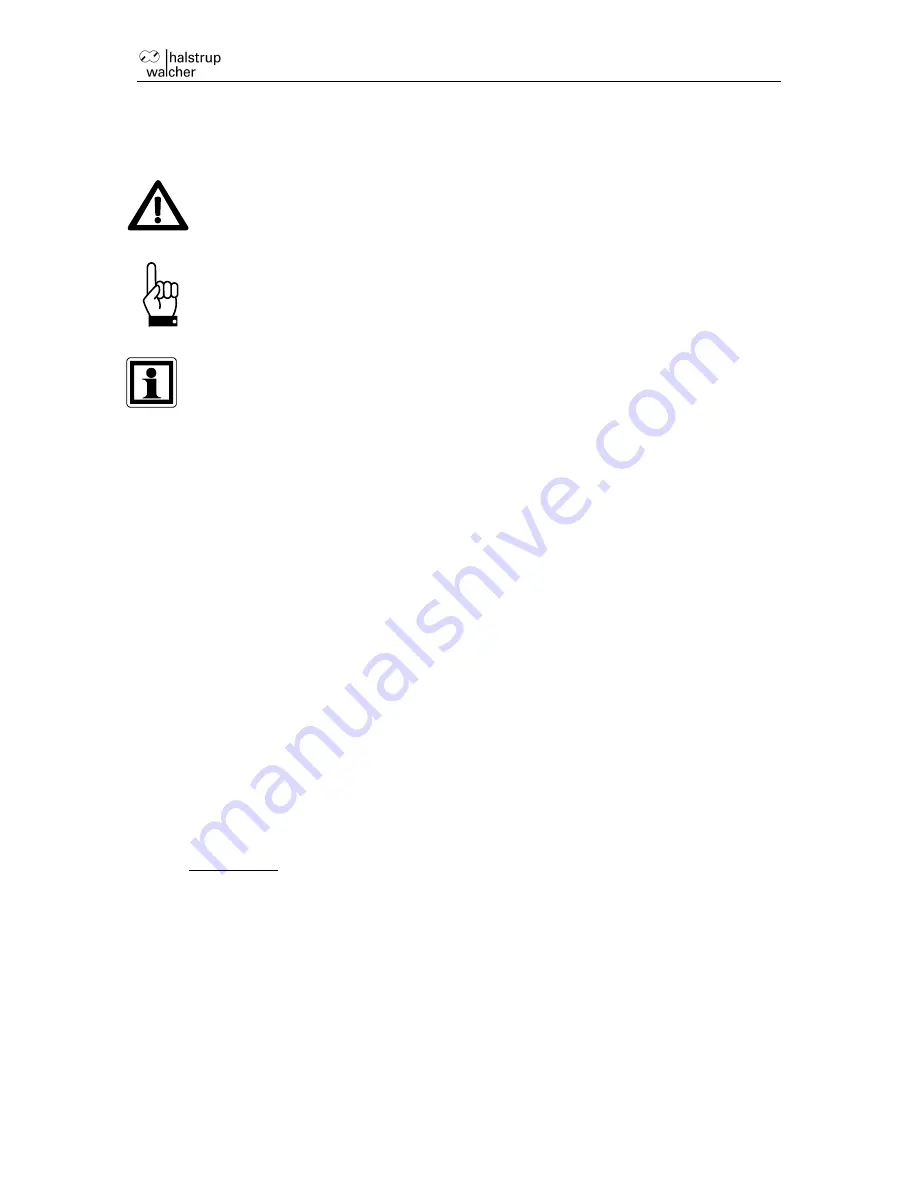
PSx3xxDN Instruction Manual
5
1.4 Symbols
The symbols given below are used throughout this manual to indicate instances when
improper operation could result in the following hazards:
WARNING!
This warns you of a potential hazard that could lead to bodily injury up
to and including death if the corresponding instructions are not followed.
WARNING:
This warns you of a potential hazard that could lead to significant
property damage if corresponding instructions are not followed.
INFORMATION:
This indicates that the corresponding information is important
for operating the device properly
2
Device description
2.1
Features
The PSx3xxDN positioning system, an intelligent, compact, complete solution for
positioning auxiliary and positioning axes, consists of an EC motor, gear power
amplifier, control electronics, absolute measuring system and DeviceNet interface.
The integrated absolute measuring system eliminates the need for a time-consuming
reference run. Connecting to a bus system simplifies the wiring. A hollow shaft with
adjustable collar makes assembly quite simple. The positioning system is especially
suitable for automatically setting tools, stops or spindles for wood-processing
equipment, packing lines, printing equipment, filling units and other types of special
machines.
PSx3xxDN positioning systems convert a digital positioning signal into an angle of
rotation.
2.2
Installation
Hollow shaft:
The PSx3xxDN is mounted onto the machine by sliding the hollow shaft of the
positioning gear onto the axis to be driven and then securing it with an adjustable
collar (recommended diameter of the axis is either 8h9 or 14h9; wrench torque for
screw: 1.5Nm). The adjustable collar should be tightened only just to the point where
it can no longer rotate freely.
Securing the pin under the hollow shaft into an appropriate bore will prevent further
rotation.\line (see drawing)