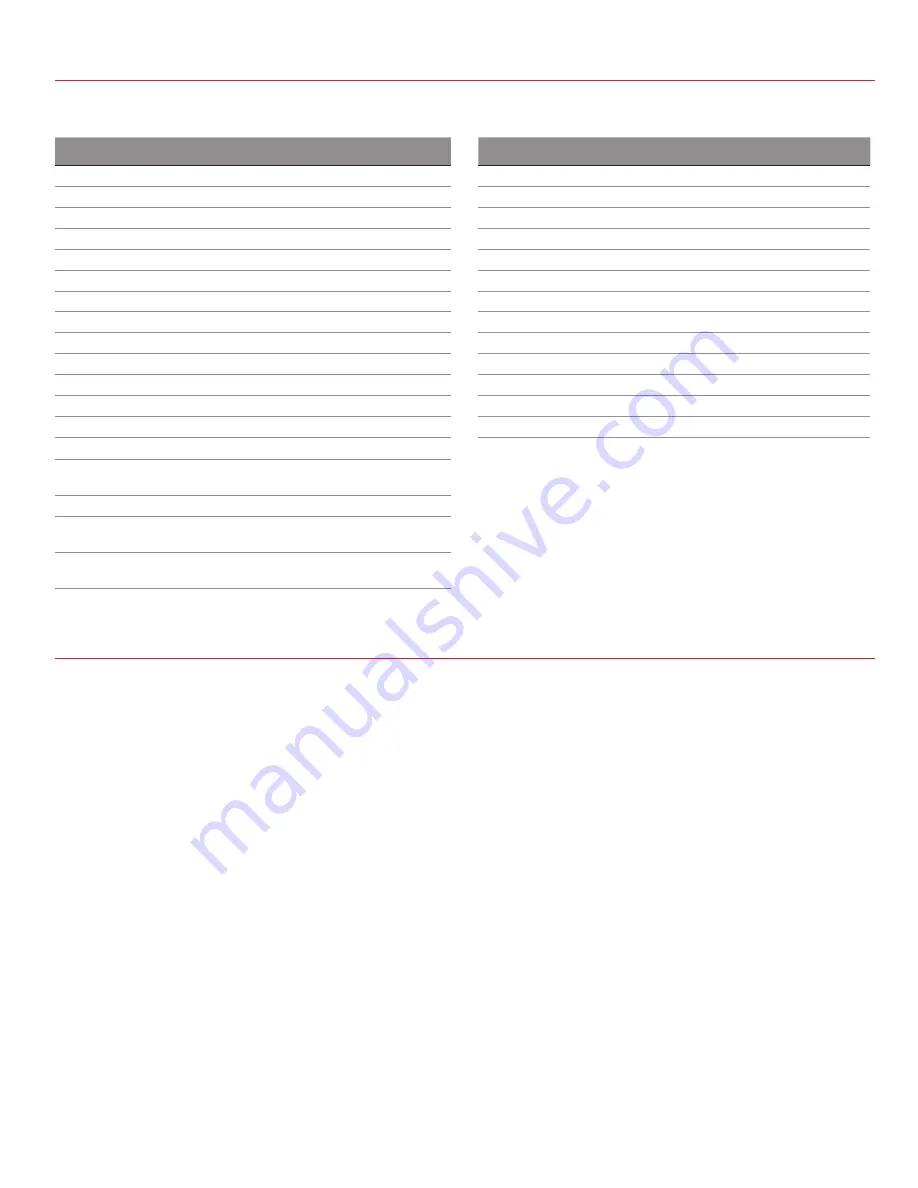
Modbus RTU
January 2023
•
Rev. 0
• Standard Devices User Manual
34
Writing Control and Configuration Information
All command and control requests to a Device are issued with Modbus function code FC16: “write multiple registers”.
