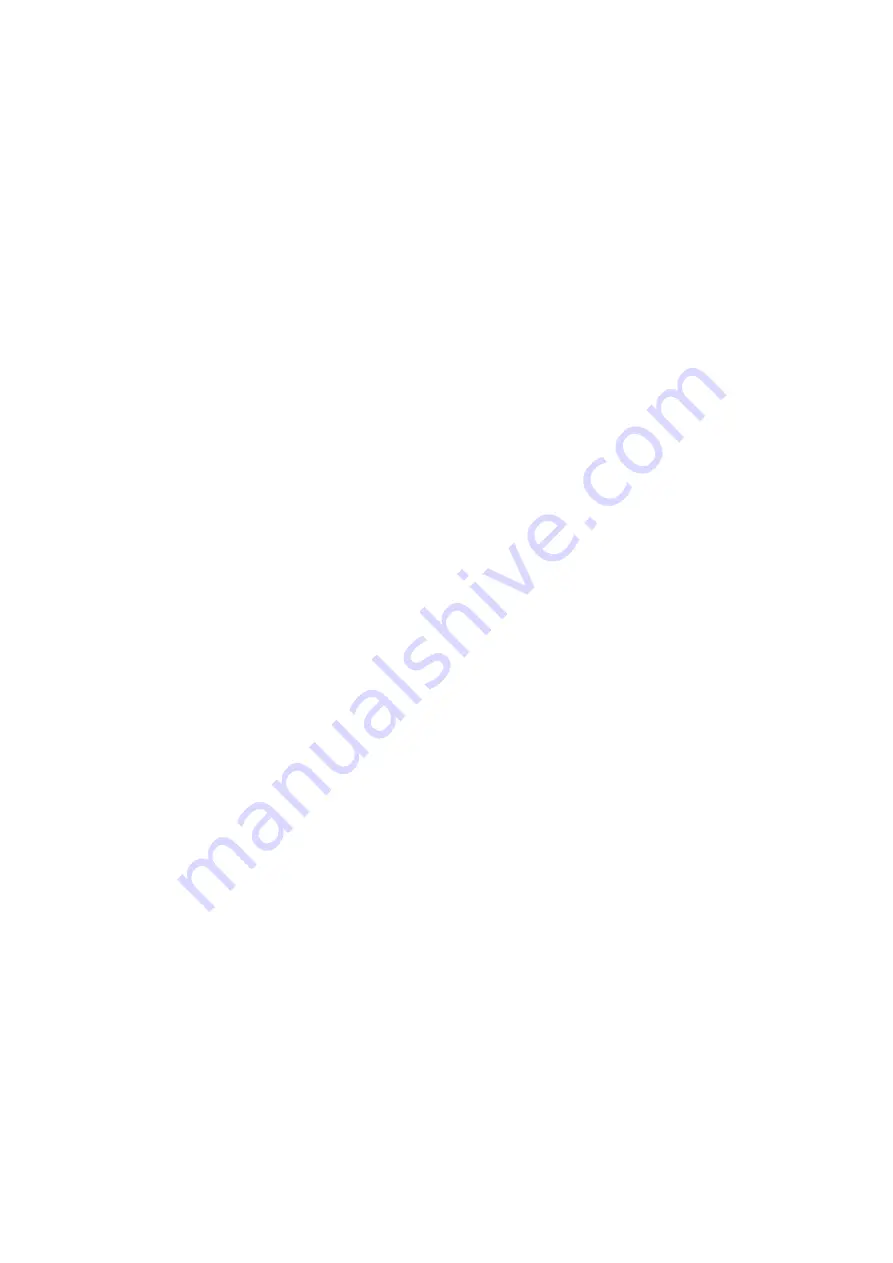
HAMWORTHY HEATING LTD
SHERBORNE
500001103/E
the controls panel to the heat exchanger, remove the
controls panel and locate it on the left hand cover
support bracket on the bottom of the wallframe.
5)
Disconnect the pressure feedback tube from the
gas valve. Remove the 4xM5 screws/nuts securing
the fan/venturi/gas valve assembly to the transition
duct.
Note
the use of a spacer on the screw/nut
nearest to the heat exchanger casting. Withdraw the
assembly from the air inlet duct. Remove the 2xM5
screws securing the venturi/gas valve assembly to
the fan. Clean the fan impellor and venturi tube with a
soft brush if necessary.
6)
Remove the 2 – M6 nuts securing the burner
assembly to the front of the heat exchanger – see
Figure 11.1 and carefully remove the burner
assembly, taking care not to damage the probes or
burner.
7)
Remove the single socket cap head screws
securing the igniter and flame probe to the burner
flange. Carefully withdraw the igniter and probe.
