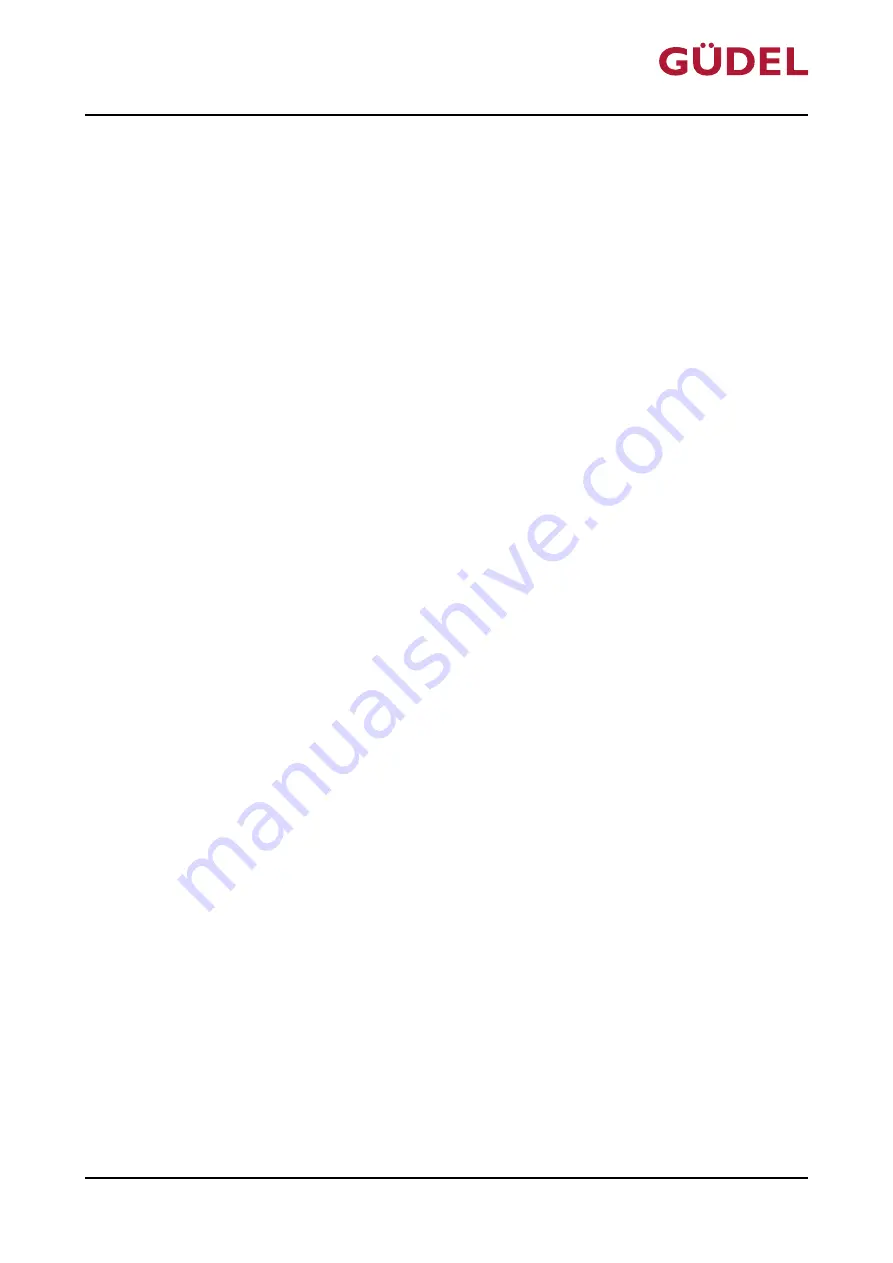
Illustrations
PSA (personal safety equipment) ................................................ 19
Position of the type plate ............................................................. 27
Dimensions and connections FlexxPump4 D .......................... 28
Design of FlexxPump lubrication system .................................. 31
Detailed design of FlexxPump4 D .............................................. 32
Function: Splitter, 2-fold ............................................................... 33
Function: Splitter, 3-fold ............................................................... 34
Function: Y-segment ...................................................................... 34
Installing the lubricant pump ........................................................ 38
Design FlexxPump4 D 3-fold ....................................................... 39
Design FlexxPump4 D 6-fold ....................................................... 40
Design FlexxPump4 D 9-fold ....................................................... 41
Design FlexxPump4 D 10-fold ..................................................... 42
Flow diagram Programming software ........................................ 45
Switching time diagram: Lubrication (normal case) ................ 47
Switching time diagram: Reset the error .................................. 51
Switching time diagram: Switching on and off .......................... 55
Switching time diagram: Empty ................................................... 57
Switching time diagram: General error ..................................... 59
Lubrication system FlexxPump .................................................... 74
Pre-lubricating rails and racks ...................................................... 74
Lubrication system FlexxPump .................................................... 75
Lubrication system FlexxPump .................................................... 75
Replace lubricant cartridge ........................................................... 80
Cleaning and checking lubrication system ................................ 87
Installing the lubricant pump ........................................................ 90
Design FlexxPump4 D 3-fold ....................................................... 91
