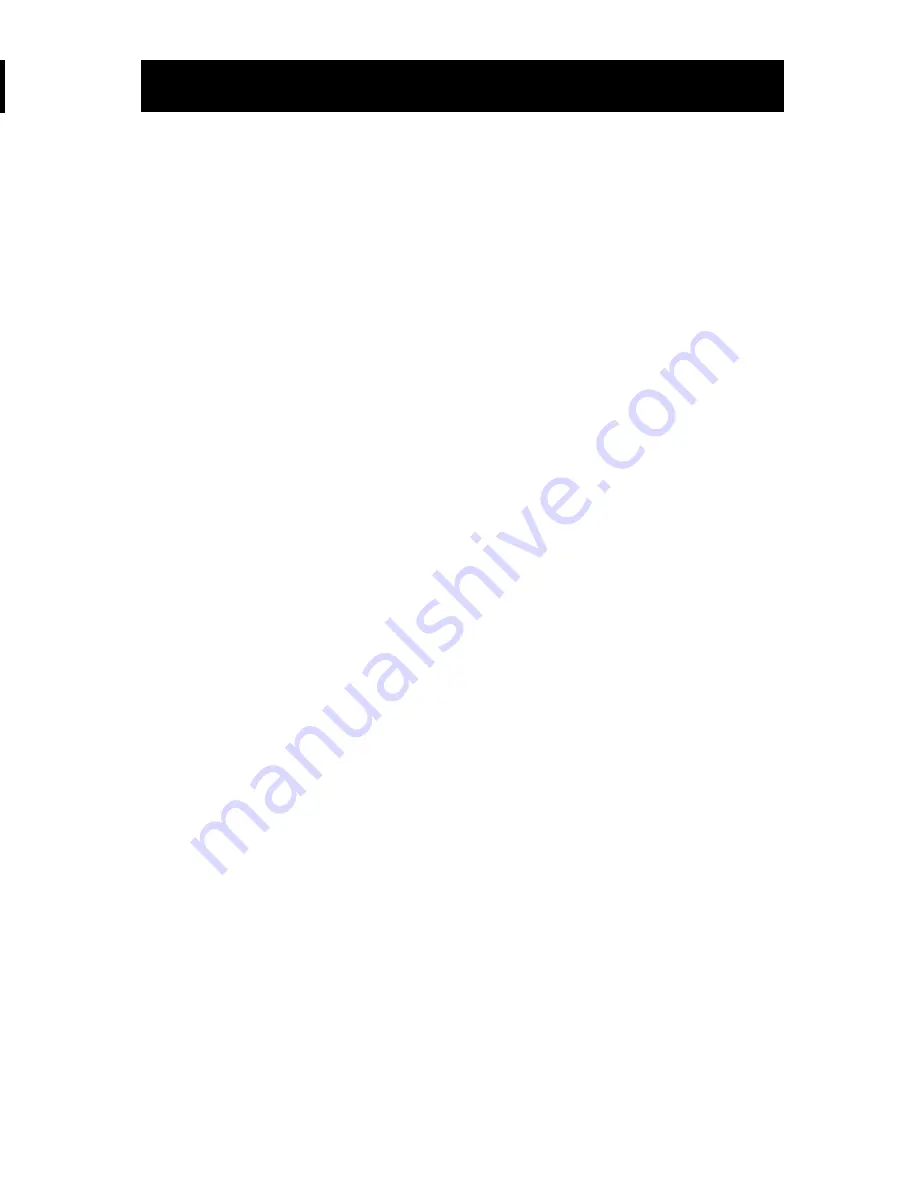
Operating the Pump
Page 10
Page 9
Installation Procedures
Installation depths
Maximum installation depth: below the static water level: 500 feet,
Minimum installation depths: 1.75' below the dynamic water level:
Vertical installation:
During start-up and operation, the pump must always be
completely submerged in water.
Horizontal installation:
The pump must be installed at least 1.75 ft. below the
dynamic water level. If there is a risk that the pump might be
covered by mud, the pump must always be placed in a flow
sleeve.
17. Generator Operation
• It is OK to operate the Redi-Flo3 with a generator.
The generator must be sized 10% above the pumps P1
(Input Power) values.
Use the table to select the correct size generator for the
motor HP.
16. Installing the Pump(cont.)
4.
Lower the pump into the well. Make sure the motor cable is not
damaged when the pump is lifted or lowered into the well —
especially in 3" wells.
NOTE: Do not lower or lift the pump
using the motor cable.
5.
When the pump has been installed to the required depth, the
installation should be finished by means of a well seal. Note that
the dynamic water level should always be above the pump.
6.
Loosen the safety wire so that it becomes unloaded and lock it to
the well seal using a cable clamp.
7.
Attach the supplemental information label at the electrical
installation site.
8.
Complete the electrical connections. Remember that a
capacitor or a control box should NEVER be connected to a
Redi-Flo3 submersible pump.
18. Starting the Pump for the First Time
When the pump has been connected correctly, the pump should be
started with the discharge valve closed approximately one-third. Due
to the soft start feature, the pump takes approximately 2 seconds to
develop full pressure.
Motor Cooling and Other Considerations
•
Make sure the well is capable of yielding a minimum quantity
of water corresponding to the pump capacity.
•
Do not start the pump until it is completely submerged in the
liquid.
•
As the valve is being opened, the drawdown should be checked to
ensure that the pump always remains submerged.
•
To ensure the necessary cooling of the motor, the pump should
never be set so low that it gives no water. If the flow rate
suddenly falls, the reason might be that the pump is pumping
more water than the well can yield.
Water Impurities
•
If there are impurities in the water, the valve should be opened
gradually as the water becomes clearer. The pump should not be
stopped until the water is clean, otherwise the pump parts and the
check valve may become clogged.
•
When the water is clean the valve should be fully opened.
Minimum flow rate
•
To ensure the necessary cooling of the motor, the pump flow rate
should never be set to a value lower than .2 gpm. If the flow rate
suddenly falls, the reason might be that the pump is pumping
more water than the well can yield.
Note:
The pump's dry-running protection is effective only within
the recommended duty range of the pump.
Note:
Do not let the pump run against a closed discharge valve for
more than 5 minutes. When the discharge valve is closed,
there is no cooling flow and there is a risk of overheating in
motor and pump.
Motor HP
Min. Generator Size (Watts)
1/3 - 1/2 A
1000
1/2 - 3/4 B
1700
1- 1
1
/
2
C
2000