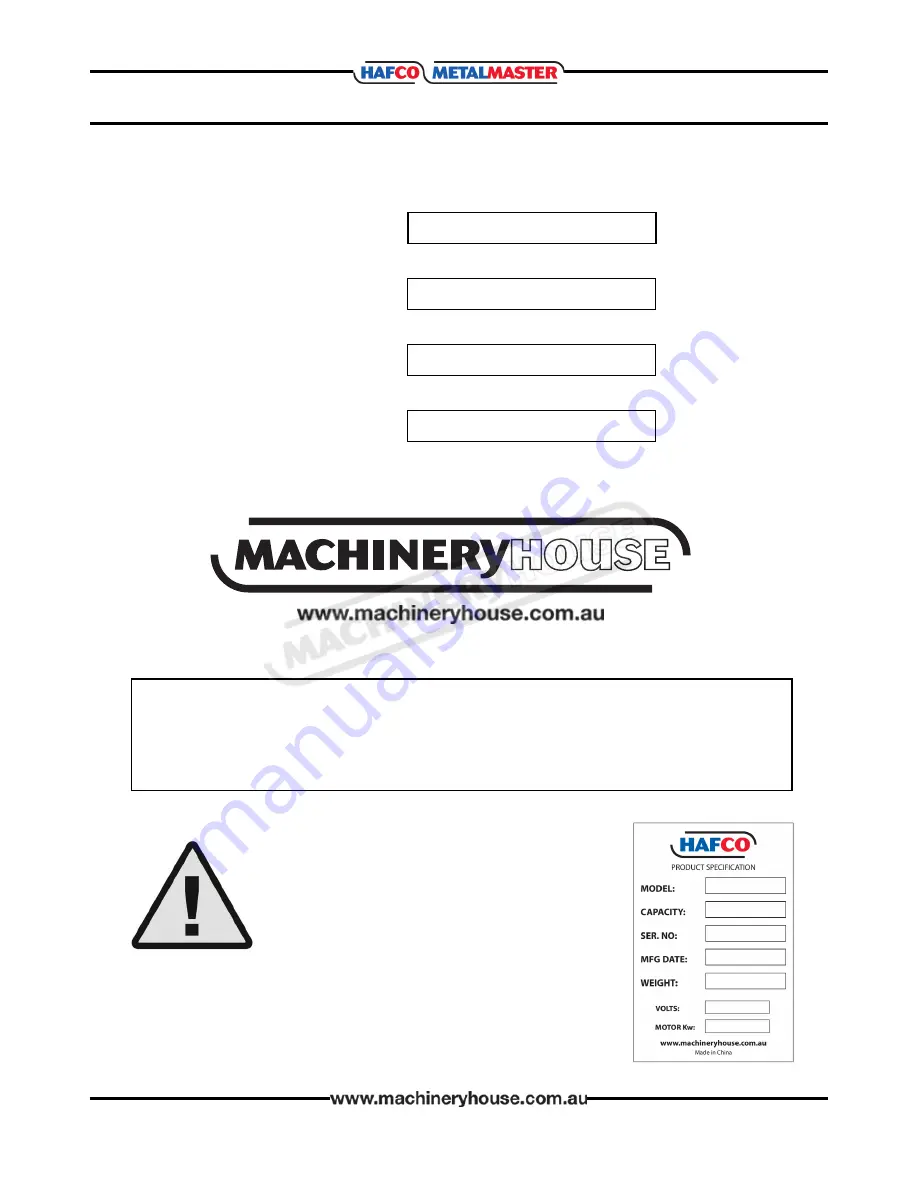
2
OPERATION MANUAL
NOTE:
In order to see the type and model of the machine, please see the
specification plate. Usually found on the back of the machine. See
example (Fig.1)
Fig.1
METAL CUTTING BAND SAW
MACHINE
EB-260V
MODEL NO.
SERIAL NO.
DATE OF .
NOTE:
This manual is only for your reference. Owing to the continuous improvement of the HAFCO
machines, changes may be made at any time without obligation or notice. Please ensure the
local voltage is the same as listed on the specification plate before operating this electric
machine.
Distributed by
www.machineryhouse.co.nz
MACHINE DETAILS
Page 2
Instruction Manual for EB-260V (B062V)
04/04/2019