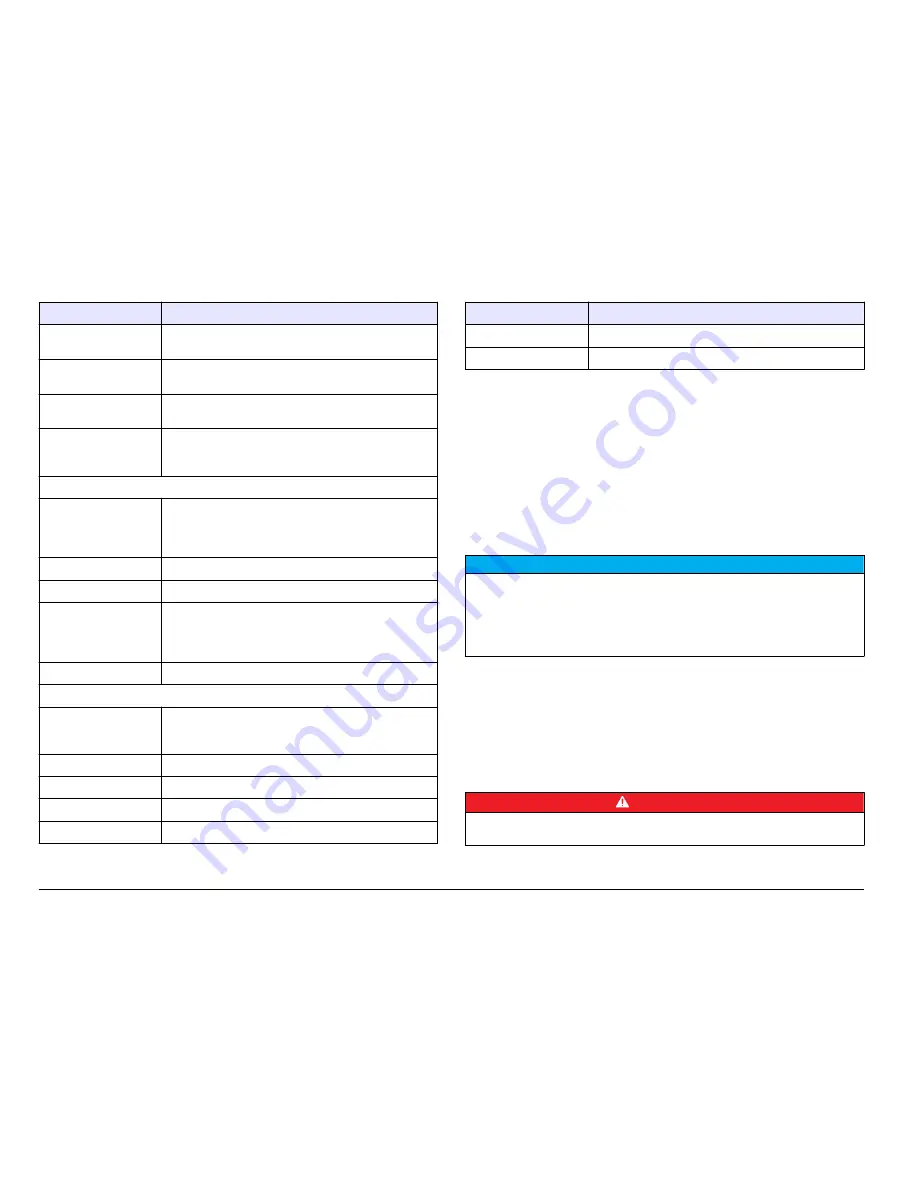
Specification
Details
Sensor-to-controller
distance
9 m (30 ft) maximum
1
Power requirements
90–130 VAC (115 VAC nominal) or 180–260 VAC
(230 VAC nominal), 50/60 Hz, 10 VA maximum
Relays
Four electromechanical relays; SPDT (Form C)
contacts; 115/230 VAC, 5 A @ 30 VDC resistive
Analog outputs
Two isolated 0.00–20.00 mA or 4.00–20.00 mA outputs
each with 0.004 mA (12–bit) resolution; up to 600 ohm
load capacity
Mechanical:
Enclosure
NEMA 4X; polycarbonate face panel, epoxy-coated
cast aluminum door and case with four 13-mm (½–in.)
cable entry holes, nylon mounting bracket and stainless
hardware
Mounting
Panel, surface or pipe mount
Net weight
2.3 kg (5 lb)
Fuses
One type T, 80 mA, 250 V slow-blow fuse for the 230 V
line power circuits, 5 mm x 20 mm; one type T,
100 mA, 250 V slow-blow fuse for the 115 V line power
circuits, 5 mm x 20 mm
Certifications
15 year environmental friendly use period
Accu4 system performance:
Measurement range
0.000–100.0 NTU; auto-ranging and automatic decimal
point shift above 1.000 NTU and 10.00 NTU (same for
other measurement units)
Measurement units
NTU, TEF, FNU or FTU
Signal averaging
0 to 60 seconds
System accuracy
±2% of reading, all ranges
Sensitivity
0.001 NTU
Specification
Details
Repeatability
0.1% of span or better
Temperature drift
Zero and span: 0.01% of span per °C
1
Contact the manufacturer if a longer distance is necessary.
General information
In no event will the manufacturer be liable for direct, indirect, special,
incidental or consequential damages resulting from any defect or
omission in this manual. The manufacturer reserves the right to make
changes in this manual and the products it describes at any time, without
notice or obligation. Revised editions are found on the manufacturer’s
website.
Safety information
N O T I C E
The manufacturer is not responsible for any damages due to misapplication or
misuse of this product including, without limitation, direct, incidental and
consequential damages, and disclaims such damages to the full extent permitted
under applicable law. The user is solely responsible to identify critical application
risks and install appropriate mechanisms to protect processes during a possible
equipment malfunction.
Please read this entire manual before unpacking, setting up or operating
this equipment. Pay attention to all danger and caution statements.
Failure to do so could result in serious injury to the operator or damage
to the equipment.
Make sure that the protection provided by this equipment is not impaired.
Do not use or install this equipment in any manner other than that
specified in this manual.
Use of hazard information
D A N G E R
Indicates a potentially or imminently hazardous situation which, if not avoided, will
result in death or serious injury.
4
English
Summary of Contents for Accu4
Page 1: ...DOC023 97 80356 Accu4 T53 8320 01 2013 Edition 1 User Manual...
Page 2: ...English 3 29 2...
Page 32: ...1 8320 1 6 2 2 7 3 2 8 in NPT 4 9 5 in NPT 10 2 3 2 1 3 4 2 4 32...
Page 34: ...4 NEMA IP NEMA 4X IP66 3H1091 3H1230 4 3 11 4 mm 0 17 0 45 in ESD ESD 5 34...
Page 35: ...5 1 2 5 2 RS232 6 2 3 TTL 7 4 4 8 6 NEMA IP 6 35...
Page 37: ...7 2 TB 1 12 18 13 19 14 20 15 21 16 22 0 00 20 00 mA 4 00 20 00 mA 1 2 5 35 35 42 600 37...
Page 40: ...10 1 in NPT 4 in IPS 2 in IPS 5 3 6 in NPT 11 11 1 2 12 T53 4 40...
Page 50: ......
Page 51: ......