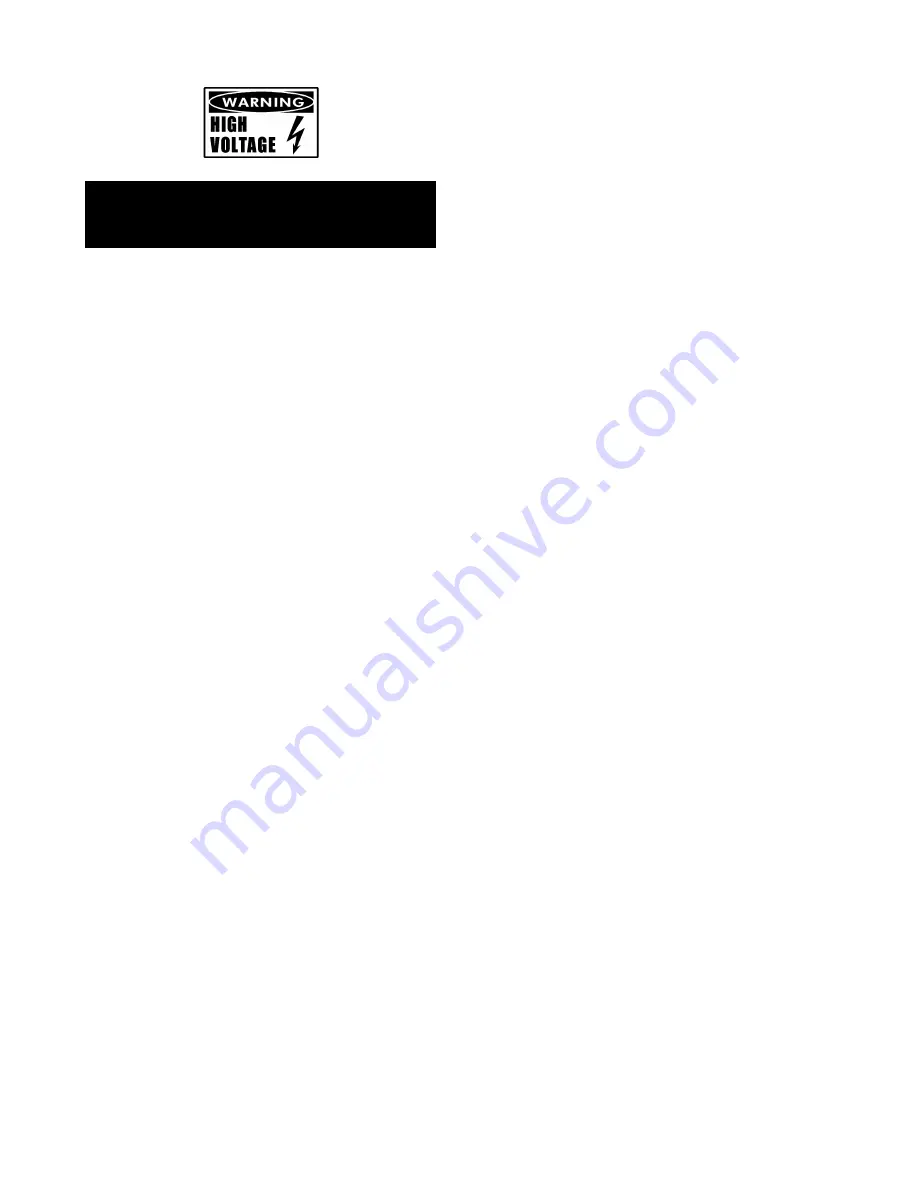
OM/SM-HY-3E & HY-5E(CE)
31
WARNING
DISCONNECT THE POWER SUPPLY BEFORE
BEGINNING ANY SERVICE PROCEDURE.
P. Steam Generator Drain Valve
P/N 071234
1.
Turn off power and disconnect steamer from
branch circuit. Remove right side panel and
top left side/cover.
2.
With a 5/16 inch nutdriver, remove the two
10-32 screws holding the valve bracket to
the steamer base on right side of unit.
3.
The steam generator drain valve is located
UNDER the cavity and all work should be
done from the left side of the steamer (as
viewed from the front).
4.
Using a 7mm nutdriver or spring clamp
pliers, disconnect ONE END of the drain
hose by loosening the drain hose clamp
from the drain elbow coming from the cavity
drain. Remove clamp.
5.
Unplug and disconnect the valve electrical
wires.
6.
Slide the valve support bracket out from
under the steam generator with the valve
attached to it. Allow the silicone hose to
leave the valve.
7.
Remove the two 10-32 screws from the
valve bracket, then remove valve from the
bracket.
To Install:
8.
Attach new drain valve to valve bracket. Pull
silicone hose through drain valve and install
hose clamp over one end of the exposed
hose and attach hose to drain elbow.
9.
Install and tighten valve mounting bracket
with two 10-32 screws. Be sure silicone hose
is properly aligned and does not have any
kinks, bends and/or twists in it.
10. Plug the electrical leads of the valve into the
wiring harness. Connect steamer to branch
circuit, and turn on power.
To Test:
Operate steamer and allow steam generator to fill.
Check for leaks and observe if drain valve fully
closes. Turn off steamer and observe that drain
valve opens and the steam generator drains.
11. Reinstall top/left side cover.
Q. Steam Generator
P/N 096836
1.
Shut off power to the steamer, drain steam
generator of all water. Remove right side
panel and top/left side cover.
2.
Remove the bracket of the high limit
thermostat switch and remove the two wires
which connect the unit to the wiring harness.
Leave thermostat attached to steam
generator.
3.
Remove the two 8-32 screws which hold the
water fill valve mounting plate to the steamer
back.
4.
Remove back panel by removing the six 10-
32 truss head screws
5.
Using a small adjustable wrench, remove
the drain hose brass compression nut
6.
Using a 5/16 nutdriver, loosen the clamps
holding steam and cleanout hoses. Detach
hoses from generator.
7.
Remove the two water level probe terminals
as indicated in Section N.
8.
Loosen hose clamp for drain hose under
cavity in order to gain access to the two 1/4-
20 kep nuts on the left side of the steam
generator.
9.
With an adjustable wrench, loosen the clamp
holding the water inlet hose to steam
generator. Remove hose from steam
generator.
10. Remove the four 1/4-20 kep nuts holding the
steam generator in position.