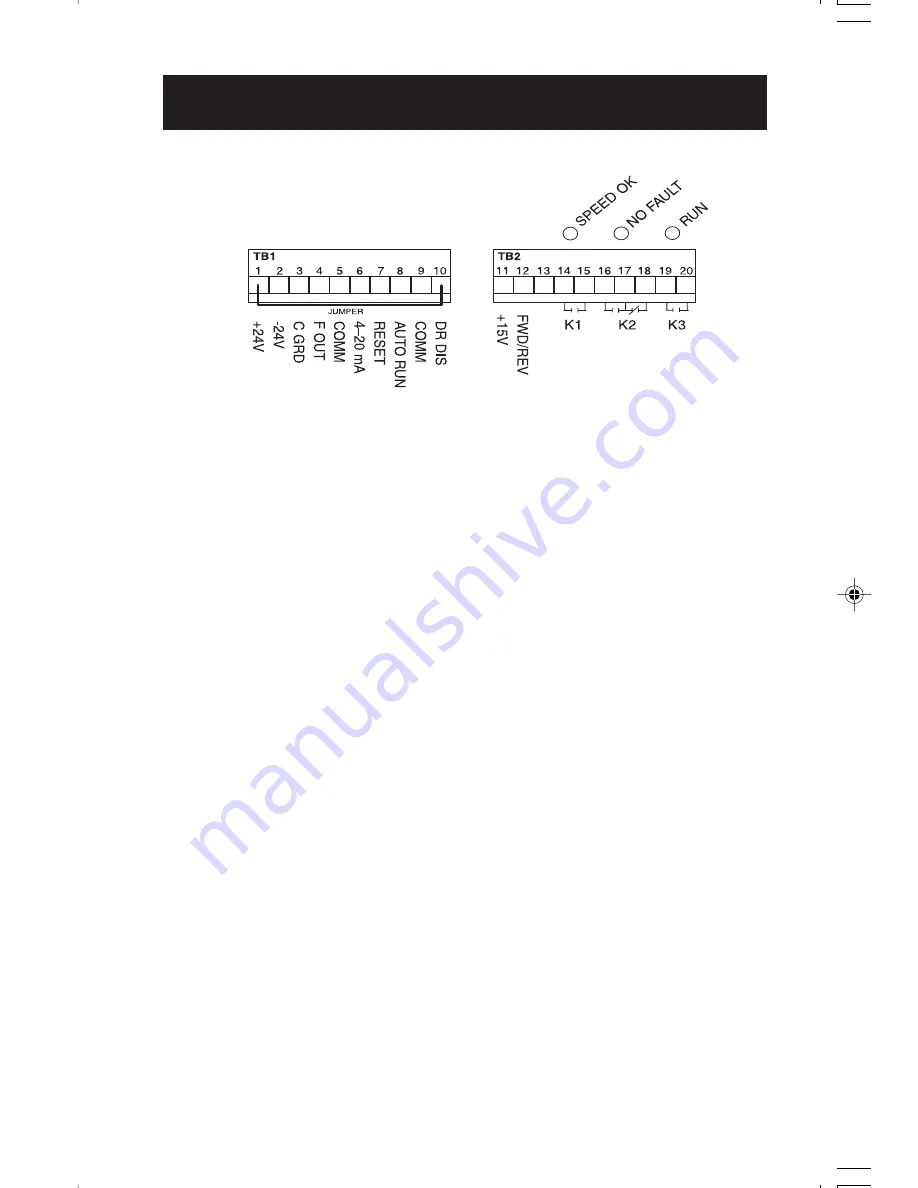
REDI-FLO VFD AUXILIARY INPUT/OUTPUT
REDI-FLO VFD ELECTRICAL INPUT/OUTPUT
Redi-Flo VFD output terminals are to be terminated into the Harting connector per Figure
10 below:
Figure 9:
WARNING- If the Redi-Flo VFD is miswired for the incoming voltage internal
damage may occur to the drive!
This drive contains possibly lethal AC voltage when AC power is connected. Switching
the Redi-Flo variable frequency drive switch to STOP does not remove AC line voltage.
All input phases must be disconnected before it is safe to touch motor terminals or
control equipment parts. Lethal voltage may be present up to 2 minutes after
disconnecting from power source. To change Input/Output line connections, first make
sure that input power is turned off and Redi-Flo VFD is disconnected. Then remove the
Redi-Flo VFD cover and wire for 115V or 230V.
CAUTION !
Figure 10:
Figure 11: Diagram of input and output terminals
located on top circuit board (behind cover)
Page 15
Page 16
• 24VDC: 100mA power supply to power external process loop. To connect to this
supply, connect to terminals 1 and 2 as labeled in Figure 11.
• 0 - 10V External speed (frequency) reference: To connect a 0-10V (0-1 mA)
external speed reference device, (Yokogawa Model # 251-320-MTMT or equivalent),
connect to terminals 4 and 9 as labeled in Figure 11.
• 4 - 20 mA Input signal: Can be used to control the Redi-Flo VFD. To set the
Redi-Flo VFD to follow a 4-20 mA input signal from a control device, connect to
terminals 5 and 6 as shown in Figure 11. The mode selection knob must also be turned
to the appropriate automatic mode, RF2A or RF4A depending on the pump being used.
A jumper is required between terminals 8 and 11, and enable Operator Adjustable
Control feature Auto Reference signal(F14) see Page 12-14.
• RST Auxiliary fault reset (reset): An auxiliary fault reset momentary contact between
terminals 7 and 11 as labeled in Figure 11.
• AUTO RUN Automatic run permissive: A jumper must be placed between
terminal 8 and 11 as labeled in Figure11, for automatic 4 - 20 mA speed reference signal
following capability. A jumper between terminals 8 and 11 does not affect manual
operation.
• DR DIS Drive enable/disable terminal: A switching device can be added to this
normally closed (jumpered) terminal giving an external enable/disable option. When
these terminals are opened during operation the unit coasts to a stop. The unit
ramps up when terminals are closed. This jumper is wired from terminal 1 to
terminal 10, as labeled in Figure 11.
• FWD/REV Pump rotation: Direction can be reversed externally by connecting a
switching device or jumper to terminals 11 and 12 as labeled in Figure 11. Open is
normal rotation and closed is reverse rotation.
• Run/Fault Signal outputs: Contact ratings, 2A @ 250V/30VDC
– K1-Redi-Flo VFD Speed Reached Output: Normally open contact between
terminals 14-15, to close when Redi-Flo VFD is in run mode and speed dial set
frequency is reached.
– K2-Redi-Flo VFD No Fault/Fault Output: Normally open and normally closed
contacts terminals 17-18. Relay to energize upon application of power. The N.O.
and N.C. contacts will change state when fault occurs.
– K3-Redi-Flo VFD Run Acknowledge Output: Normally open contact terminals 19-
20 to close when Redi-Flo VFD is in run mode and there is output current.
Input Power Terminals
The Input voltage can be changed between 115V and 230V by changing the line input
connections as shown in Figure 9 below.
L1
L2
L3
GND
L1
L2
L3
GND
White
Black
Green
(Ground)
White
Black
Green
(Ground)
115V
230V
U V W G
1 2 3 4
White
Green
Red
Black
Harting Terminals
Drive Terminals
To access output terminals refer to page 13 steps 1-2
Output Power Terminals
URES
.
TR'sVFDIO.p65
5/31/00, 9:02 AM
9