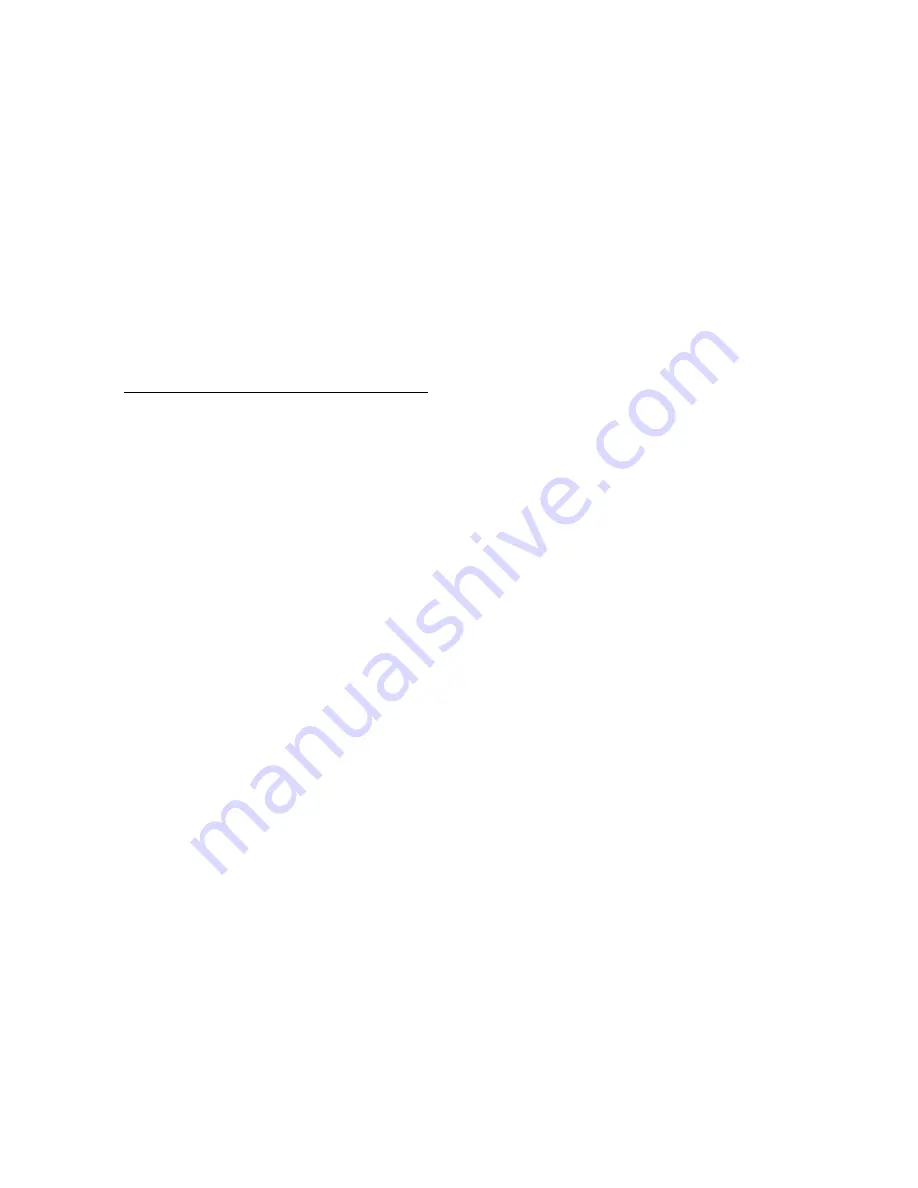
HAMWORTHY HEATING LTD. PUREWELL AUTOMATIC IGNITION 500001035/G
9
9.1
Site Wiring
Access to the controls is achieved by rotating the
1
/
4
turn
latch and removing the door. A 20mm dia. knockout is
provided in each side panel if required for electrical
connections. Any other routing of site cables should
ensure that cables do not pass close to the boiler flue
hood or that any cable trunking does not interfere with
normal air circulation and supply ducts.
A gland plate is supplied with every Purewell boiler having
two 20mm dia. holes for electrical cable anchorage. A
plug and socket arrangement is utilised for the site
terminal connections. Care must be taken to ensure
correct connections are made to the relevant terminals
before applying power.
Refer to Figure Nos. 13 & 13a for typical wiring diagrams
of standard fully automatic boiler.
10.0
BOILER ASSEMBLY AND INSTALLATION
10.1
General
Each boiler is despatched to site as follows: -
i)
Heat exchanger & basket including burners
and gas valve(s) etc. on a pallet.
ii)
Casing complete with assembly instructions.
iii) Control assembly with relevant control system.
iv) Primary flue & draught diverter. (Draught Diverter
models only)
Further details of each individual assembly are given
below: -
1)
Factory tested heat exchanger casting assembly
complete, including insulation wrap, gas valve assembly
including pre-wired plug assembly. The gas connection
pipe should be fitted to the boiler flue hood once the
heat exchanger is in place.
NOTE!
Care must be taken
to ensure no damage occurs to either insulation wrap or
gas connecting pipe.
THIS PIPE
MUST NOT
BE USED
TO MANOEUVRE OR POSITION THE BOILER.
NOTE!
Consideration must be given to the weight of the boiler
(See Figure No. 9), before lifting. It is recommended
that the boiler is moved complete with pallet and
positioned correctly. The pallet can then be dismantled
and the boiler slid into position.
2)
Casing including all screws, fasteners etc. to permit
site assembly. Instructions are included in each box to
show method of assembly. Two sizes are manufactured
these are: - Small casing for boilers up to 80kW (
NOTE!
P70 L/L utilises larger casing), large casing for boilers
from 95kW to 120kW.
NOTE!
When installing a multi-
casing set the spacing plates must be used to correctly
space the boilers approx. 3mm apart prior to fitting the
casing. (See label attached to the basket fixing.)
It is recommended that all mechanical work is carried
out prior to fitting the casing assembly, this will reduce
possible damage to the panels.
The casing assembly includes a component list, which
is also shown in Figure No. 7. You should check to
ensure that all parts are supplied prior to assembly.
3)
Controls assembly including fascia panel and
thermostats. This assembly will be suited to the
desired controls and include any optional extras
required. Refer to Figure No. 7 for fitting instructions.
Ensure all thermostat capillaries are inserted and
correctly located into the top of the boiler. The controls
assembly also incorporates a socket which matches
the gas valve wiring plug. Care must be taken to
ensure both plug and socket are correctly located and
fixed in position by the screws provided.
4)
(Standard Diverter models only)
Primary flue pipe
and draught diverter complete with casing bezel.
Instructions are supplied with the draught diverter on
how to assemble the unit, if required. These
instructions
MUST
be followed correctly and fully
complied with to ensure correct operation.
NOTE!
Ensure the baffle (Not fitted to 120kW boiler)
is positioned correctly and laying flat on the heat
exchanger before fitting the flue hood onto the boiler
(if removed).
10.2 Heat Exchanger Insulation Fitting Instructions
With reference to Figure No. 5a - Unfold blanket and
offer up to the boiler as shown. Ensure gas pipe cutout
is positioned to the left and that the ‘petals’ are
uppermost. Sit the insulation blanket onto the basket
ensuring a snug fit.