Status Flags
Modbus Reading and Status Registers
Devices
Interpretation
Bit
Devices
Access
Register
Parameter
Mass Flow and Liquid
Temperature Overflow (TOV)
0
All
Read/Write
1000
Command ID
Mass Flow and Liquid
Temperature Underflow (TOV)
1
All
Read/Write
1001
Command Argument
Mass Flow and Liquid
Volumetric Overflow (VOV)
2
Controllers
Read/Write
1010–1011
Setpoint
Mass Flow and Liquid
Volumetric Underflow (VOV)
3
Mass Flow
Read/Write
1050
Mixture Gas 1 Index
Mass Flow
Mass Overflow (MOV)
4
Mass Flow
Read/Write
1051
Mixture Gas 1 Percent
Mass Flow
Mass Underflow (MOV)
5
Mass Flow
Read/Write
1052
Mixture Gas 2 Index
All
Pressure Overflow (POV)
6
Mass Flow
Read/Write
1053
Mixture Gas 2 Percent
Mass Flow and Liquid
Totalizer Overflow (OVR)
7
Mass Flow
Read/Write
1054
Mixture Gas 3 Index
Controllers
PID Loop in Hold (HLD)
8
Mass Flow
Read/Write
1055
Mixture Gas 3 Percent
All
ADC Error (ADC)
9
Mass Flow
Read/Write
1056
Mixture Gas 4 Index
Dual Valve Controllers
PID Exhaust (EXH)
10
Mass Flow
Read/Write
1057
Mixture Gas 4 Percent
Custom OPL devices
Over pressure limit (OPL)
11
Mass Flow
Read/Write
1058
Mixture Gas 5 Index
Mass Flow and Liquid
Flow overflow during totalize (TMF)
12
Mass Flow
Read/Write
1059
Mixture Gas 5 Percent
All
Measurement was aborted
13
Mass Flow
Read/Write
1200
Gas Number
All
Read
1201–1202
Status Flags
(next table)
All
Read
1203–1204
Pressure Statistic
Mass Flow
and Liquid
Read
1205–1206
Flow Temperature
Mass Flow
and Liquid
Read
1207–1208
Volumetric Flow
Mass Flow
Read
1209–1210
Mass Flow
Special Commands
You can access special control functions on devices with an
FC16 write to registers 1000–1001. Special commands consist
of a Command ID and a Command Argument written in a
single pass to these registers. Each command/argument pair
issues as a set of two 16-bit unsigned integers. Commands
start by a write to register 1000. If you send a command to
register 1000 without sending an argument to 1001 the device
will interpret the command with a default argument of 0.
At any time after sending a special command to registers
1000..1001 you can perform a read of the same registers
to determine the success or failure of the last command.
Register 1000 will store the last Command ID sent to the
device, and register 1001 will return a status code indicating
the command result.
Custom Gas Mixtures
Custom gas mixtures can be saved with 2–5 gases using the
mix registers 1050–1059. This does not instruct the device to
mix the gas, it programs it to be able to measure a premixed
custom gas blend.
Saving the mix is a two-step process. First, the desired
constituent gas indexes and percentages must be written
to the mix registers (1050–1059). Then, a write of the
Create
Custom Gas Mixture
command (ID 2) into command register
1000 (with the command argument being optional).
Gas mix percentages are interpreted as integer hundredths
of a percent and the total percentage must sum to 100%. For
example, to specify a mix of 50%, a value of 5000 is written
into the gas percentage register.
The mix is performed with the first N gases that have a non-
zero percentage. As an example, if you wish to use a mixture of
3 gases, write the index and percentage for those gases into
registers 1050–1055 and write a value of zero into 1057–1059.
If the command argument is 0 or is omitted, the custom gas
mixture is allocated in the next empty gas mix index starting
at 255 and working down to 236. If no user mix indexes are
available, the command fails and an error is returned in the
command argument register.
To specify which index to write the custom gas mixture to, use
a command argument between 236 and 255. The specified
index either creates or updates to the new composition. If the
specified index is not valid (the command argument is neither
0 nor 236–255), an error is returned.
Upon completion, the command argument register is updated
with the new mixture. If the mix is valid, the index of the mixed
gas is returned. If one of the requested mix gas constituents
did not exist, or the percentage does not add to 100%, an
error value is returned and the mixture is not saved.
All gas mixtures are accessible via Gas Select™ on the front
panel.