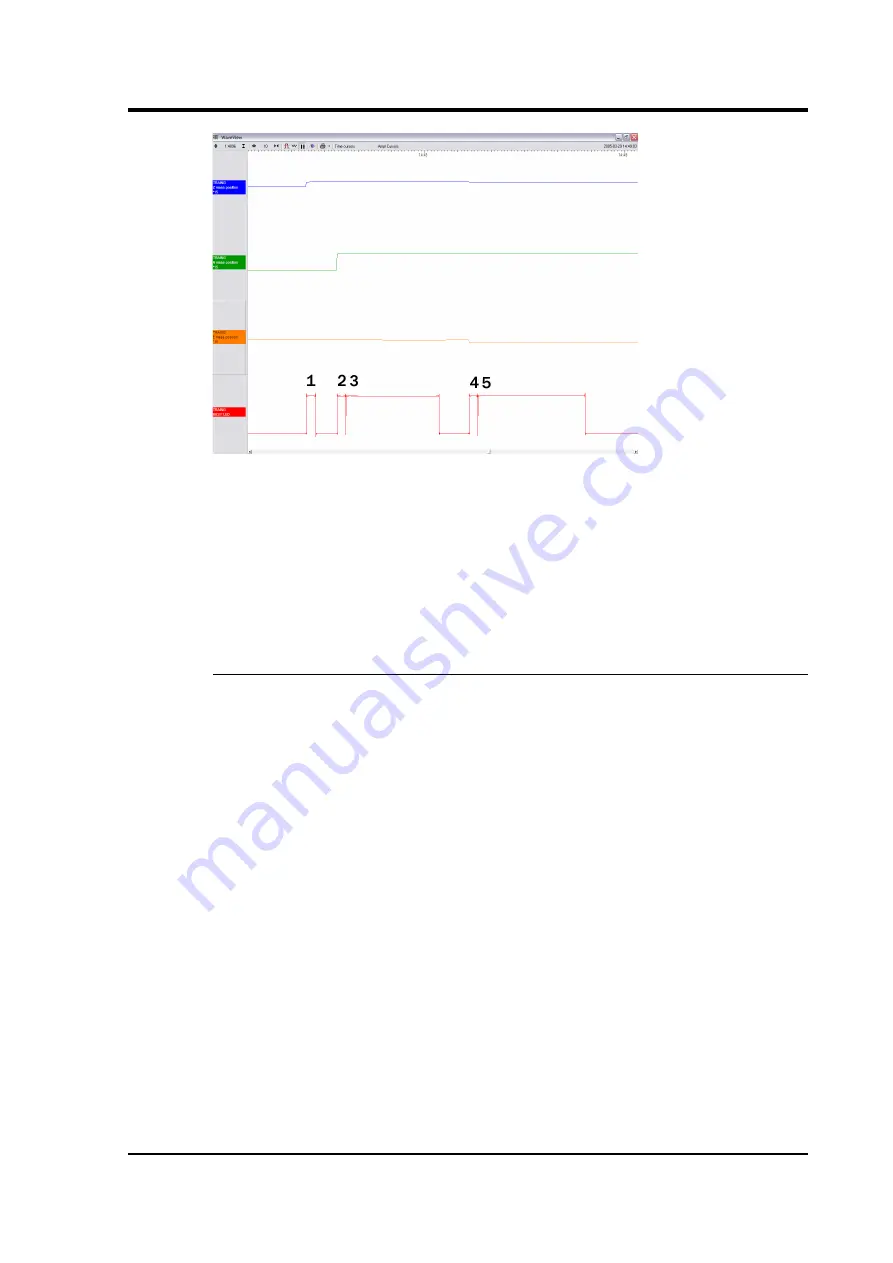
Operator's guide
In the five-stage process, each mass in turn is locked with a motorised
micrometer (stages 1, 2, 4), and the
N/S and E/W sensor bases are tilted
to their end stops (stages 3 and 5). At some point during each tilting
stage, the position of the relevant mass will flip to one or other side.
The
BUSY LED is lit during each stage, but goes out briefly between
stages, allowing you to follow the progress of the lock.
UNLOCK
This command unlocks the sensor masses and prepares the instrument
to begin operating.
If
UNLOCK is activated when the masses are already unlocked, the
processor will lock them and attempt to unlock again. This is useful if
you suspect that the locking procedure has failed.
During the
UNLOCK procedure, the instrument automatically
performs a round of centring for each component.
November 2006
67