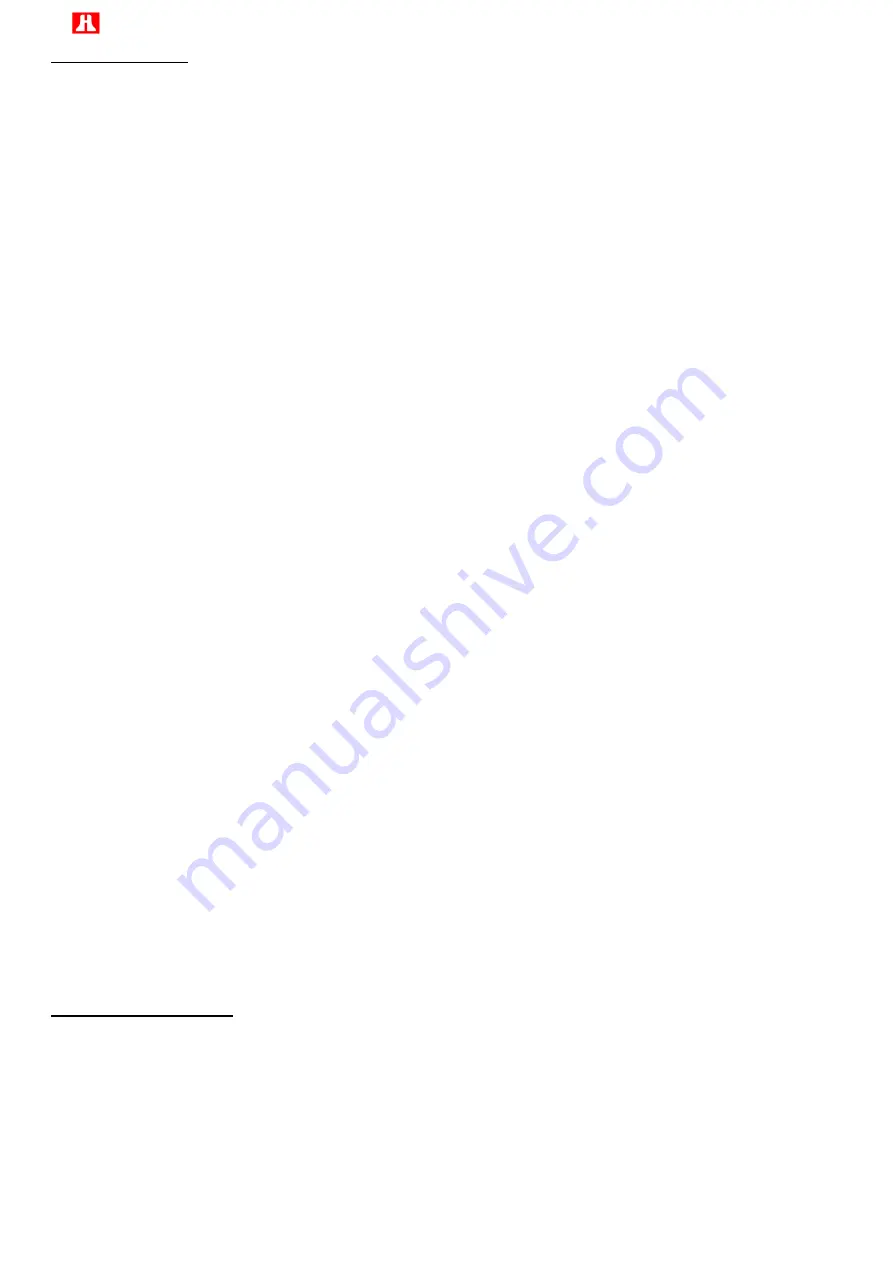
4
2.4 Design features
HANBELL screw compressors feature simple and robust construction by elimination of some components such as
pistons, piston rings, valve plates, oil pumps which are usually found in reciprocating compressors. Without these
components, screw compressors are running with minimum noise and vibration level and high reliability and durability.
