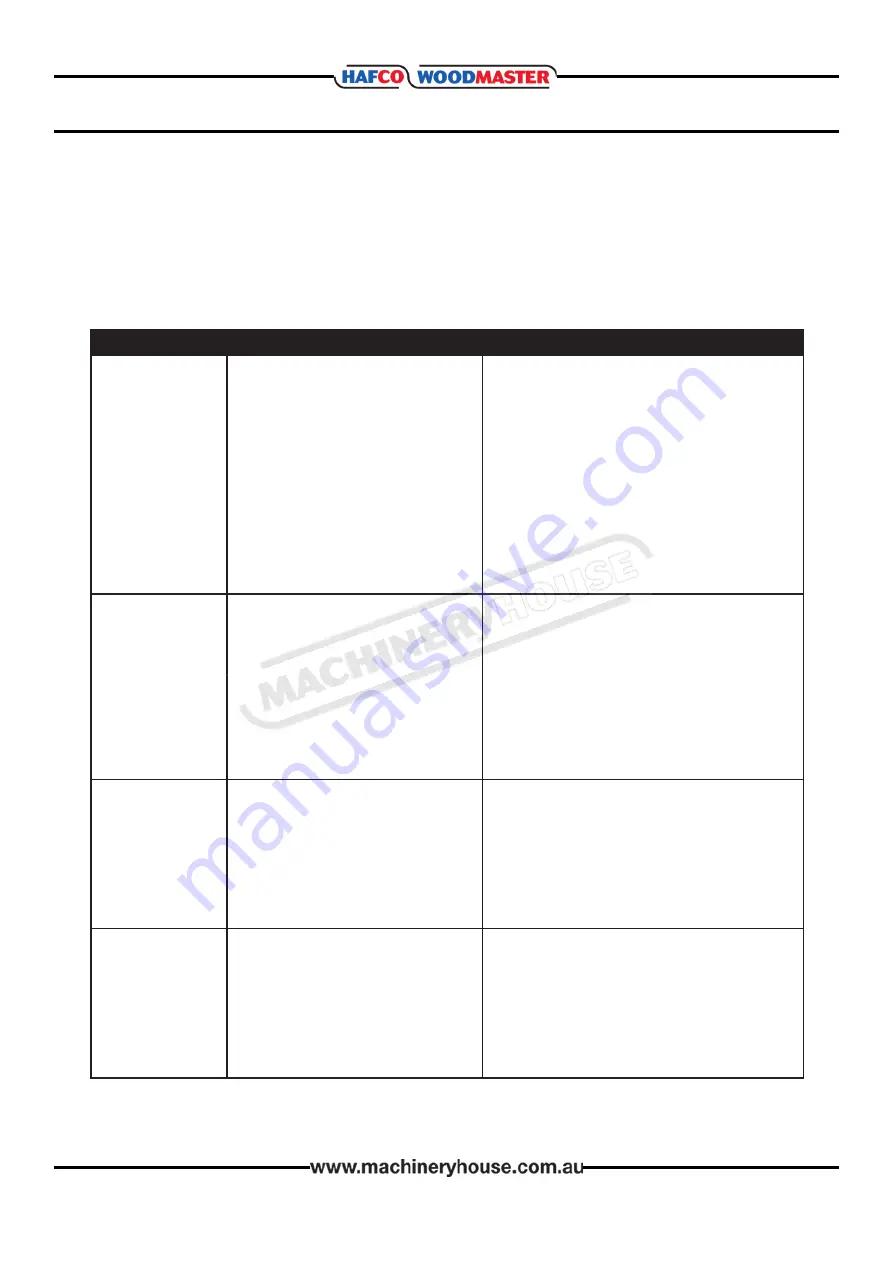
23
OPERATION MANUAL
5.3 TROUBLESHOOTING
SYMPTOM
SYMPTOM
POSSIBLE CAUSE
POSSIBLE SOLUTION
Machine does not
start or a breaker
trips.
1. Stop push-button engaged/faulty.
2. Power switched OFF or at fault.
3. Thermal overload relay has tripped.
4. Wall circuit breaker tripped.
5. Plug/receptacle at fault/wired
incorrectly.
6. Motor connection wired incorrectly.
7. Contactor not energized.
8. Wiring open/has high resistance.
9. ON/OFF switch at fault.
10. Start capacitor at fault.
11. Centrifugal switch at fault
12. Motor at fault.
1. Check magnetic switch/replace it.
2. Ensure power supply is switched ON
3. Reset trip load dial if necessary; replace.
4. Ensure circuit size is correct/replace.
5. Test for good contacts; correct the wiring.
6. Correct motor wiring connections
7. Test all legs for power/replace if faulty.
8. Check and fix broken, disconnected wires
9. Replace switch.
10. Test/replace if faulty.
11. Adjust/replace centrifugal switch.
12. Test/repair/replace.
Machine stalls or is
underpowered
1. Feed rate too fast.
2. Workpiece material not suitable.
3. Dust collection ducting problem.
4. Motor overheated.
5. V-belt(s) slipping.
6. Run capacitor at fault.
7. Pulley/sprocket slipping on shaft.
8. Motor bearings at fault.
9. Motor at fault.
1. Decrease feed rate.
2. Ensure timber moisture is below 20%.
3. Clear blockages, use smooth wall duct,
4. Clean motor, let cool, and reduce load.
5. Tension/replace belt(s) ensure pulleys
are aligned
6. Test/repair/replace.
7. Replace loose pulley/shaft.
8. Test/repair/replace.
9. Test/repair/replace.
Excessive step
(snipe)
(gouge at the end
of the workpiece
that is uneven with
the rest of the cut).
1. One or both of the bed rollers are
set too high.
2. Rear table extension slopes down or
is not level with the table
3. Chip breaker or pressure bar set too
low
4. Workpiece is not fully supported as it
leaves the thicknesser.
1. Lower the bed rollers
2. Adjust the rear extension wing set screws
to make the extension level with the table
3. Raise the height of the chip breaker or
pressure bar
4. Use a roller stands to properly support the
workpiece as it leaves the thicknesser.
Workpiece stops/
slows in the middle
of the cut.
1. Depth of cut too deep.
2. Pitch/glue build-up on thicknesser
components.
3. One or both of the bed rollers are set
too low or too high.
4. Chip breaker or pressure bar set too
low
5. Feed rollers set too low or too high.
1. Reduce the depth of cut.
2. Clean planer components with a pitch/
resin dissolving solvent.
3. Lower/raise the bed rollers
4. Raise the height of the chip breaker or
pressure bar
5. Adjust the feed rollers to the correct height
Should any problems arise review the troubleshooting procedures in this section to find the
possible problem or fix and adjust your machine.
The spare parts view and the proceedure for ordering is layed out in the spare parts section.