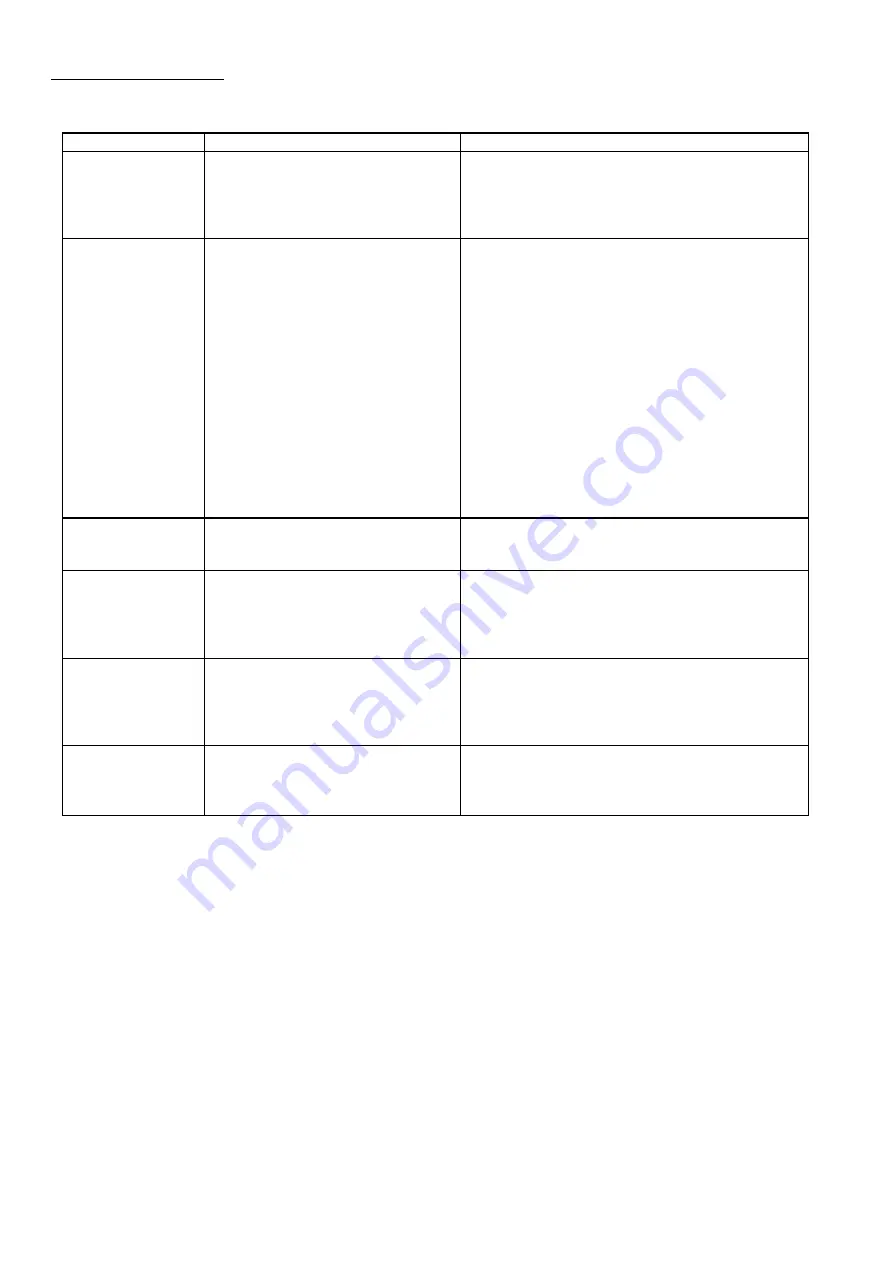
52
6. Operation and maintenance
6.1 Compressor start-up
PRE-START CHECKING- The table below shows the required procedures and checkpoints before starting the
compressor during commissioning or initial operation of the unit.
Items
Things to be checked
States or standard values
1. Accessories
1. Oil level
2. Oil heater
3. System valves status
4. Solenoid valves
1. Oil should be enough
2. Should be kept energized after the compressor’s
shutdown.
