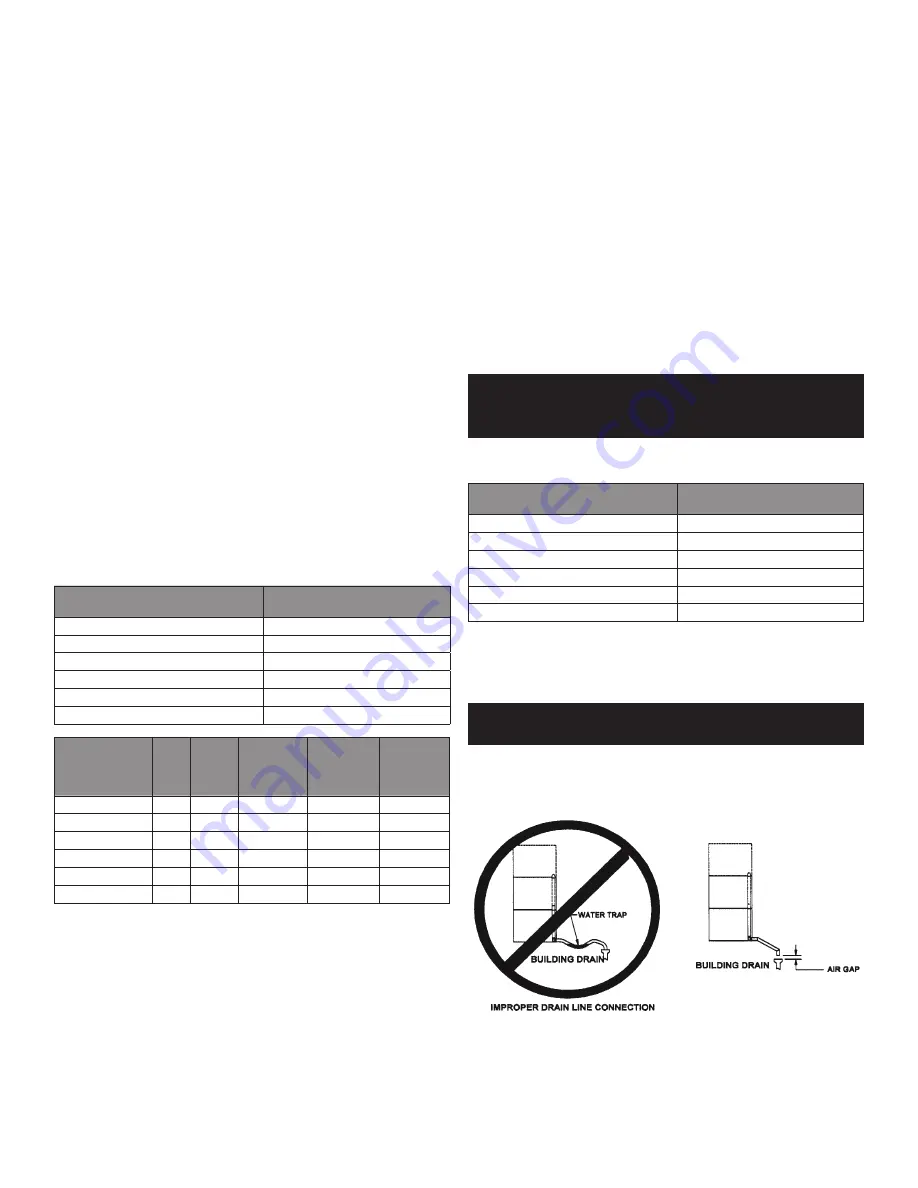
3
OM-GSSP-BL-G BOILERLESS STEAMER
the service compartment. Maximum load is 2-1/2 AMPs. In Canada, provide
electrical service in accordance with the Canadian Electrical Code, CSA C22.2 Part
1 and/or local codes.
1. Panel Removal (Right Side): Open the wiring and control panel by removing
screws from the right side panel. Lower panel below top cover panel. Pull
away toward the front of the unit. Slide panel and set aside.
2. Control Panel Removal: While right side panel is removed, carefully disconnect
harness from touchscreen display and on/off switch. Remove screws from
behind front panel and pull control panel away.
3. Supply Voltage: The unit must be operated at the rated name plate voltage. The
name plate can be found inside of the electrical compartment and outside of
the right access panel.
4. Terminal Block: The terminal block for incoming power is located at the back
of the control compartment. The ground terminal is located in the wiring
compartment near the terminal block.
5. Supply Wire: The equipment grounding wire must comply with the National
Electrical Code (NEC) requirements. The wiring diagram on the inside of the
unit’s right side cover gives directions for proper connection of the terminal
block jumpers. The wire must be used or the unit will not meet Underwriters
Laboratories and NEC requirements. The electric hole is sized for a 1/2 inch
conduit fitting.
