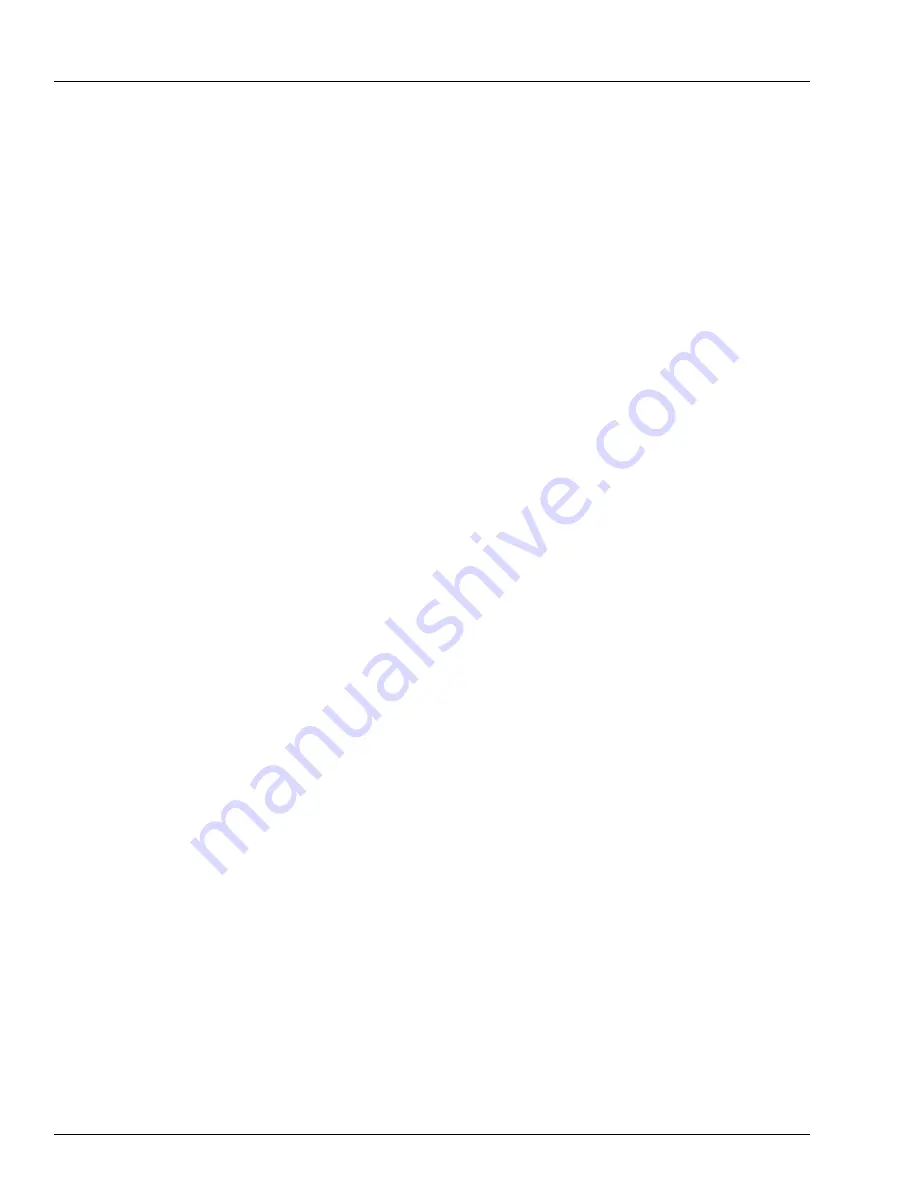
Autoflow Operation
8
Date
Employers Signature
Employee
________________________________________________________________________________________________________________________
_________________________________________________________________________________________________________________________
________________________________________________________________________________________________________________
___________________________________________________________________________________________________________________________
________________________________________________________________________________________________________________________
_____________________________________________________________________________________________________________________________
__________________________________________________________________________________________________________________________
_______________________________________________________________________________________________________________________________
_____________________________________________________________________________________________________________________________
______________________________________________________________________________________________________________________________
___________________________________________________________________________________________________________________________
______________________________________________________________________________________________________________________
_________________________________________________________________________________________________________________________
_____________________________________________________________________________________________________________________
______________________________________________________________________________________________________________________
_________________________________________________________________________________________________________________________
______________________________________________________________________________________________________________________
_______________________________________________________________________________________________________________________
______________________________________________________________________________________________________________________
______________________________________________________________________________________________________________________
_____________________________________________________________________________________________________________________
________________________________________________________________________________________________________________________
______________________________________________________________________________________________________________________
_____________________________________________________________________________________________________________
_______________________________________________________________________________________________________________________
_____________________________________________________________________________________________________________________
___________________________________________________________________________________________________________________
SAFETY SIGN-OFF SHEET
Summary of Contents for PNEG-728
Page 1: ...1 Autoflow Operation 1 Autoflow Operation PNEG 728 ...
Page 2: ...Autoflow Operation 2 This page was left blank intentionally ...
Page 6: ...Autoflow Operation 6 DECAL PLACEMENT ...
Page 10: ...Autoflow Operation 10 CONTROL SYSTEM Electronic Monitoring Control System ...
Page 13: ...13 Autoflow Operation CONTROL PANEL ...
Page 14: ...Autoflow Operation 14 CONTROL SYSTEM Electronic Monitoring Control System ...
Page 19: ...19 Autoflow Operation CONTROL SYSTEM ...
Page 20: ...Autoflow Operation 20 CONTROL SYSTEM ...
Page 21: ...21 Autoflow Operation CONTROL SYSTEM ...
Page 22: ...Autoflow Operation 22 CONTROL SYSTEM ...
Page 28: ...Autoflow Operation 28 FILL SYSTEM CONTROL BOX ...