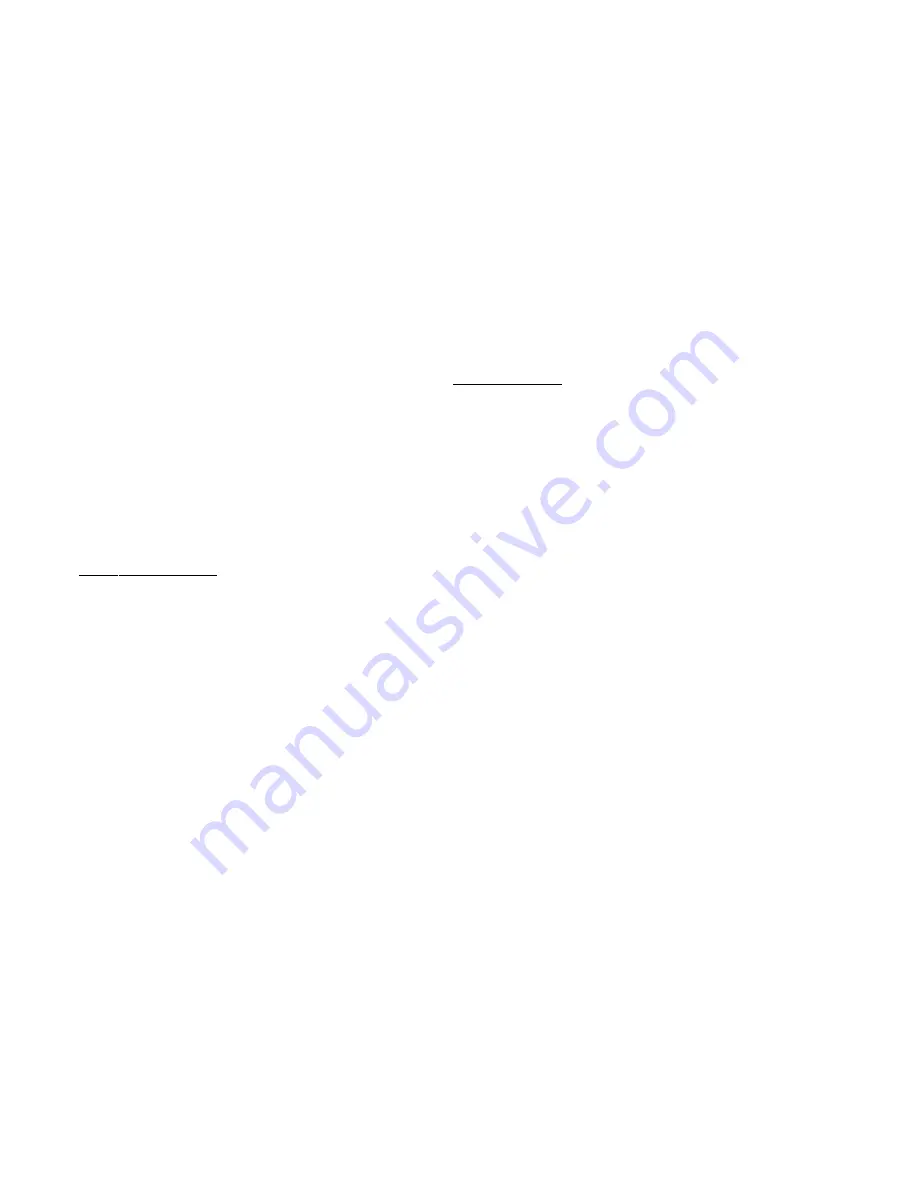
HAMWORTHY HEATING LTD. PUREWELL AUTOMATIC IGNITION 500001035/G
16
Combustion figures for Natural Gas should be as
follows: -
CO
2
= 9% volume in dry flue gas
CO
= 0-50ppm: however figure should not
exceed 200ppm under normal operating conditions.
Details of flue gas composition relating to propane
firing can be found in Appendix ‘A’.
