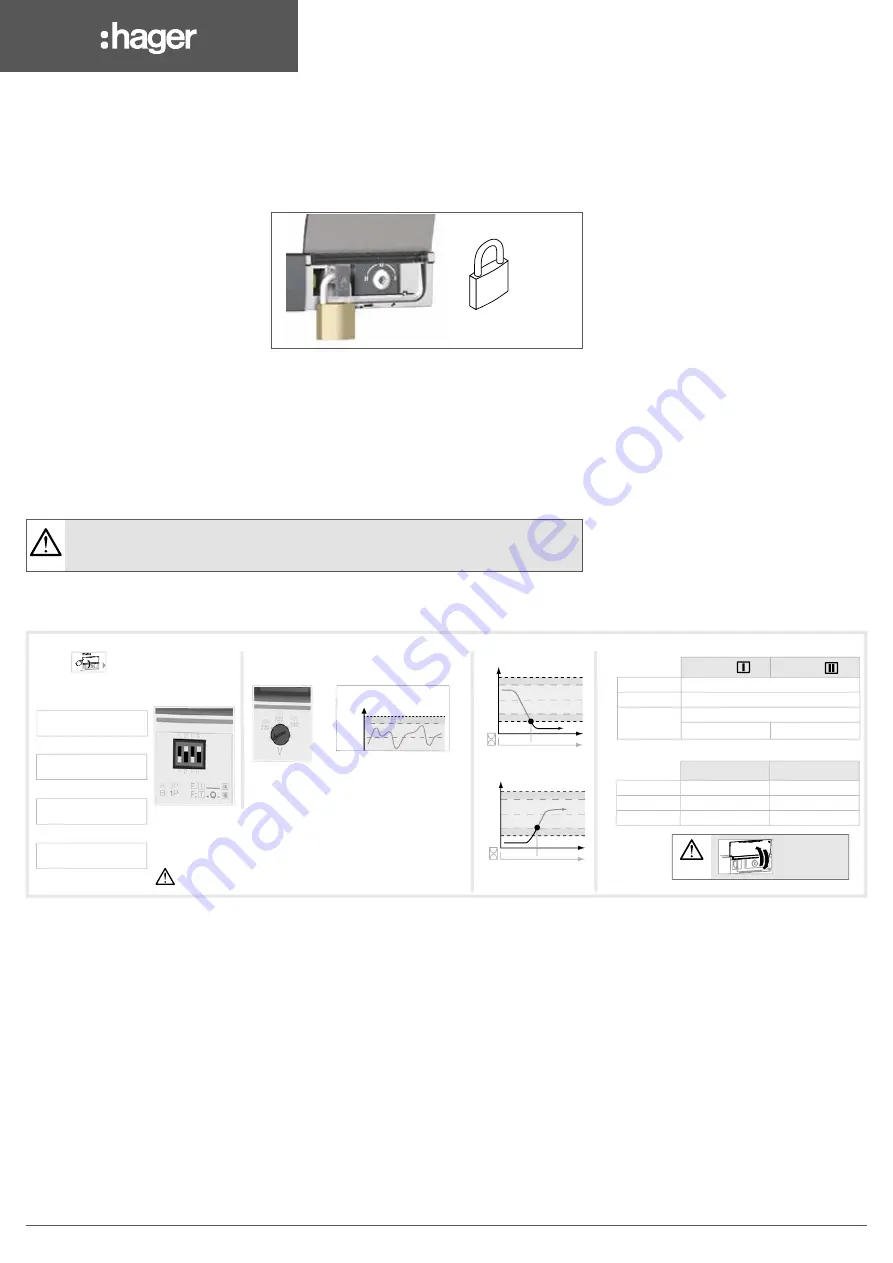
6LE007621A
22
11.4.
Padlocking
Enables locking in the 0 position (factory configuration) or in positions I, 0 or II (user configurable).
It is necessary to configure padlocking to all positions before installation as access to configuration is at
the back of the product. Refer to section "7.1. Changing the padlocking configuration", page 11
Locking is only possible in manual mode
(cover open).
Pull on the locking handle to enable the
interlock. Lock by inserting a padlock into
the orifice provided for this purpose.
4 mm min
8 mm max
11.5.
Programming
Whilst in manual mode check the wiring and installation. If ok power up the product.
This product must always be put into service by qualified and approved personal.
The LED signalling is only active when the product supply is on (supply LED lit).
To set the dip switches, it is necessary to open the AUTO/MANU cover.
The commissioning must always result in having at least 1 LED source available lit.
Therefore, the voltage and frequency must be within the defined thresholds.
Any action on the potentiometers changes the settings, even if the cover is closed.
11.5.1. Single phase version
207208209210 63 64 73 74
22
44
66
88
11
33
55
77
22
44
66
88
11
33
55
77
2
4
6
8
1
3
5
7
2
4
6
8
1
3
5
7
/
I1 I2 I3
O1 O2
5 A AC1 / DC1
250 Vac / 30Vdc
22 24 21
11 14 12
01 04 02
In order to
padlock put
the product in
manual mode.
Pull the locking
mechanism and insert a padlock
as shown.
As standard padlocking in the O
position. Configurable to I - O - II
(see step 1).
Installation
Control / aux power terminals and wiring
Recommended orientation
116
324
26
245
143
350
13
53
46
73,5
18
45
MAX : 2
x2
x2
X8
Click!
