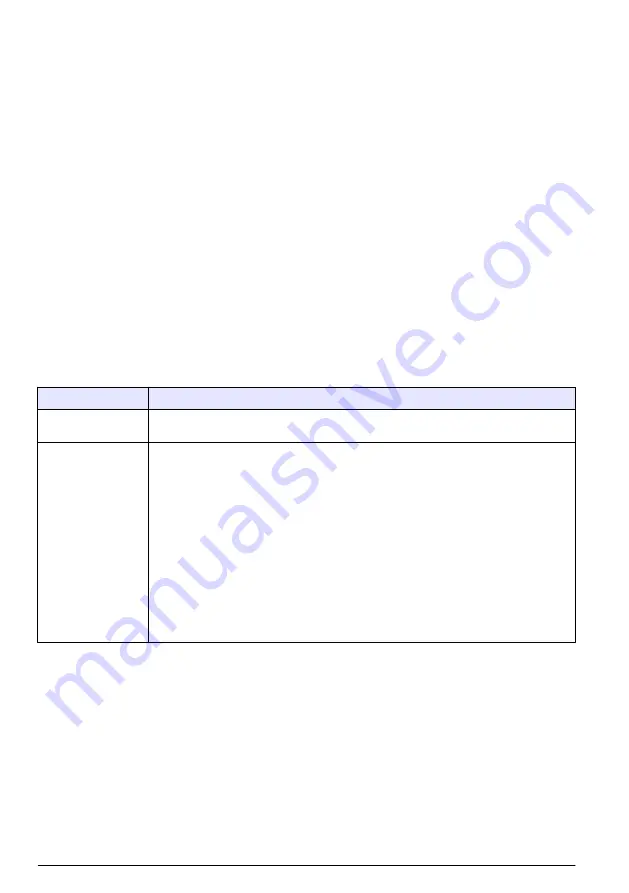
To remove a thin layer at the windows, use a soft cloth or clean water. Do not use harsh cleaning
solutions, spatula, sand paper or cleaning products with abrasive ingredients to remove continuous
dirt. Contact the manufacturer to replace damaged windows.
Note: Do not scratch the glass of the windows.
Note: Make sure not to touch the window surface with fingers.
1.
From the Main menu, select
Options
.
2.
Select
Service mode
to set the relay for the compressed air cleaning on HOLD.
Note: The Service mode also disables measurements.
3.
Remove the sensor from the basin or flow cell.
4.
Clean the measuring window with a cleaning agent and a cloth.
5.
When the cleaning is complete, push
Service mode
to remove the HOLD condition.
Clean the compressed air connector
1.
Manually clean the compressed air connector 1–2 times a week.
2.
Clean the compressed air connector if very fine mud clogs the cleaning connector.
To prevent blockages, install a check valve.
Troubleshooting
Disconnect the compressed air cleaning system before the sensor is removed from the basin.
Problem
Solution
The controller cannot
find the sensor.
Examine the cable and the probe connector for damage. Contact the technical support if
there are damages.
The sensor readings
are much higher or
lower than expected.
1.
Make sure that settings for factor and offset are correct. Refer to
on page 14.
2.
Identify the expected measuring value is measurable with the installed optical path
length.
3.
Measure the optical path length of the sensor. Make sure that the correct length is set
in the controller settings. Refer to the controller documentation for more information.
4.
Clean the measuring windows. Refer to
on page 15.
5.
Put the sensor in a container with a known target parameter concentration (sample or
standard). Make sure that there are no air bubbles between the measuring windows.
Use a syringe to put sample between the measuring windows.
• If the readings are correct—There is an issue with dirt on the measuring windows.
Change the location or the cleaning settings. Contact the technical support.
• If the readings are not correct—Contact the technical support.
16
English
Summary of Contents for NV3300
Page 2: ...English 3 Fran ais 19 Espa ol 35 51 67 Portugu s 82 98 114 2...
Page 53: ...ESD 53...
Page 54: ...NV3300 SAC Spectral Absorption Coefficient 1 8 LED 4 50 100 150 250 mm 51 CD500 CD300 54...
Page 55: ...1 1 4 2 5 3 6 2 2 1 2 55...
Page 57: ...OFF 3 4 5 3 57...
Page 58: ...4 1 6 mm 3 2 4 8 mm 5 58...
Page 59: ...M12 10 m 6 7 COM COM 6 7 3 1 RS232 RX RS485 A 2 3 ETH_TX 4 ETH_TX 5 12 24 VDC 6 ETH_RX 59...
Page 64: ...MSDS SDS 1 Options 2 Service mode HOLD 3 4 5 Service mode HOLD 1 1 2 2 1 62 2 3 4 64 5 64...
Page 69: ...ESD TV 69...
Page 70: ...NV3300 SAC 1 8 LED 4 50 100 150 250 mm 67 CD500 CD300 1 1 4 2 5 3 6 2 70...
Page 72: ...2 SAC 4 LED 1 nm LED 2 nm SAC 436 1 m 436 740 DIN EN ISO 7887 2011_method B NBR OFF 3 4 5 72...
Page 73: ...3 4 1 6 mm OD 3 2 4 8 mm OD 73...
Page 74: ...5 M12 10 m 6 7 COM COM 6 74...
Page 76: ...8 1 3 2 4 1 Options 2 Cleaning 3 15 5 10 mA 5 Execute Sensor 5 76...
Page 79: ...MSDS SDS 1 Options 2 Service mode HOLD 3 4 5 Service mode HOLD 1 2 1 77 2 3 4 79 5 79...
Page 100: ...ESD 100...
Page 101: ...NV3300 SAC 1 8 LED 4 50 100 150 250 98 CD500 CD300 101...
Page 102: ...1 1 4 2 5 3 6 2 2 1 2 102...
Page 104: ...OFF 3 4 5 3 104...
Page 105: ...4 1 OD 6 3 2 4 OD 8 5 105...
Page 107: ...3 8 7 ETH_RX 8 RS232 TX RS485 B 7 1 13 0 5 8 2 8 3 HOAB 3 6 25 82 108 8 1 3 2 4 107...
Page 111: ...1 Options 2 Service mode HOLD 3 4 5 Service mode HOLD 1 1 2 2 1 109 2 3 4 110 5 111...
Page 116: ...ESD 116...
Page 117: ...NV3300 SAC 1 8 LED 4 50 100 150 250 mm 114 CD500 CD300 1 1 4 2 5 3 6 2 117...
Page 119: ...NBR OFF 3 4 5 3 119...
Page 120: ...4 1 6 mm 3 2 4 8 mm 5 120...
Page 121: ...10 M12 6 7 COM COM 6 7 M12 3 8 1 RS232 RX RS485 A 2 3 ETH_TX 4 ETH_TX 5 12 24 V 6 ETH_RX 121...
Page 128: ......
Page 129: ......