Remove the loose flange and Mica sight glass noting
the position for re-assembly. Check condition of the
igniter assembly and probe for damage, clean or
replace as required.
8)
Remove the 2 x M6 nuts securing the transition
duct to burner and separate the components.
9)
Check the burner and clean using a soft brush if
required (if possible use compressed air to blow out
the dust inside the burner tube). Alternatively the
burner tube can be washed using a soapy water
solution. Tap the burner flange firmly downwards on
a block of wood to dislodge any residual debris from
inside the burner tube. A damaged burner should be
replaced. (Fit the igniter and probe to the burner
flange to check the respective positions - See Figure
11.5)
Re-assemble in reverse order checking the condition
of gaskets and replace if necessary.
Refer to
Section 11, Commissioning and Testing
,
and test all gas joints broken or disturbed for
soundness before firing.
Carry out a combustion check by testing the flue gas
CO
2
and CO levels as detailed in
Section 11
.
4
.
13.3 Two Year Service
Repeat the annual service as previously described
but do not refit any components to the heat
exchanger.
To clean the heat exchanger, either ;
the sump must be removed. In the case of the S70C
model this requires the boiler to be isolated from the
system and drained down.
Or the heat exchanger must be removed from the
aluminium casing, having isolated the boiler from the
system and drained down. This is best achieved by
lifting the boiler module off the wall plate. Go to
Section 13.3.2.
13.3.1
Disengage the appliance flue connector from
the sump casting. Remove the 2xM6 screws securing
the condense trap to the sump and disconnect the
section of pipe routed back to the wall frame.
S65 Model
– support the sump from underneath and
remove the 4xM6 securing nuts. Lower the sump
casting to expose the heat exchanger and baffles.
S70C Model
- having drained the system down,
remove the return (lower) connection and heat
exchanger connecting pipe from the rear of the boiler
secured by M8 nuts and washers – see Figure 10.4.
Note
, there is an ‘O’ ring used on each fitting.
Support the sump from underneath and remove the
4xM6 securing nuts. Lower the sump casting and
secondary heat exchanger assembly to expose the
heat exchanger and baffles.
To clean the heat exchanger(s), the use of a high
pressure water hose (40-80 psi) is recommended
with the resultant discharge being collected in a
suitable receptacle.
Primary Heat Exchanger -
using the high pressure
hose, insert the cleaning nozzle into the burner
opening. Switch on the pump and traverse the full
length and circumference of the heat exchanger to
remove any deposits
Condensing Heat Exchanger -
using the high
pressure hose, traverse the exposed top and side of
the heat exchanger angling the sump to drain.
13.3.2
Should a high pressure hose not be available,
the respective heat exchanger will have to be
removed from the aluminium casing after isolating
from the flow and return water pipework. This
involves drain down and the removal of all fittings
from the rear of the boiler, secured by M8 nuts and
washers – see Figure 10.4.
Note
, there is an ‘O’ ring
used on each fitting.
Each module holds approximately 4 - 5 litres of water
and weighs 50 - 60kg (depending on model). It is
strongly recommended
that a minimum of two
people are on hand to lift the module from the wall.
Alternatively, two lifting eyes are provided for use with
suitable lifting equipment.
13.3.3
Carefully place the module onto two blocks
of wood so that the heat exchanger front casting
is supported off the floor to protect from damage.
Remove the 4xM10 nuts securing the front casting to
the aluminium casing and carefully lift the casing
vertically upwards away from the heat exchanger.
Unhook the stainless steel springs and remove the
16 stainless steel baffle plates to expose the finned
tube bank. Wire brush both sides of the baffles to
remove any deposits.
Thoroughly wire brush the finned tubes.
13.3.5
Re assemble in reverse order and refit heat
exchanger to the casing using a new gasket. Replace
the water connection gaskets on the rear of the
boiler. Re-connect the water connections using new
‘O’ rings. Carefully lift the module back onto the wall
plate and secure with the M10 nut and bolt on the left
hand side mounting. Re-fit the system pipework and
check for soundness.
29
Summary of Contents for Sherborne Series
Page 8: ...HAMWORTHY HEATING LTD SHERBORNE 500001103 E Figure 1 1 Boiler Installation Typical 2...
Page 29: ...HAMWORTHY HEATING LTD SHERBORNE 500001103 E Figure 10 6 Gas Pipe Fitting 23...
Page 45: ...HAMWORTHY HEATING LTD SHERBORNE 500001103 E NOTES 39...
Page 46: ...HAMWORTHY HEATING LTD SHERBORNE 500001103 E NOTES 40...
Page 47: ...Notes...