Automatic
operation
PROGRAMMING
(
Manual operation)
Power terminal connections
Manual
operation
Padlocking mode
Check
Dip switch settings
Type of network: A-B
Frequency: C-D
Stop in O position: E-F
Type of application: G-H
Source voltage supply configuration
Padlocking configuration
LED's info
Timer settings
Source
Source
LED ON
available
LED OFF
missing or out of range
LED blinking
- a timer is counting down
- test mode
A: 3P
B: 1P
C: 50 Hz
D: 60 Hz
E: No stop in O position
F: 2 s stop in O position
G: Network / Genset
H: Network / Network
Load side bridging bars
125A: HZI400
160A: HZI401
Voltage taps provide 2x ≤ 1.5 mm
2
connections.
They can be fitted in any terminals on the
source supply side.
Do not use on the load side when
equipped with a bridging bar.
Close the front cover as shown
to put the product into automatic
mode.
Source supply
side
Ensure that the product is in manual mode
(front cover open).
DIN RAIL IEC 60715
131,5
47
326
131,5
52
104
176
Auxiliary contacts:
Fitting of auxiliary contacts:
HZI300.
To fit an AC, the switch must first
be put in position O. An auxiliary
contact module comprises: one
NO / NC changeover contact for
each position (I-O-II). To install use
the long screws supplied with the
module.
Recommended
Ok
Ok
Ok
Ok
Ok
I
O
II
I
O
II
Step 1
Step 2
Step 3
1
2
4
5
6A
6B
6C
3
(Max 8 Nm)
Extension
To simplify
operation use
the handle
with the
extension
provided.
Open the front
cover as shown
to put into
manual mode.
Use the handle situated in the
front panel under the cover to
operate the transfer switch.
Check the changeover switch
position on the indicator before
operating.
LOAD
&
é
"
'
HYST
HYST
+∆U/
+∆F
+∆U/
+∆F
Un
HYST: 20 % ∆U/F
ΔU: 5 - 20 %
ΔF: 3 - 10 %
Ensure that the product is
installed on a flat rigid surface.
Tighten to avoid movement on the
DIN rail.
The HIC4xxA is
delivered with
padlocking
configured to the
O position.
To allow padlocking in all
positions (I - O - II), configure
the HIC4xxA as follows
before installation. (Screw
is located at the back of the
product).
It is essential
to tighten
all terminals
including those
not being used.
Whilst in manual
mode, check the
wiring and if ok power
up the product.
6LE003168Ad
3
6LE003168Ad
2
Type
Terminal
no.
Application
Status of the
contact
Description
Output
characteristics
Recommended
connection
cross-section
Inputs
207
Common
6 mm
0.5 to 1.5 mm
2
6 mm
0.5 to 2.5 mm
2
3
0.5 Nm
208
I1
Network / Network
With priority
Dry potential free
contact
Without priority
Network / Genset
Automatic retransfer
Manual Retransfer
209
I2
Network / Network
Source priority I
Source priority II
Network / Genset
Stop the test on load
Test on load
210
I3
Network / Network
or Network / Genset
AUTO mode
Automatic mode
inhibition
Outputs 63 / 64
O1
Network / Network
or Network / Genset
Product not available:
- Manual mode
- Operation failure
- Electronic failure
- No power sources
Resistive load
2A 30Vdc
0.5A 230Vac
Pmax:
60W or 125VA
Umax:
30Vdc or 230Vac
Product available
73 / 74
O2
Network / Genset
No start command genset
Generating set starting
90°
90°
LOAD
Type
Terminal
no.
Status of the
contact
Description
Output
characteristics
Recommended
connection
cross-section
Auxiliary
contact
block
HZI300
11/12/14
11
14
12
Changeover switch in
position I
250Vac 5A AC1
30Vdc 5A DC1
10 mm
0.5 to 1.5 mm
2
10 mm
0.5 to 2.5 mm
2
2.5
21/22/24
21
24
22
Changeover switch in
position II
01/02/04
01
04
02
Changeover switch in
position O
Un (P-P):
380-420 Vac
Un (P-N):
220-240 Vac
Loss of priority
source timer
Return of priority
source timer
6 mounting brackets 6x M6 screw - 2.5 Nm
MRT
Source availability LED's
Fault and state of the product LED's
q
AUT
LED ON
Fault
Auto mode
LED OFF
Product OK
Manual mode
LED blinking
Wait
Manual retransfer
MFT
MFT: 0-60 s
U/F
[HYST]
[HYST]
MRT: 0-30 min.
U/F
6 mm
6 mm
0.5 to 1.5 mm
2
0.5 to 2.5 mm
2
4
5 Nm
15 mm
15 mm
10 to 70 mm
2
The LED signalling and operation is only active when the product supply is
available. To set the dip switches, it is necessary to open the Auto/Manual
cover. Commissioning must always result in having at least 1 LED source
available on. (Therefore, the voltage and frequency must be within the defined
thresholds).
Any action on the potentiometers will change the settings, even when
the cover is closed.
1
0
2
0
Fault Reset
Use 20 mm screws for 1 module
Use 35 mm screws for 2 modules
1 Nm
PZ1
0.25 Nm
PZ2
0.25 Nm
PZ2
3.5
0.45 Nm
1 Nm
PZ2
1 Nm
PZ2
4-8 mm