3. Opened
4. Fixed firmly.
2. Electrical system
1. Voltage of main power
2. Voltage of control circuit
3. Insulation resistance value of the
motor between phase to phase and
phase to ground.
4. Power terminals and wire
cables’
terminal connection.
5. Grounded
6. Capacity of electrical accessories
7. Settings of switches, sensors and
controllers
1. Voltage of power supply should be kept within 5
%
tolerance to the rated voltage, instant maximum
voltage drop while starting should be less than
10% tolerance to the rated voltage.
2. Standard voltage is 220V. Maximum voltage is
230V. If there is other demand, contact
HANBELL.
3. Insulation resistance value should be above
5M
Ω
4. Power terminals are firmly fixed on terminal
block and well insulated. Keep cables away from
heat source and sharpened metal.
5. Regulated by the local electricity regulations.
6. Properly selection (or required by the system
designer)
7. Proper settings (or required by system designer)
3. Piping system
1. Outer piping system
2. Leakage test
3. Bolts to fix the compressor.
1. Fixed firmly
2. No leakage
3. Fix the compressor tightly
4. Safety devices
1. Motor coil temperature sensor
(thermistor)
2. Discharge temperature sensor
(thermistor)
3. Controller
1. Connected in series with discharge temperature
sensor to INT69HBY
2. Connected in series with motor temperature
sensor to INT69HBY
3. Close circuit (no reaction)
5. VFD setting
1. Connection with controller
2. V/F, motor rated current setting
3. Acceleration / deceleration time
1. Those functions as speed control, malfunction
feedback, VFD reset should be workable
2. Should follow the nameplate of compressor
3. Acceleration: 50~60 sec from 0Hz to 50Hz;
deceleration: vice versa
6.Compressor motor
1. Motor temperature (from
Pt100/1000)
2. Liquid level (from motor sight
glass)
1. Temperature meter should be correct.
2. Lower than the upper level of sight glass.
In addition to the pre-start checking given in the above table, also consider the following:
a.
It is necessary to pay extra attention to the auxiliary facilities while commissioning the chiller at job-site and have
periodic maintenance after the initial start-up.
b.
In order to keep steady lubrication at low ambient temperature, oil heater should be energized after the
compressor shuts down to maintain oil temperature for the next start-up.
c.
Check all the settings on each pressure switch.
d.
Check if all the stop valves in the system are opened.
e.
Check the rotating direction of the compressor by starting the compressor for a transient period (0.5 to 1 sec.) and
check the suction and discharge pressure gauges. If the compressor runs rightly, the suction pressure drops and
the discharge pressure climbs immediately.
f.
Oil supply to compressor should be checked immediately after start-up. Oil flow switch is suggested so that oil
flow rate could be monitored automatically.
g.
Oil foaming may occur during starting stage. Foams should disappear afterwards when the compressor reaches
stable operating conditions. Otherwise, it indicates excessive liquid in suction gas.
h.
The running condition of the compressor after commissioning should be adjusted - discharge temperature should
be at least 10K above the saturated condensing temperature and the suction vapor superheat should be within
10K to the saturated evaporating temperature.
i.
The whole plant, especially the pipelines and capillary tubes must be checked for possible abnormal vibrations.
Contact HANBELL or local distributors if any abnormal vibrations or noise is found.
j.
Regularly check the field according to national regulations and the following items also should be checked:
Summary of Contents for RC2-1020AV
Page 15: ...4 3 RC2 AV series compressor outline drawings ...
Page 16: ...15 ...
Page 17: ...16 UNIT SI mm Imperial in ...
Page 18: ...17 ...
Page 19: ...18 ...
Page 20: ...19 ...
Page 21: ...20 ...
Page 22: ...21 ...
Page 23: ...22 ...
Page 24: ...23 ...
Page 25: ...24 ...
Page 26: ...25 ...
Page 27: ...26 ...
Page 28: ...27 ...
Page 29: ...28 ...
Page 30: ...29 ...
Page 31: ...30 ...
Page 32: ...31 ...
Page 33: ...32 ...
Page 34: ...33 SI mm Imperial in UNIT ...
Page 35: ...34 ...
Page 36: ...35 ...
Page 37: ...36 ...