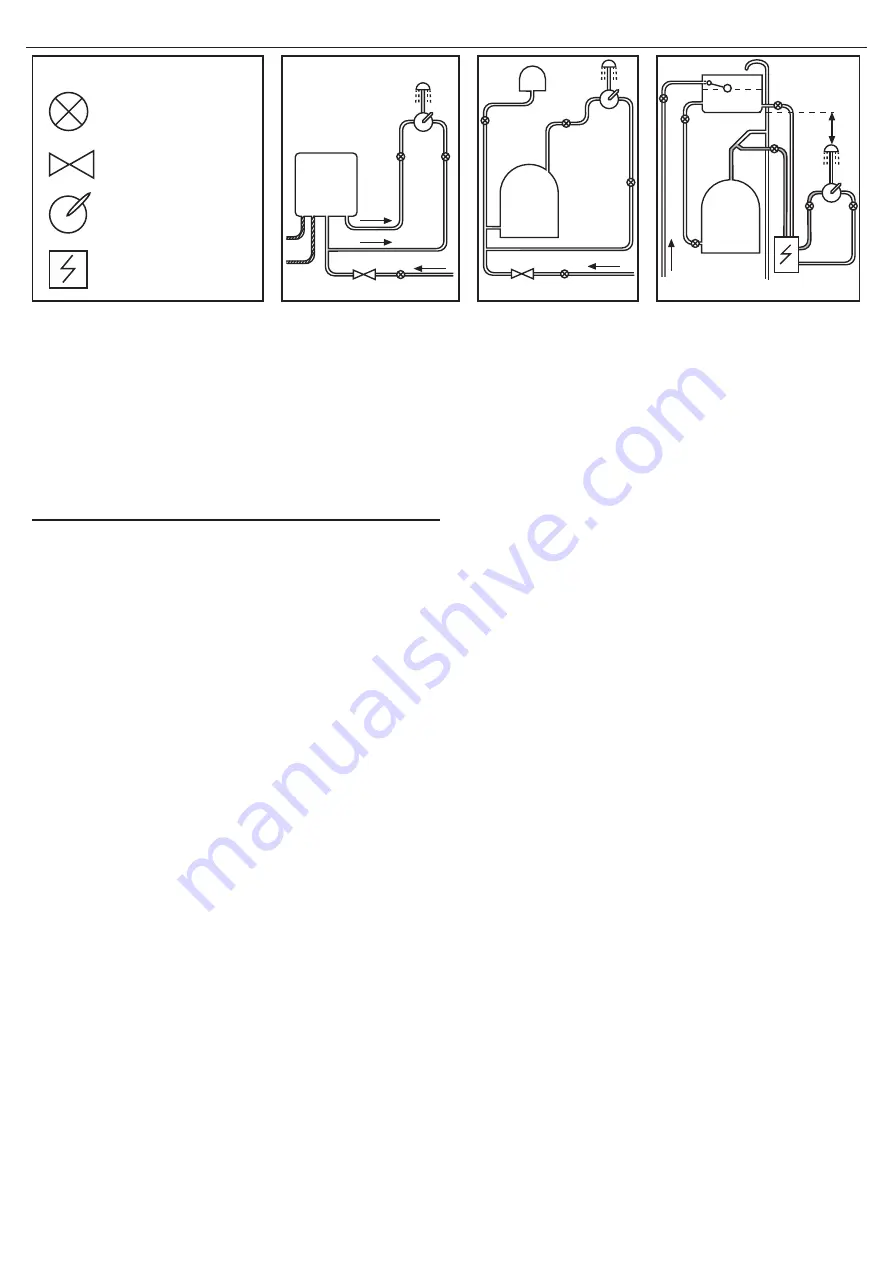
41
KEY
Isolating valve
Reducing valve
Mixer Valve
Pump
Unvented System
(pressure balanced)
22
mm
22
mm
cold mains supply
Gas Combination Boiler
(multi-point)
15
mm
15
mm
cold mains supply
Pumped System
cold
hot
hot
28
mm
22
mm
22
mm
22
mm
22
mm
cold mains supply
c) record the temperature of the mixed water at a smaller draw-off flow rate,
which shall be measured
d) isolate the cold water supply to the mixing valve and monitor the mixed
water temperature
e) record the maximum temperature achieved as a result of (d) and the final
stabilised temperature
NOTE:
The final stabilised mixed water temperature should not exceed the
values in Table A.
f) record the equipment, thermometer etc. used for the measurements
Table A: Guide to maximum stabilised temperatures recorded during site tests
Application
Mixed water tem-
perature
Shower
43°C
Washbasin
43°C
Bath (44°C fill)
46°C
Bath (46°C fill)
48°C
The mixed water temperature at terminal fitting should never exceed 46ºC.