Design FlexxPump4 D 6-fold ....................................................... 92
Illustrations
OPERATING MANUAL Lubrication system FlexxPump4 D
9007202674126091_v2.0_
EN-US
131
Summary of Contents for FlexxPump4 D
Page 14: ...General OPERATING MANUAL Lubrication system FlexxPump4 D 9007202674126091_v2 0_EN US 14...
Page 48: ...Commissioning OPERATING MANUAL Lubrication system FlexxPump4 D 9007202674126091_v2 0_EN US 48...
Page 50: ...Commissioning OPERATING MANUAL Lubrication system FlexxPump4 D 9007202674126091_v2 0_EN US 50...
Page 52: ...Commissioning OPERATING MANUAL Lubrication system FlexxPump4 D 9007202674126091_v2 0_EN US 52...
Page 54: ...Commissioning OPERATING MANUAL Lubrication system FlexxPump4 D 9007202674126091_v2 0_EN US 54...
Page 56: ...Commissioning OPERATING MANUAL Lubrication system FlexxPump4 D 9007202674126091_v2 0_EN US 56...
Page 68: ...Commissioning OPERATING MANUAL Lubrication system FlexxPump4 D 9007202674126091_v2 0_EN US 68...
Page 82: ...Maintenance OPERATING MANUAL Lubrication system FlexxPump4 D 9007202674126091_v2 0_EN US 82...
Page 86: ...Maintenance OPERATING MANUAL Lubrication system FlexxPump4 D 9007202674126091_v2 0_EN US 86...
Page 100: ...Maintenance OPERATING MANUAL Lubrication system FlexxPump4 D 9007202674126091_v2 0_EN US 100...
Page 102: ...Maintenance OPERATING MANUAL Lubrication system FlexxPump4 D 9007202674126091_v2 0_EN US 102...
Page 118: ...Accessories OPERATING MANUAL Lubrication system FlexxPump4 D 9007202674126091_v2 0_EN US 118...
Page 130: ...Torque tables OPERATING MANUAL Lubrication system FlexxPump4 D 9007202674126091_v2 0_EN US 130...
Page 140: ...Index OPERATING MANUAL Lubrication system FlexxPump4 D 9007202674126091_v2 0_EN US 140...
Page 142: ...Appendix OPERATING MANUAL Lubrication system FlexxPump4 D 9007202674126091_v2 0_EN US...
Page 143: ...Layout Appendix OPERATING MANUAL Lubrication system FlexxPump4 D 9007202674126091_v2 0_EN US...
Page 144: ...Appendix OPERATING MANUAL Lubrication system FlexxPump4 D 9007202674126091_v2 0_EN US...
Page 146: ...Appendix OPERATING MANUAL Lubrication system FlexxPump4 D 9007202674126091_v2 0_EN US...
Page 148: ...Appendix OPERATING MANUAL Lubrication system FlexxPump4 D 9007202674126091_v2 0_EN US...
Page 149: ......
Page 151: ...G DEL AG Industrie Nord CH 4900 Langenthal Switzerland info ch gudel com www gudel com...