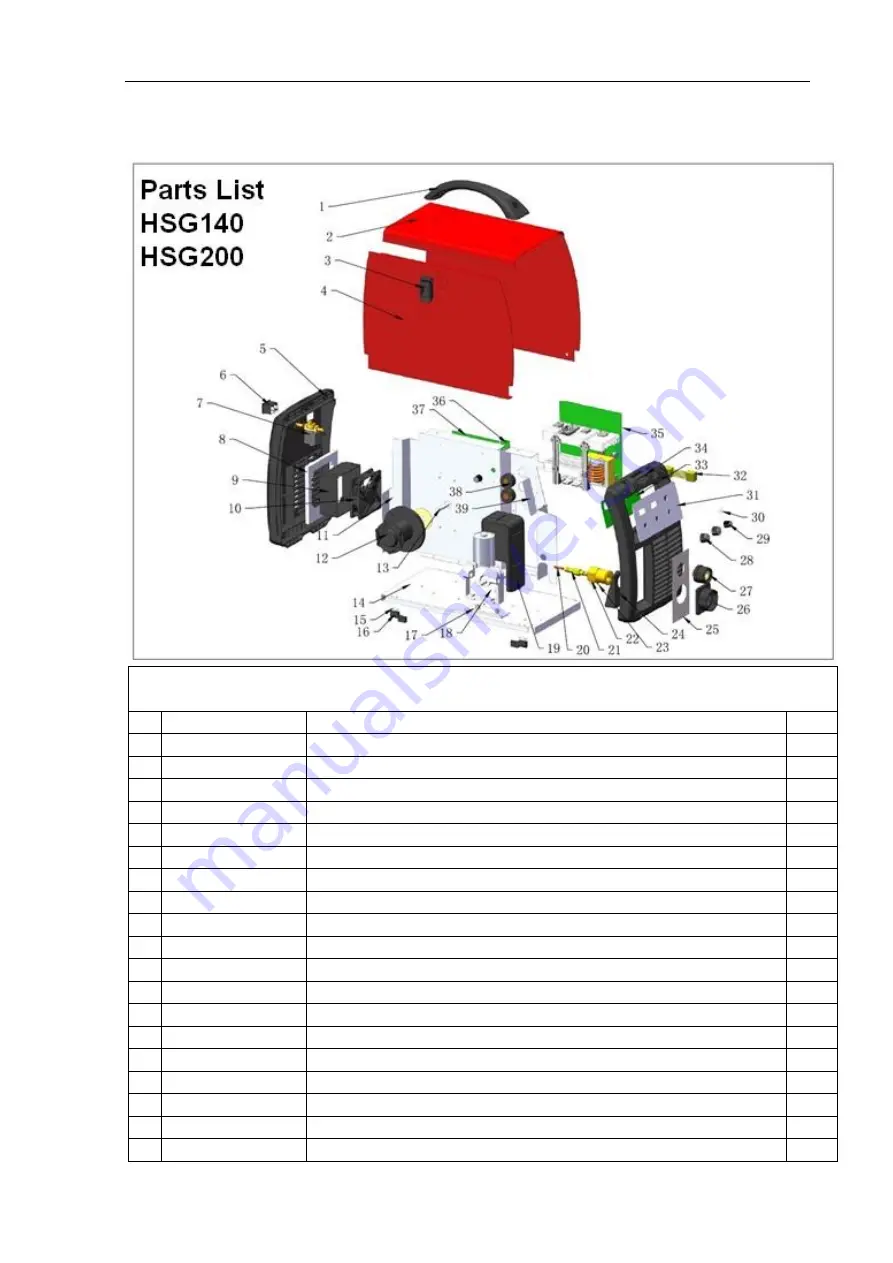
THANK YOU FOR USING OUR PRODUCTS
18
§5.5 Replacement Exploded Parts Drawing
HSG140/200 Part List
#
Part Number
Description
Qty.
1
520.3010
Handle, Machine CP
1.00
2
520.4050
Cabinet, Cover 140/200
1.00
3
520.4011
Latch, Wire Feed Door 140/200
1.00
4
520.4051
Cabinet, Wire Feed Door 140/200
1.00
5
520.4052
Cabinet, Rear Panel 140/200
1.00
6
538.0017
Power Switch
1.00
7
520.3012
Solenoid Valve, Two-Way
1.00
8
520.3053
Fan Mouting Plate CP
1.00
9
538.0055
Fan Cover CP
1.00
10
520.3013
Cooling Fan CP
1.00
11
520.3054
Cabinet Center Panel 140/200
1.00
12
520.3014
Spool Holder Assembly CP
1.00
13
520.3015
Spool Holder Shaft Assembly CP
1.00
14
520.3055
Cabinet Base 140/200
1.00
15
520.3016
Hinge Base CP
1.00
16
520.3017
Hinge Lever CP
2.00
17
520.3018
Wire Feeder Insulation Board CP
1.00
18
520.3019
Wire Feed Drive Motor 140/200
1.00
19
520.3020
Motor Cover 140/200
1.00