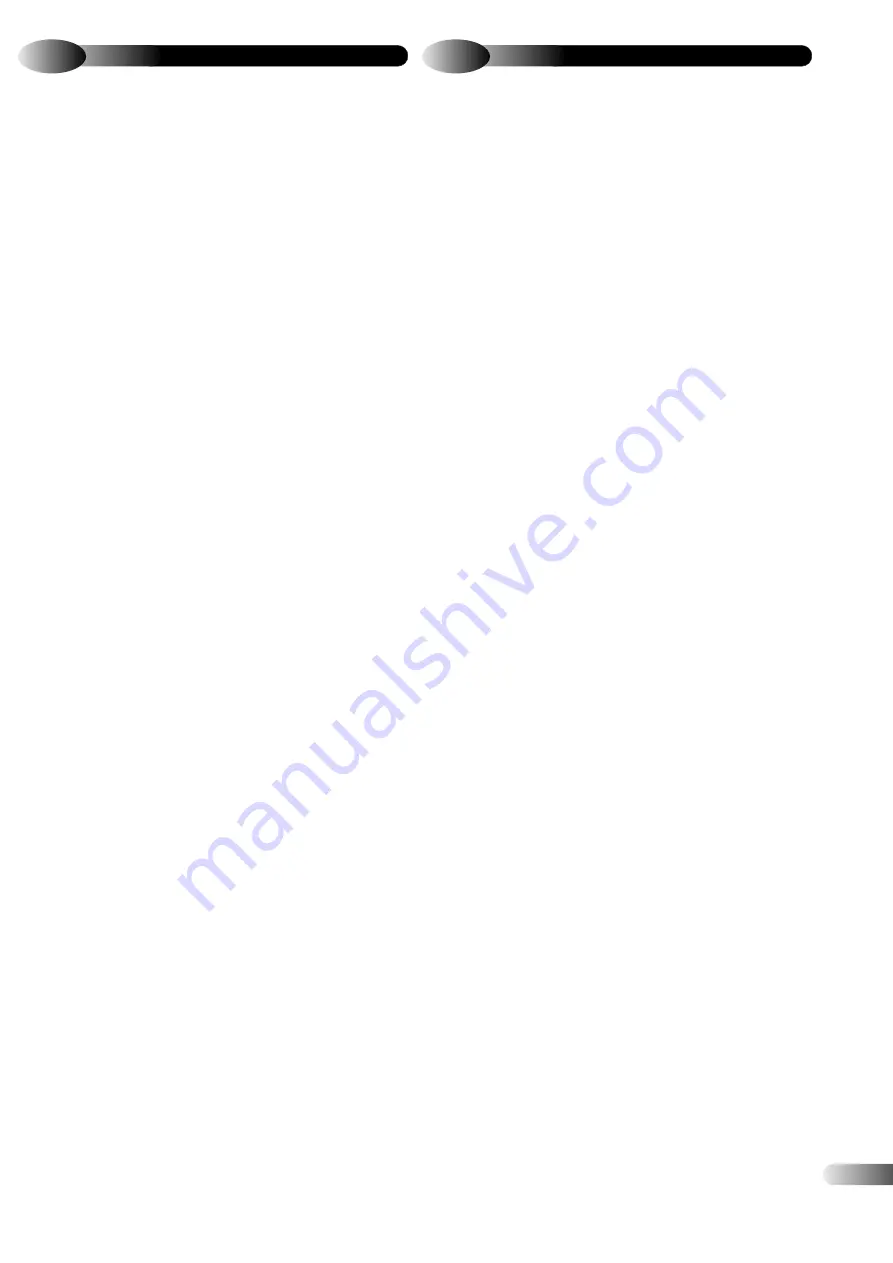
1
IT IS A ST
ATUTORY REQUIREMENT THAT ALL GAS
APPLIANCES ARE INSTALLED BY COMPETENT PERSONS,
(i.e. CORGI REGISTERED INSTALLERS) IN ACCORDANCE
WITH THE GAS SAFETY (INSTALLATION AND USE)
REGULATIONS (CURRENT EDITION). FAILURE TO
COMPLY WITH THESE REGULATIONS MAY LEAD TO
PROSECUTION.
This appliance has been tested and cer
tified in order to satisfy the
necessary European Directives and comply with the latest Building
Regulations, including the efficiency requirements of the SEDBUK
scheme.
Gas Appliance Directive
90/396/EEC
Efficiency of Hot Water Boilers Directive
92/42/EEC
Low Voltage Directive
93/68/EEC
Electromagnetic Compatibility Directive
92/31/EEC
No modifications to this appliance should be made unless they
are fully approved by the manufacturer.
Appliance installation must be carried out by a competent person
and must be in accordance with the current legislation in force at
the time of installation, in the country of destination.
The manufacturer’s instructions must not be taken as overriding
any statutory requirements.
GAS LEAKS. DO NOT OPERA
TE ANY
ELECTRICAL SWITCHES, OR USE A NAKED
FLAME. TURN OFF THE GAS SUPPLY.
VENTILATE THE AREA BY OPENING DOORS AND
WINDOWS. CALL OUT YOUR LOCAL GAS SUPPLIER.
Control of Substances Hazardous to Health
Under Section 6 of the Health and Safety at W
ork Act 1974, it is
required to provide information on substances hazardous to health.
The adhesives and sealants used in this appliance are cured and
give no known hazard in this state.
Insulation Pads – These can cause irritation to skin, eye and the
respiratory tract. If you have a history of skin complaint you may be
susceptible to irritation. High dust levels are usual only if the
material is broken. Normal handling should not cause discomfort,
but follow normal good hygiene and wash your hands before
eating, drinking or going to the lavatory. If you do suffer irritation to
the eyes or severe irritation to the skin seek medical attention.
Gas and Electricity Consumer Council (Ener
gywatch)
Ener
gywatch is an independent organisation, which protects the
interests of gas users. If you need advice concerning energy
issues, they may be contacted on their consumer help line
number: 08459 060708, or via their web site;
http://www.energywatch.org.uk.
This appliance incorporates a microprocessor based, fully
modulating air/gas ratio control system with direct burner
ignition, which provides a modulated heat output to central
heating (CH) demands, with internal frost protection provided as
standard. The heat exchanger is constructed from stainless steel
encased in high temperature polymer.
A combined circulating pump and automatic air vent assembly,
pressure gauge, safety valve and system expansion vessel are
included. Isolation valves are fitted to the service connections.
This appliance may be used with any certified mains voltage room
thermostat, and can operate without the need for an automatic
bypass valve, however if thermostatic radiator valves are installed
it is recommended that one radiator is fitted with lockshield valves,
to allow the pump overrun facility to operate correctly. A separate
CH expansion vessel is not required if the total CH system content
is less than 84 litres, but one is required for systems with volumes
greater than 84 litres; refer to section 3.7.
It is recommended that a drain cock is fitted at the lowest point in
the system.
1.1
IMPORTANT INFORMATION
1.2
GENERAL DESCRIPTION
!