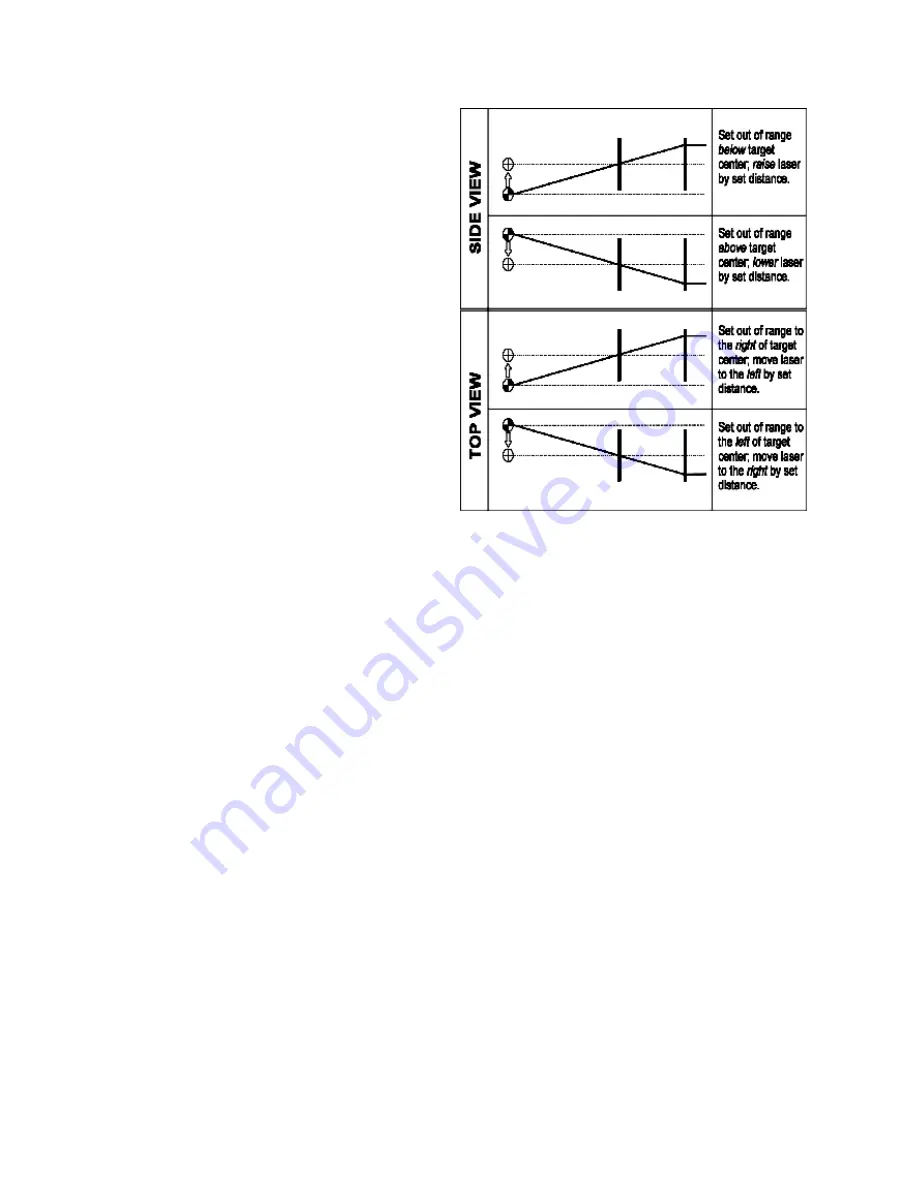
23
Once the laser beam is parallel to but offset from
the target centerline, center the beam on the near
target. The targets should give the same reading,
both number and sign, for both axes (horizontal
and vertical). If not, refigure the set and buck in
again. In most cases, remote buck-in can be
accomplished in two or three passes. This method
will work even when L1 is much greater than L2,
or when the beam does not even hit the target (in
such cases the far reading can be taken by using a
ruler to measure the beam's distance from the
target center).
The determining factor for which method to use
can be summed up as follows:
•
Use Normal Buck-in if the distance from the
laser to the first target is less than one-tenth of
the distance between the two targets. When
using normal buck-in, the rule is:
Zero Near,
Point Far
. Buck in the laser beam by zeroing
it on the
near
target, and then "pointing" the
laser beam using the appropriate adjustment
knobs to
center
on the far target. The two steps
are repeated until both targets show zero
readings.
•
Use Remote Buck-in if the distance from the laser to the first target is more than one-tenth of the
distance between the two targets, or if normal buck-in method is not effective. When using remote
buck-in, the rule is:
Point Through Zero to Set
. Zero the near target, determine the set point (making
sure the sign is correct), and adjust the laser beam using the appropriate adjustment knobs to point to
set rather than zero on the far target. Repeat if necessary, until both targets read zero. The laser beam
is now bucked in to the reference points defined by the two targets.
Figure 17 -
Moving the laser when the set point is out of range of the
target cell