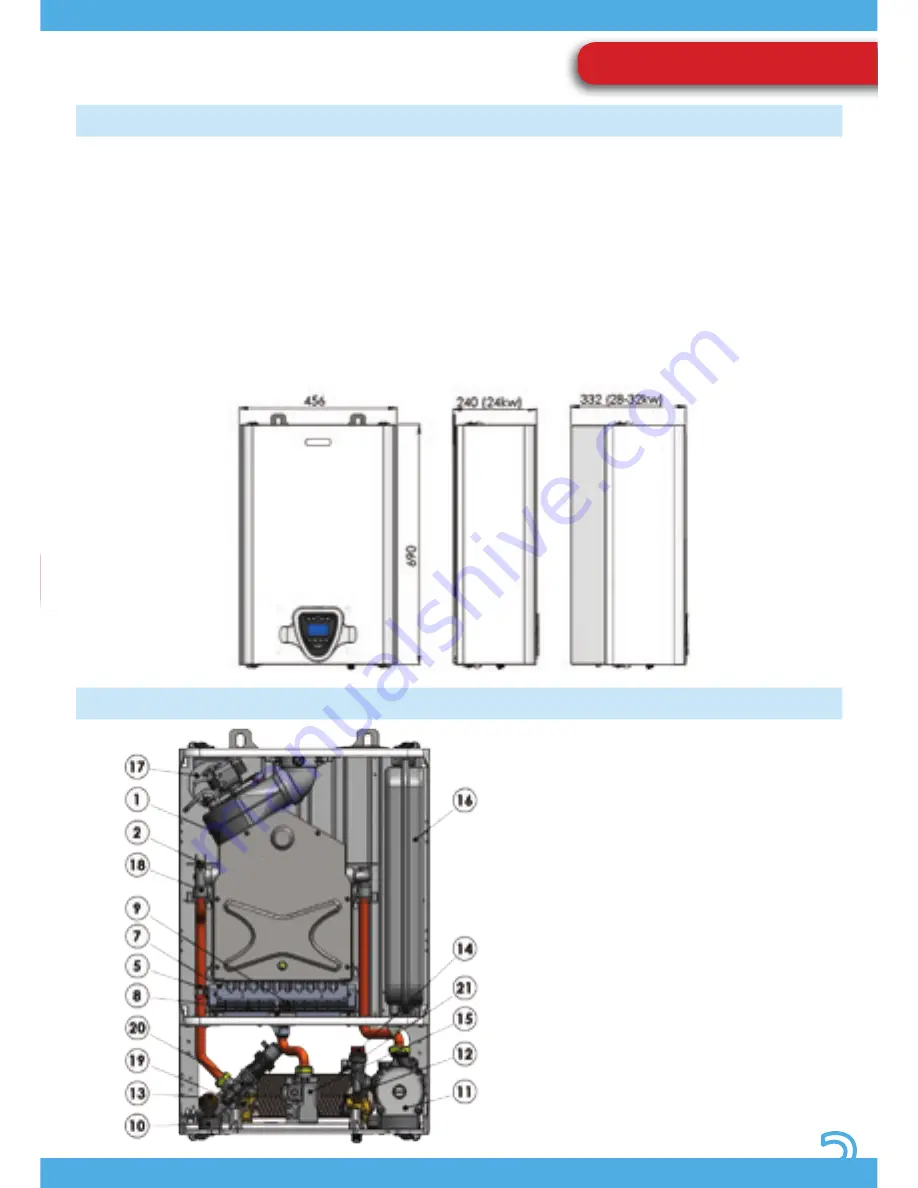
3
DESCRIPTION OF THE BOILER
COMPONENTS
The Ivy range of boilers represents the best
appliances available for domestic central
heating and hot water production. Their
essential but extremely modern and
elegant lines, compact size, solidity,
performance, reliability and safety place
Ivy boilers in the category of appliances
which are indispensable in every home. In
creating the Ivy range of boilers we chose
to design a system which could satisfy a
wide range of needs, able to adapt itself
to any situation and thus enlarging its
field of application. Models ranging from
24 to 32 kW power output are indeed
available. The flexibility of the Ivy range of
boilers is also increased by the possibility
to configure the management program
of the microprocessor fitted to the system.
This allows to pass from a reduced number
of functions and configurations which
make using the device easy, immediate
and effective to a complete configuration
with many specific options enabled as
well as the possibility to interface with
external control and regulation devices.
Ivy MR (whit rapid heat exchanger)
1) FUME EXTRACTOR
2) SAFETY THERMOSTAT
5) HEATING SENSOR
7) BURNER
8) IGNITION MONOELECTRODE
9) EARTH ELECTRODE
10) PRESSURE GAUGE
11) CIRCULATOR UNIT
12) DHW PRIORITY VALVE
13) PRESSURE SENSOR (TRANSMITTER)
14) SAFETY VALVE
15) GAS VALVE
16) EXPANSION TANK
17) COMBUSTION GAS PRESSURE SWITCH
18) PRIMARY HEAT EXCHANGER
19) IMMERSION DHW SENSOR
20) THREE-WAYS GROUP
21) SECONDARY HEAT EXCHANGER
Pic. 1
Pic. 2
USE AND OPERATION
Summary of Contents for IVY 24 MR/MN
Page 2: ......
Page 3: ...IVY 24 28 32 KW MR MN MONOTHERMAL BOILER MANUAL VERS 11 2017 REV 3...
Page 18: ...Pic 20 Pic 21 LAYOUT OF CONNECTIONS 24 KW 28 32 KW...
Page 43: ......