HANBELL screw compressors are of two-shaft rotary displacement design with the advanced 5:6 patented screw
rotors. Screw rotors are precisely installed with roller bearings, i.e. radial bearings at both suction and discharge ends
as well as angular contact ball bearings i.e. axial bearings at discharge end. A three-phase, two-pole, squirrel-cage
dedicated induction motor drives the compressor. The motor rotor is affixed with the shaft of the male screw rotor.
Cooling of the motor is achieved with suction refrigerant vapor.
Compressor technical features:
Automatic variable volume ratio- Compressor’s Vi is adjustable, which reduce the risk of efficiency loss when the
working condition may vary at job site. Peak and off-peak operation conditions can be taken into account at the same
time. Automatic variable volume ratio ensures no loss of work in various working condition.
Variable frequency drive (VFD)
-
Variable frequency drive efficiently adjusts motor speed to match output
requirements and save energy.
Full product range- RC2-AVI series compressor consists of 11 models with displacement ranging from 140 m
3
/hr to
1775 m
3
/hr.
Multinational patents of high-efficiency screw rotors-
The new 5:6 high efficiency screw rotor profile is patented in
Taiwan, UK, US, and China. This large-volume, high-efficiency rotor profile is designed especially for modern
refrigerant characteristics. High-efficiency screw rotors are accomplished by using precise CNC machining centers,
rotor milling machines, rotor grinding machines. Quality system certified by ISO 9001 with precise measuring
equipment such as ZEISS 3D coordinate measuring machines, ensure high-efficiency, high-quality, low-noise and low-
vibration HANBELL RC2-AVI series screw compressors.
High efficiency motor- Premium grade low-loss core steel with special motor cooling slot and refrigerant guide vane
pilots the cold suction refrigerant gas going through the motor, providing high efficiency under different operating
conditions. Its winding and insulation is specially made for variable speed drive applications.
Long life bearings and high reliability- The screw compressors utilize a combination of 10 axial and radial bearings
with
α
axial balance piston to ensure longer bearing life and higher compressor reliability.
Double-walled rotor housing- Double-walled casing structure with high strength inner ribs is designed to minimize
noise and vibration level. The rotor housing is made of high-strength gray cast iron FC25 that is extremely stable.
These casings are machined by computer aided machining centers and inspected by precision measuring machines.
Direct flange-on oil separator- A vessel made of ductile material FC500 specially designed to withstand high
pressure and provide the highest efficiency of oil separation. Simple oil management, three-staged oil separator, low-
pressure-drop demister ensures the minimum refrigerant dilution in the oil and maintain high oil viscosity.
Perceptive protection modules- RC2-AVI series screw compressors are equipped with PTC thermistors and motor
protection module which can monitor discharge and motor coil temperatures. Accessories also include oil level switch
to monitor the level of oil, pressure differential switch connector, and optional pressure relief valve.
Adaptable with additional cooling- Liquid injection connectors on motor casing and the compression casing maintain
proper temperature of lubricant and prevent the compressor from overheat. Similarly, oil cooler connectors for the
external oil cooler application can reduce discharge temperature and gives better efficiency. The middle pressure
economizer connection port can be used to achieve higher refrigeration capacity and system efficiency through a sub-
cooling circuit and two-stage refrigeration expansion.
2.5 Compression process
(A) Suction and sealing:
At the beginning of the compression cycle, as the male rotor and female rotor unmesh, gas from suction port fills
the interlobe space (refer to the dark area below). Refrigerant at suction pressure continues to fill it, until the trailing
lobe crosses the suction area and the gas is trapped inside the interlobe space.
(B) Compression:
As the male rotor and female rotor mesh with each other, the interlobe space moves towards to discharge end and
its volume shrinks so that gas pressure increases consequently.
Summary of Contents for RC2-AVI Series
Page 13: ...12 4 3 Compressor outline SI mm Imperial in UNIT...
Page 14: ...13 UNIT SI mm Imperial in...
Page 15: ...14...
Page 16: ...15...
Page 17: ...16 SI mm Imperial in UNIT...
Page 18: ...17...