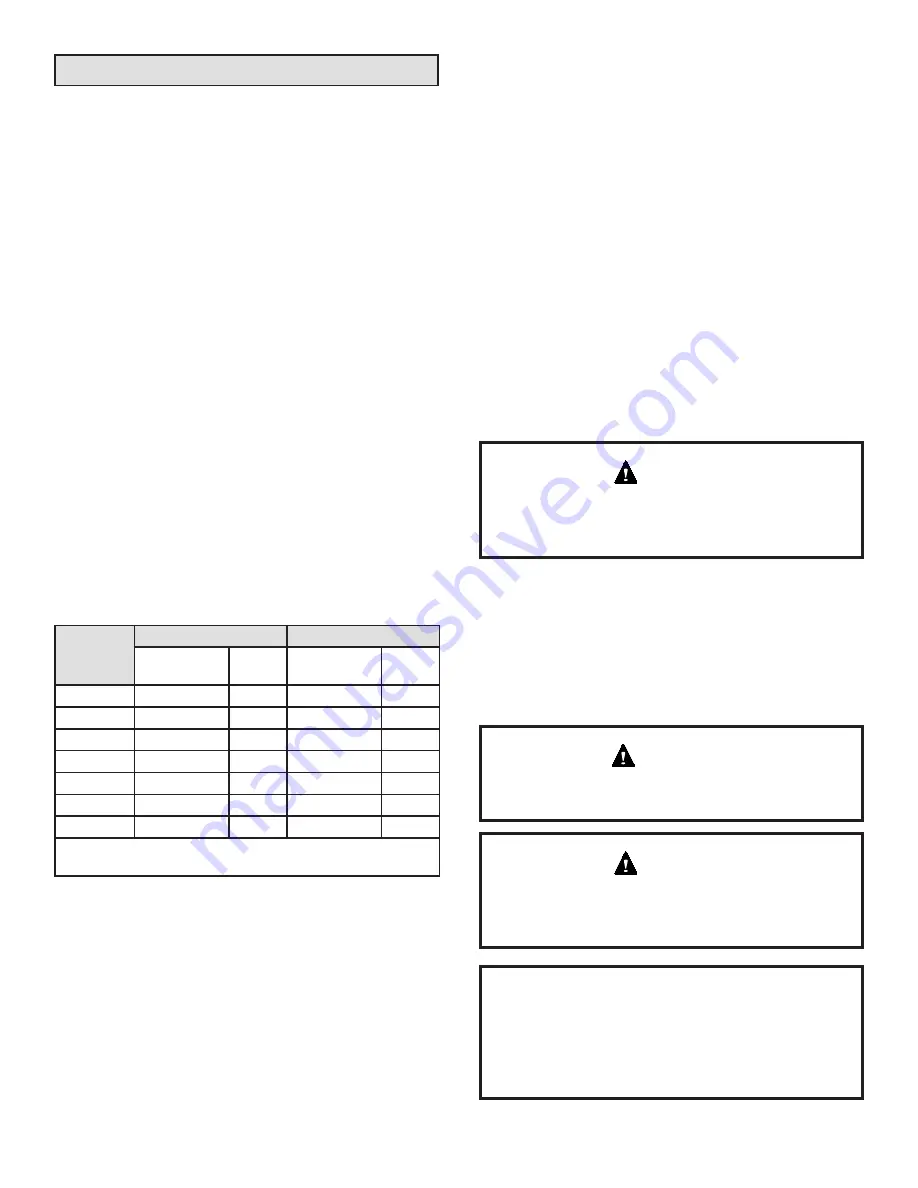
Page 10
31-5000752 Rev. 0
Filter Drier
The filter drier is very important for proper system operation
and reliability. If the drier is shipped loose, it must be
installed by the installer in the field. Unit warranty will be
void, if the drier is not installed.
Installation of Line Sets
DO NOT
fasten liquid or suction lines in direct contact with
the floor or ceiling joist. Use an insulated or suspension
type of hanger. Keep both lines separate, and always
insulate the suction line. Liquid line runs (30 feet or more)
in an attic will require insulation. Route refrigeration line
sets to minimize length.
