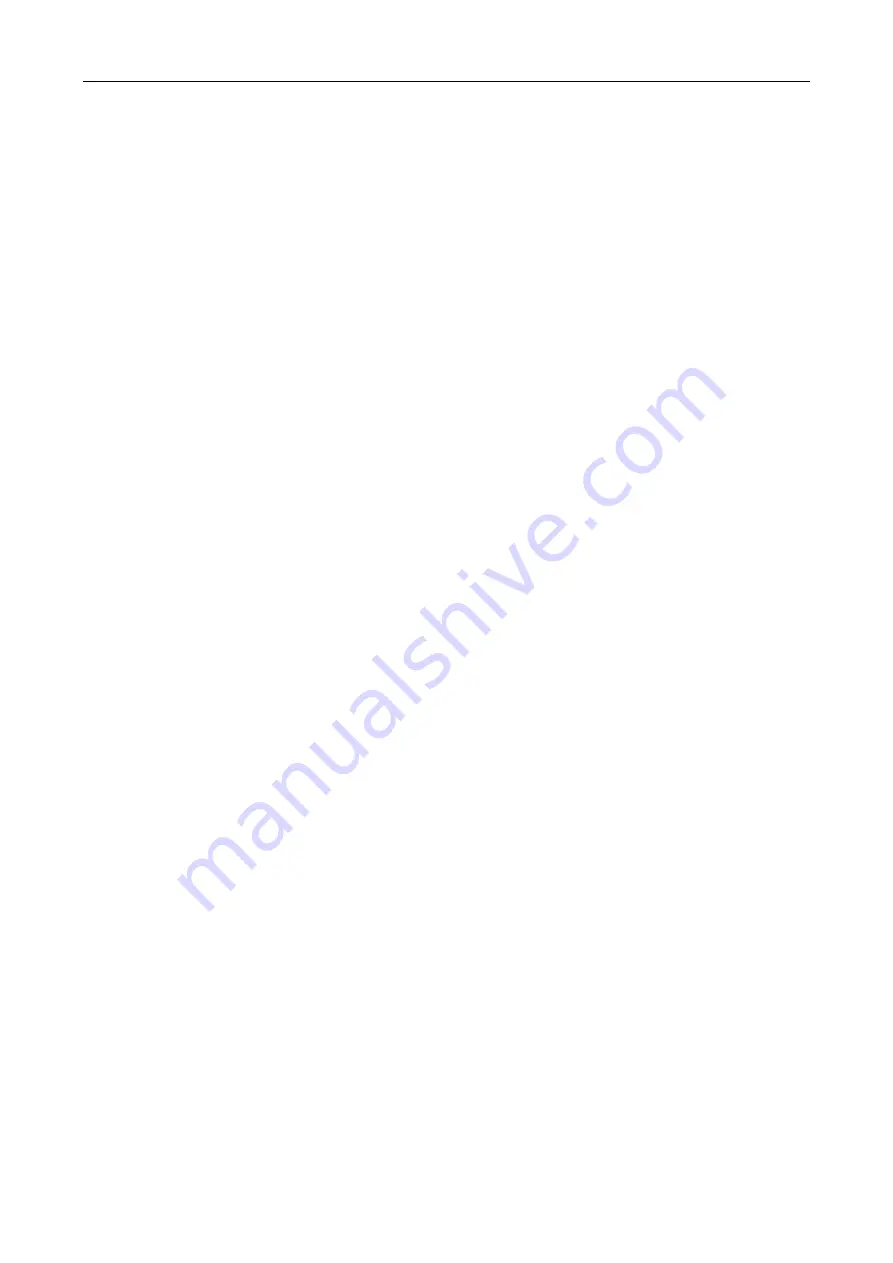
MAINTENANCE AND TROUBLESHOOTING
-
Ⅳ
-
§5.3 Maintenance of MIG Gun mechanism
§5.3.1 The operation for the MIG GUN
1. Service the wire feed mechanism at least every time the reel is changed.
·Check the wear of the feed roll groove and change the feed roll when necessary.
·Clean the welding gun wire guide with compressed air.
2. Cleaning the wire guide
Pressure of the feed rolls remove metal dust from the filler wire’s surface which then
finds its way to the wire guide. If the wire guide is not cleaned, it gradually clogs up and
causes wire feed malfunctions. Clean the wire guide in the following manner
:
Remove the welding gun’s gas nozzle, contact tip and contact tip’s adapter.
With a pneumatic pistol, blow compressed air through the wire guide.
Blow the wire feed mechanism and reel housing clean with compressed air.
Reattach the welding gun’s parts. Tighten the contact tip to spanner tightness.
3. Changing the wire guide
If the wire guide is too worn or totally clogged, change it to a new one according to the
following instructions.
Open the mounting nut of the wire guide which exposes the end of the wire guide.
Straighten the welding gun’s cable and withdraw the wire guide from the gun.
Push a new wire guide in to the gun. Make sure that the wire guide enters all the way
into the contact tip’s adapter and that there is an O-ring at the machine-end of the guide.
Tighten the wire guide in place with the mounting nut.
Cut the wire guide 2mm from the mounting nut and file the sharp edges of the cut round.
Reattach the gun in place and tighten the parts to spanner tightness.