If there is a residual flow during the commissioning or the annual verification (cold
water supply isolation test), then this is acceptable providing the temperature of the
water seeping from the valve is no more than 2°C above the designated maximum
mixed water outlet temperature setting of the valve.
Temperature readings should be taken at the normal flow rate after allowing for
the system to stabilise.
The sensing part of the thermometer probe must be fully submerged in the water
that is to be tested.
Any TMV that has been adjusted or serviced must be re-commissioned and re-
tested in accordance with the manufacturers' instructions.
In-service tests
Purpose
The purpose of in-service tests is to regularly monitor and record the performance
of the thermostatic mixing valve. Deterioration in performance can indicate the
need for service work on the valve and/ or the water supplies.
Procedure
1.
Carry out the procedure
2.
(a) to (e) on page 40 using the same measuring
equipment, or equipment to the same specifications.
2.
If the mixed water temperature has changed significantly from the previous test
results (e.g. > 1 K), record the change and before re-adjusting the mixed water
temperature check:
a) that any in-line or integral strainers are clean
b) any in-line or integral check valves or other anti-backsiphonage devices
are in good working order
c) any isolating valves are fully open
3.
With an acceptable mixed water temperature, complete the procedure
2.
(a)
to (e) on page 40.
4.
If at step
2.
(e) on page 40 the final mixed water temperature is greater than
the values in Table A and / or the maximum temperature exceeds the corre-
sponding value from the previous test results by more than about 2 K, the need
for service work is indicated.
NOTE:
In-service tests should be carried out with a frequency which identifies
a need for service work before an unsafe water temperature can result. In
the absence of any other instruction or guidance, the procedure described in
„Frequency of in-service tests“ may be used.
Frequency of in-service tests TMV3*
General
In the absence of any other instruction or guidance on the means of determining
the appropriate frequency of in-service testing, the following procedure may be
used:
1.
6 to 8 weeks after commissioning carry out the tests given in
2.
on page 40.
2.
12 to 15 weeks after commissioning carry out the tests given in
2.
on
page 40.
3.
Depending on the results of
1.
and
4.
several possibilities exist:
a) If no significant changes (e.g. < 1 K) in mixed water temperatures are
recorded between commissioning and 1., or between commissioning and
4. the next in-service test can be deferred to 24 to 28 weeks after commis-
sioning.
b) If small changes (e.g. 1 to 2 K) in mixed water temperatures are recorded
in only one of these periods, necessitating adjustment of the mixed water
temperature, then the next in-service test can be deferred to 24 to 28
weeks after commissioning.
c) If small changes (e.g. 1 to 2 K) in mixed water temperatures are recorded
in both of these periods, necessitating adjustment of the mixed water
temperature, then the next in-service test should be carried out at 18 to 21
weeks after commissioning.
d) If significant changes (e.g. > 2 K) in mixed water temperatures are re-
corded in either of these periods, necessitating service work, then the next
in-service test should be carried out at 18 to 21 weeks after commission-
ing.
4.
The general principle to be observed after the first 2 or 3 in-service tests is
that the intervals of future tests should be set to those which previous tests have
shown can be achieved with no more than a small change in mixed water
temperature.
*TMV2: The frequency of performing the in-service tests is 1 year
maximum.
Thermostatic Adjustment
Temperature Limitation
The temperature is limited by the safety stop to 40°C. If a higher temperature is
required, it is possible to over ride the safety stop by depressing the safety button.
NB.
It is recommended that for private domestic use the maximum mixed water
temperature be set at the following factory set values:
Shower Mixer 43°C
Bath/Shower 43°C
Temperatures can be set by following the procedures on page 32. This ensures
that after correct installation the outlet temperature of the water can never exceed
43°C.
To guarantee a smooth running of the thermostatic element, it is necessary from
time to time to turn the thermostat from total hot to total cold. The thermostatic
mixer valve should be checked annually by a qualified person to ensure correct
operation.
The mixer is fitted with check valves (page 36 pos. 96737000 and 93136000)
and filters (page 36 pos 96922000 and 94282000). If the water flow drops
the filters need to be cleaned. For that purpose please follow the steps 1 - 5 on
page 33.
Calibrating Thermostat
If the temperature reading is different to the showering temperature, follow the
steps 1 - 6 on page 32.
Summary of Contents for Ecostat Select 13141 Series
Page 33: ...33 1 2 3 4 5 ...
Page 43: ...43 ...