6. Branch Circuit Protection: Each Boilerless Steamer, including individual units of
stacked models, should have its own branch circuit protection and ground wire.
7. On/Off Switch (in the rear): There is main power disconnect on the unit. It is
located on rear back panel above the entry hole for incoming electrical supply
wiring.
GAS SUPPLY CONNECTION
Connection to the gas supply shall be in accordance with the NPT and Ratings
charts below.
STEAMER
NPT Pipe Size Required
GSSP-BL-3G/GS
1/2
(2)GSSP-BL-3GS
1/2 x 2
GSSP-BL-5G/GS
1/2
(2)GSSP-BL-5G
1/2 x 2
GSSP-BL-10GS
1/2
(2)GSSP-BL-10GS
1/2 x 2
STEAMER
GAS
TYPE
BTU
Operating
Pressure
(Measured on
top of gas valve)
MIN
Incoming Gas
Feed Rate
MAX
Incoming Gas
Feed Rate
GSSP-BL-3G/GS
NG
54,000
4.3” WC
5” WC
14” WC
(2)GSSP-BL-3GS
LP
54,000
10.5” WC
12” WC
14” WC
GSSP-BL-5G/GS
NG
58,000
4.3” WC
5” WC
14” WC
(2)GSSP-BL-5G
LP
58,000
10.5” WC
12” WC
14” WC
GSSP-BL-10GS
NG
100,000
4.3” WC
5” WC
14” WC
(2)GSSP-BL-10GS
LP
100,000
10.5” WC
12” WC
14” WC
After the unit has been connected to the gas supply, all gas joints must be
checked for leaks. Do NOT use flame checking for leaks. A thick soap solution or
other suitable leak detector should be used.
For a Unit on casters:
1. The installation shall be made with a connector that complies with the
standard for connectors for movable gas appliances; ANSI Z21.69.CSA
6.16, and a quick disconnect device that complies with the standard for quick-
disconnect devices for use with gas fuel, ANSI Z21.41.CSA 6.9.
2. Adequate means must be provided to limit the movement of the appliance
without depending on the connector and the quick disconnect device or its
associated piping to limit the appliance movement.
3. The location where the restraining device may be attached to the
appliance shall be in accordance with Groen specifications for the device.
WATER CONNECTION(S)
Install a check valve to prevent back flow in the incoming cold water line, as
required by local plumbing codes. Water pressure in the line should be between 30
and 60 PSI. If pressure is above 60 PSI, a pressure regulator will be needed. These
pressures must provide the 1.5 gallons per minute required for proper steamer
function.
Dual water connection: A 3/4 inch female NH connector (garden hose type) is
used to attach the water supply to the inlet valve. Minimum inside diameter of the
water feed line is 1/2 inch. Use a washer in the hose connection. Do not allow the
connection to leak, no matter how slowly. Do not over-tighten hose connections.
This equipment is to be installed to comply with the basic plumbing code of the
Building Officials and Code Administrators International, Inc. (BOCA) and the Food
Service Sanitation Manual of the Food and Drug Administration (FDA).
NOTE: Local code may also require check valves in the water supply line.
DRAIN CONNECTION
WARNING: DO NOT CONNECT THE DRAIN DIRECTLY TO A BUILDING DRAIN. BLOCKING
THE DRAIN IS HAZARDOUS.
CAUTION: DO NOT USE PLASTIC PIPE. DRAIN MUST BE RATED FOR BOILING WATER.
Level the steamer front to back, and pitch it slightly to the rear (maximum 1/4 inch)
by adjusting the optional legs or the bullet feet on the optional stand.
STEAMER
Drain ID Hose Size
Required (IN)
GSSP-BL-3G/GS
1.5
(2)GSSP-BL-3GS
2.5
GSSP-BL-5G/GS
1.5
(2)GSSP-BL-5G
2.5
GSSP-BL-10GS
2
(2)GSSP-BL-10GS
2.5
There must be a free air gap between the end of the hose and the building drain.
The free air gap should be as close as possible to the unit drain. There must also be
no other elbows or restrictions between the unit drain and the free air gap.
Install the drain line with a constant downward pitch.
IMPORTANT: DO NOT ALLOW WATER TRAPS IN THE LINE. A TRAP CAN CAUSE PRESSURE
IN THE CAVITY, WHICH MAY CAUSE THE DOOR GASKET TO LEAK.
Proper Drain Line Connection –– Drain Line must have a constant downward pitch
of at least 1/4 per foot. Observe local code regarding air gap spacing and drain
connections.
FACTORY-STACKED UNITS
This section is applicable only if you are installing factory-stacked units. Installing
stacked steamers is similar to installing a single unit. The steamers are stacked
and assembled at the factory and delivered with the water connections and drain
hoses required for a single point connection.