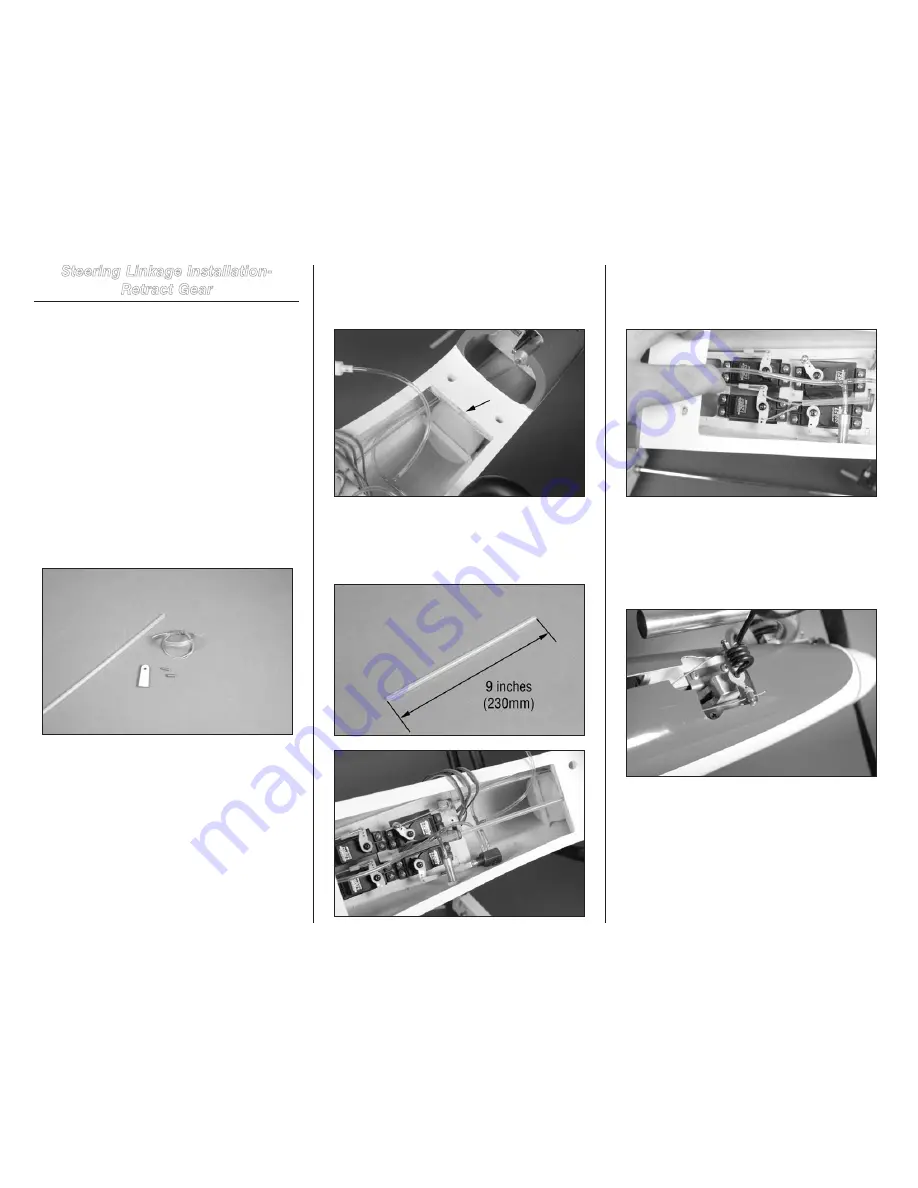
35
Hangar 9 Phoenix 7 ARF Assembly Manual
Steering Linkage Installation-
Retract Gear
Required Parts
Fuselage
Copper crimp (2)
Plywood pushrod support
38-inch (964mm) braided cable
Pushrod tube, 36-inch (914mm)
Required Tools and Adhesives
Medium CA
Crimping tool
Side cutter
Optional Tools and Adhesives
Drill
Long drill bit: 11/64-inch (4.5mm)
1. Locate the items necessary to install the steering
cables for the nose gear. You will also need to have the
fuselage at this time.
2. (Optional) Use a long 1/8-inch (3mm) drill bit to drill a
hole through the front wing bolt plate for the pushrod tube.
This will align the pushrod tube with the steering, but is
optional as it requires a long drill bit.
3. Cut the pushrod tube to a length of 9 inches (230mm).
Slide the pushrod tube in the fuselage. The plywood pushrod
support is then placed on the tube near the rudder servo as
shown. If you have not drilled the hole in the front wing bolt
plate, the guide tube will rest on the top of the plate.
4. Cut the braided cable into two 16-inch (482mm)
pieces. Slide the cables into the pushrod tube. Use two
copper crimps to secure the cables to the steering servo arm
using a crimping tool.
5. Slide the cable through the holes on the pushrod
connectors at the steering arm. After checking that the
cables are oriented so the nose wheel moves in the correct
direction, use a 3mm x 5mm machine screw to secure the
cables in the connectors. A #1 Phillips screwdriver will be
required to tighten the screw. Trim the excess cable using
side cutters.
6. Use medium CA to glue the pushrod tube where it
crosses the front wing bolt plate. Glue the plywood standoff
to the servo tray, and the pushrod tube to the standoff using
medium CA.