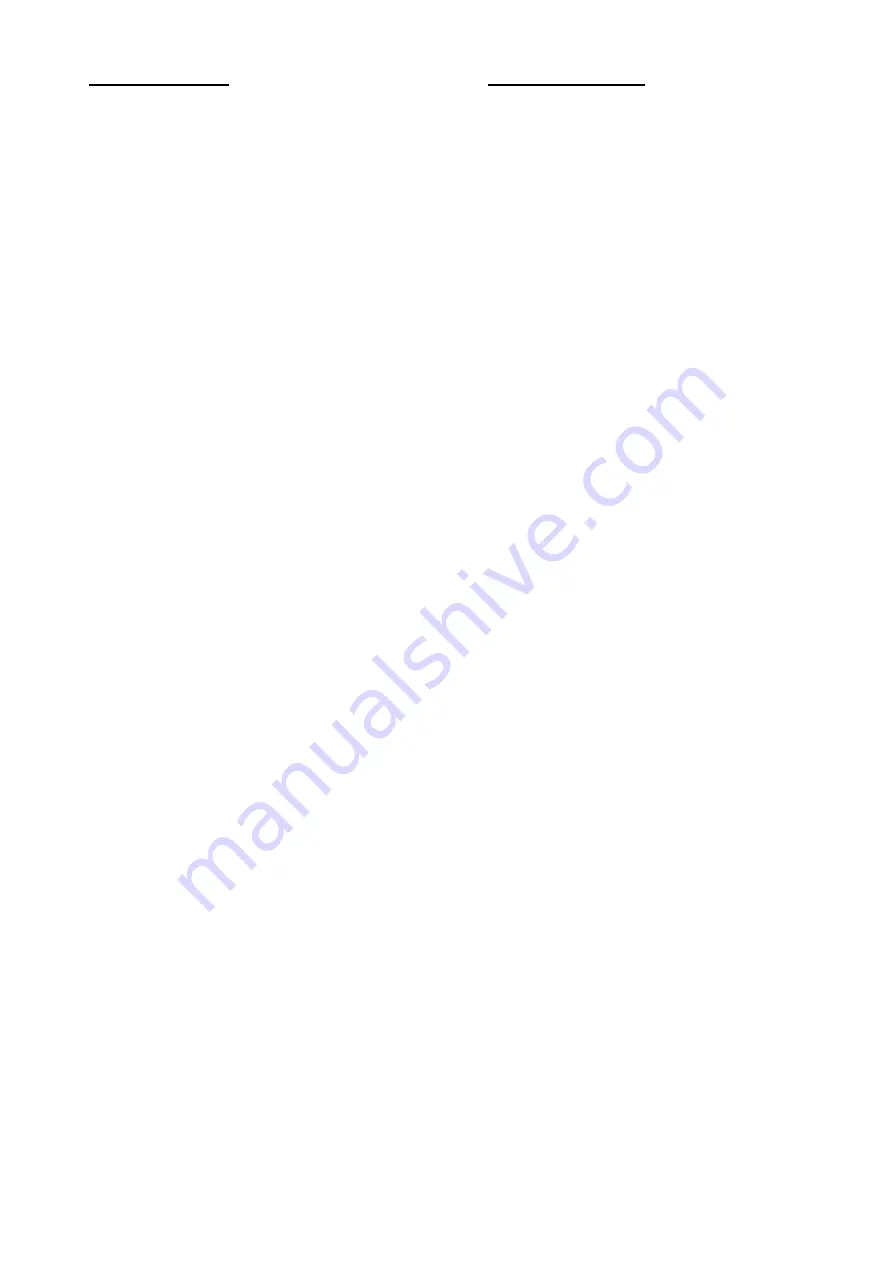
HAMWORTHY HEATING LTD
WESSEX-HE 200 BOILER
500001008/K
1
1.0 INTRODUCTION
1.1
These
instructions
are for use with Group H
Natural Gas (2nd Family) and LPG - Propane (3rd
Family). The information relative to Propane firing is
to be found in Appendix ‘A’. Boilers
MUST NOT
use
gas other than that for which they were designed and
built.
The Wessex HE is a gas fired, fan assisted, open
flued central heating/hot water boiler comprising of a
burner and water tube bank assembly (module). The
Wessex-HE 200 range consists of a single 200kW
unit and a vertically stacked double module mounted
in a common casing (Wessex-HE 400 County).
The boiler is designed for direct connection to a flue
system. Flue outlets from more than one boiler may
be connected to a single chimney, providing the rele-
vant requirements of the current Building Regulations
are adhered to. No draught diverter is fitted to the
boiler nor is a fixed diverter required in the flue sys-
tem. However a draught stabiliser is recommended
for some installations (see Section 6.1) The Wessex-
HE boiler is floor mounted and is intended for the
heating of Commercial and Industrial premises. It
may also be used to supply hot water via an indirect
cylinder.
The Wessex-HE has a low water content and water
flow rates
MUST
be maintained at or above the mini-
mum levels shown in Section 8 and Fig. 3.
1.2
This boiler must be installed and serviced by a
competent person holding “CORGI” registration or
equivalent. All installations must conform to the rele-
vant Safety and Building Regulations. HSE require-
ments must also be taken into account when install-
ing any equipment.
Failure to comply with the above may lead to Prose-
cution.
1.3
If the boiler is to be connected to an unvented
(Pressurised) heating system, care must be taken to
ensure all extra safety requirements are met and that
the relevant interlocks will shut down the boiler(s)
should a high or low pressure fault occur.
The Pressurisation unit must also incorporate a low
level water switch that protects the water pumps and
will directly or indirectly shut down the boiler plant
should a low water condition occur.
Consideration should also be given to the maximum
working pressure of the boiler as given in Section
2:
TECHNICAL DATA
. Consult Hamworthy Heating
Technical Department for help or assistance if in
doubt.
2.0 TECHNICAL DATA
The Technical Data Table relating to Propane firing
can be found in Appendix ‘A’.
2.1 Overall Dimensions
For overall dimensions and layout of the Wessex-HE
200 refer to Figure No. 9.
For overall dimensions and layout of the Wessex-HE
400 County refer to Figure No. 11.