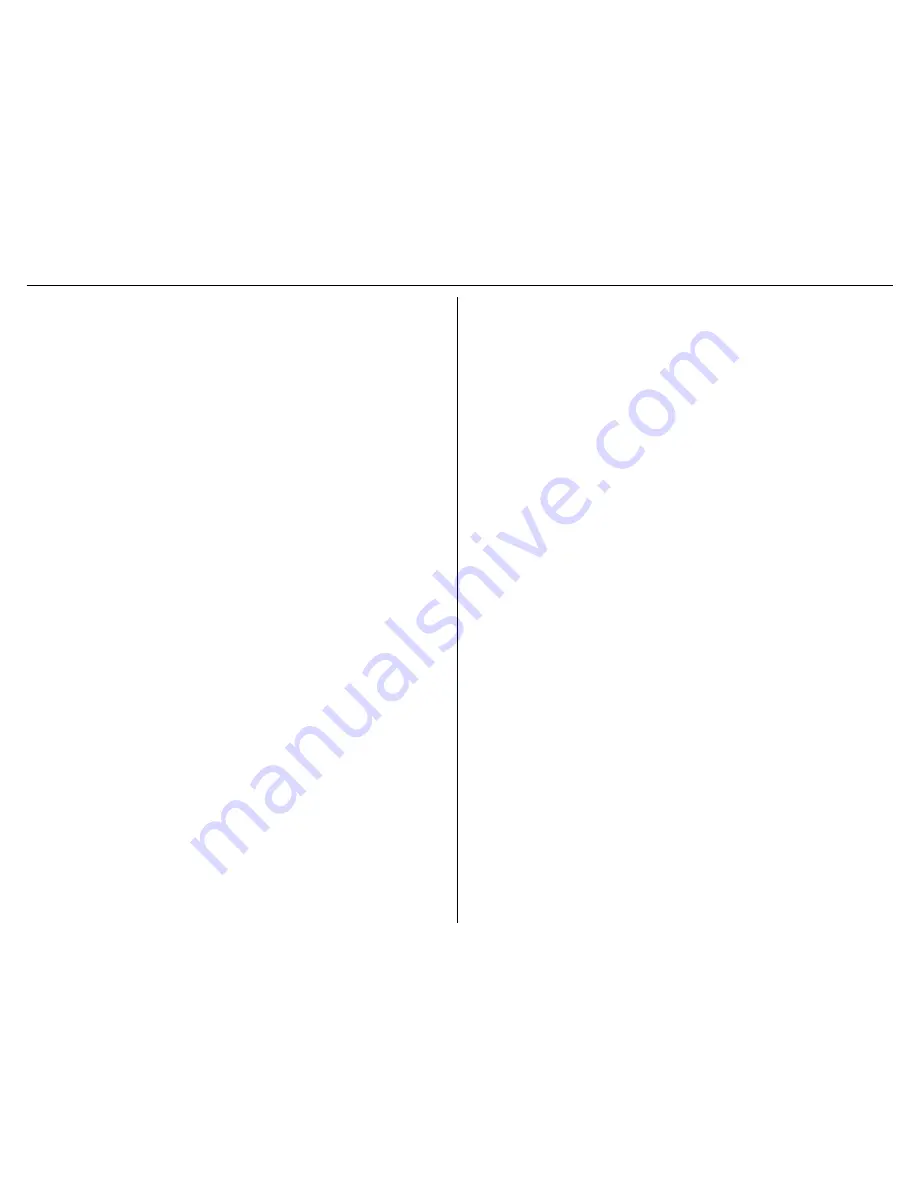
Packaged in Kit
Fuselage assembly with hatch
1
Fiberglass nose cone
1
Right wing
1
Left wing
1
Right stabilizer with elevator
1
Left stabilizer with elevator
1
Right nacelle
1
Left nacelle
1
Rudder
1
Cowling
2
Right main landing gear with screws
1
Left main landing gear with screws
1
Nose leg assembly with screws
1
Landing gear fairings (left and right)
2
Wing struts (left and right)
2
3/4 x 19 1/2 inch aluminum wing tube
1
3/8 x 11 inch aluminum stabilizer tube
1
Fuel tanks 200cc
2
2 1/4-inch white nylon spinners
2
Control Horn Bag
Small control horns
2
rudder
#4 x 1/2 in Phillips head screws
4
rudder control horns
Nylon clevises
9
steel pushrods
Snap keepers
9
steel pushrods
Silicone keepers
18
clevises
1/4-20 x 2 in nylon screws
2
wing retention
Pushrod Bag
2-56 x 4-in steel pushrod
7
ailerons and flaps
2-56 x 10-in steel pushrods
2
throttles
2-56 x 7-in steel pushrod
1
nose gear steering
Rudder Cable Bag
Rudder cable 82 inch
1
rudder cables
Copper crimps
4
Wire cable ends
2
EZ links
2
rudder servo
Main Hardware Bag
8-32 x 1-inch Allen head machine screws
6
main landing gear
#4 x 7/16-inch wood screws
3
nose cone
4-40 x 1-inch Allen head machine screws
2
strut to wing attach
8-32 x 1-inch Allen head machine screws
4
nose gear attach
Glow Engine Mount Bag
Small nylon engine mount
4
engine
6-32 x 1-inch Allen head machine screws
8
engine mount
6-32 blind nuts
8
engine mount
#6 steel washers
4
engine mount
4-40 x 1-inch Allen head machine screws
8
engine
4-40 nylon lock nuts
8
engine
#4 steel washers
16
engine
Electric Power Mount Bag
4-40 1 1/4-inch Allen head machine screws
8
motor
3/8-inch diameter x 3/4-inch nylon standoffs
8
motor
Servo Mounting Bag
10 x 11 x 20mm hardwood blocks 10
aileron and flap servos
8 x 8 x 14mm hardwood blocks
4
elevator servos
12-inch hook and loop straps
2
battery/fuel tank
4-inch adhesive-backed hook and loop tape
3
Hatch Screw Pack
#2 x 3/8-inch woodscrews (silver) 12
servo hatches
#2 x 1/4-inch woodscrews (black) 46
hatches and cowls
Included Hardware
3
Twin Otter ARF Assembly Manual