11.8 Safety Checks
To check for correct operation of the controller, remove
A link (Terminals C1 and C2): the boiler should lockout
after approximately one second. Check that the flame
has been extinguished. Remove multi-meter and
replace wire link (Terminals C1 & C2). Wait at least
15 seconds before pressing re-set button on fascia to
re-set controller. After a waiting period the boiler will
light and run normally.
11.9 User’s Instructions
When the above is complete, the boiler owner or their
representative should be made aware of the lighting
and operating instructions fitted to the inside of the
boiler door. A practical demonstration should be given
describing each functional step. This Installer’s Guide
and User’s Instructions should then be handed over
and be kept in a safe place for easy reference.
12.0 FAULT FINDING
12.1 Safety Features Summary
Should the control thermostat fail, the temperature
limiter will trip thus creating an immediate shutdown
regardless of firing mode. An overheat neon on the
controls fascia will indicate this condition has occurred.
The door will have to be removed to permit access to
the temperature limiter re-set pin. If, after pushing
the pin in, the light on the fascia does not go out and
the boiler does not light up, it could be that the boiler
is still too hot, i.e. the control thermostat has not re-
set. An investigation should be carried out to ascertain
the reason for the overheating. An obvious reason
would be too low a water flow rate through the boiler.
The flame is under constant supervision by the burner
logic controller. This is accomplished by measuring
the flame’s ability to rectify an AC current. If the flame
diminishes for whatever reason and the rectified
current drops below the controllers minimum
(Honeywell controller minimum detection current is
0.7
u
A DC), the controller will induce a non-volatile
lockout which will require a manual re-set (situated
on the controls fascia) to re-start the control sequence.
If the boiler continues to lockout, then an investigation
must be made to ascertain the cause. See Figure
No. 17 for possible corrective scenarios.
All Propane firing boilers are fitted with a low gas
pressure switch (set at 20mbar). Should the gas
supply pressure fall below this level, the boiler
will not
operate.
12.2 Fault Finding Procedures
General fault finding is shown in Figure No. 17. If the
boiler still cannot be operated satisfactorily after following
the chart, consult your local office of Hamworthy Heating
for assistance.
12.3 Possible Causes of Boiler Lockout
1) Ignition failure due to no spark at electrode.
2) Ignition failure due to faulty gas valve.
3) Ignition failure due to broken igniter electrode or probe
lead.
4) No or low gas supply pressure.
5) No ignition due to faulty controller.
13.0 SERVICING
13.1
Regular annual servicing is recommended to ensure
trouble free operation. Although cleaning of flueways
may not be necessary on a yearly basis, it is important
that all controls and safety features are checked for
correct operation.
NOTE!
Measuring flue gas CO
2
and
gas temperatures will give an indication of the state of
the boiler flueways and waterways. Results should be
compared with previously measured values to establish
possible loss of efficiency.
13.2 Before
servicing the boiler, the following procedure
must be carried out: -
WARNING: Isolate the electrical
supply and turn off the gas service cock to the boiler
module being serviced.
1)
Remove the front casing door by using a screwdriver
to rotate the
1
/
4
turn latch.
2)
Turn off gas service cock, (fitted upstream of gas
control valve).
3)
Undo both screws on gas valve wiring plug, situated
under controls assembly, and disconnect plug completely
by pulling firmly downwards.
4)
Disconnect igniter and probe leads carefully.
(Protective boots will require pulling back to reveal
connectors.)
5)
Slacken union below gas service cock and release.
Slacken and remove nuts/washers holding gas valve and
manifold assembly. Remove manifold assembly taking
care not to damage high/low gas solenoid.
6)
Carefully remove burner assembly by pulling burner
front plate. Check condition of igniter assembly and
probe for damage. Clean as required. Check burner
bars and clean using a soft brush if required (if possible
use compressed air to blow out the dust inside the bar).
Damaged or cracked burner bars should be replaced.
To replace an individual bar will require drilling out the
rivets holding it on to the front plate. A replacement burner
bar will be supplied with clinch nuts and screws to fix
onto the front plate.
The boiler flueways can now be cleaned as follows:-