DO NOT
let refrigerant lines come in direct contact with
foundation. When running refrigerant lines through the
foundation or wall, openings should allow for a sound
and vibration absorbing material to be placed or installed
between tubing and foundation. Any gap between
foundation or wall and refrigerant lines should be filled with
a vibration damping material.
If ANY refrigerant tubing is required to be buried by state
or local codes, provide a 6 inch vertical rise at service
valve.
CAUTION
Flushing Line Sets
If the unit will be installed in an existing system that uses
an indoor unit or line sets charged with R-22 refrigerant,
installer must perform the following flushing procedure.
NOTE:
Existing system components (including line set
and indoor coil) must be an AHRI match with the unit in
order to fulfill unit warranty requirements.
Refrigerant must be reclaimed in accordance with
national and local codes.
WARNING
Do
NOT
attempt to flush and re-use existing line sets
or indoor coil when the system contains contaminants
(i.e., compressor burn out).
CAUTION
“Clean refrigerant” is any refrigerant in a system that
has not had compressor burnout. If the system has
experienced burnout, it is recommended that the
existing line set and indoor coil be replaced.
NOTE
Refrigeration Piping
•
Use only refrigerant grade copper tubes.
•
Split systems may be installed with up to 50 feet of
line set (no more than 20 feet vertical) without special
consideration (see long line set guidelines).
•
Ensure that vapor and liquid tube diameters are
appropriate to capacity of unit.
•
Run refrigerant tubes as directly as possible by
avoiding unnecessary turns and bends.
•
When passing refrigerant tubes through the wall, seal
opening with RTV or other silicon-based caulk.
•
Avoid direct tubing contact with water pipes, duct work,
floor joists, wall studs, floors, walls, and any structure.
•
Do not suspend refrigerant tubing from joists and
studs with a rigid wire or strap that comes in direct
contact with tubing.
•
Ensure that tubing insulation is pliable and completely
surrounds vapor tube.
It is important that no tubing be cut or seals broken until you
are ready to actually make connections to the evaporator
and to the condenser section. DO NOT remove rubber
plugs or copper caps from the tube ends until ready to
make connections at evaporator and condenser. Under no
circumstances leave the lines open to the atmosphere for
any period of time, if so unit requires additional evacuation
to remove moisture.
Capacity
Liquid
Vapor
Connections
Dia.
Tube
Dia.
Connections
Dia.
Tube
Dia.
-018
3/8”
3/8”
3/4”
3/4”
-024
3/8”
3/8”
3/4”
3/4”
-030
3/8”
3/8”
3/4”
3/4”
-036
3/8”
3/8”
7/8”
7/8”
-042
3/8”
3/8”
7/8”
7/8”
-048
3/8”
3/8”
7/8”
7/8”
-060
3/8”
3/8”
*1-1/8”
*1-1/8”
* Field supplied 7/8 x 1-1/8 connector required on indoor unit.
Table 3. Recommended Liquid & Vapor Tube
Diameters (in.)
Be extra careful with sharp bends. Tubing can “kink” very
easily, and if this occurs, the entire tube length will have
to be replaced. Extra care at this time will eliminate future
service problems.
It is recommended that vertical suction risers not be up-
sized. Proper oil return to the compressor should be
maintained with suction gas velocity.
Summary of Contents for GE APPLIANCES NS17HS
Page 7: ...Page 7 31 5000752 Rev 0 Figure 1 Typical Parts Arranegment Figure 2 Typical Parts Arranegment...
Page 29: ...Page 29 31 5000752 Rev 0 Figure 11 Typical Factory Wiring 018 through 036 models...
Page 30: ...Page 30 31 5000752 Rev 0 Figure 12 Typical Factory Wiring 042 through 060 models...
Page 31: ...Page 31 31 5000752 Rev 0 Figure 13 Wiring Diagram 018 036 Models...
Page 32: ...Page 32 31 5000752 Rev 0 Figure 14 Wiring Diagram 042 060 Models...
Page 43: ...Page 43 31 5000752 Rev 0 Notes...