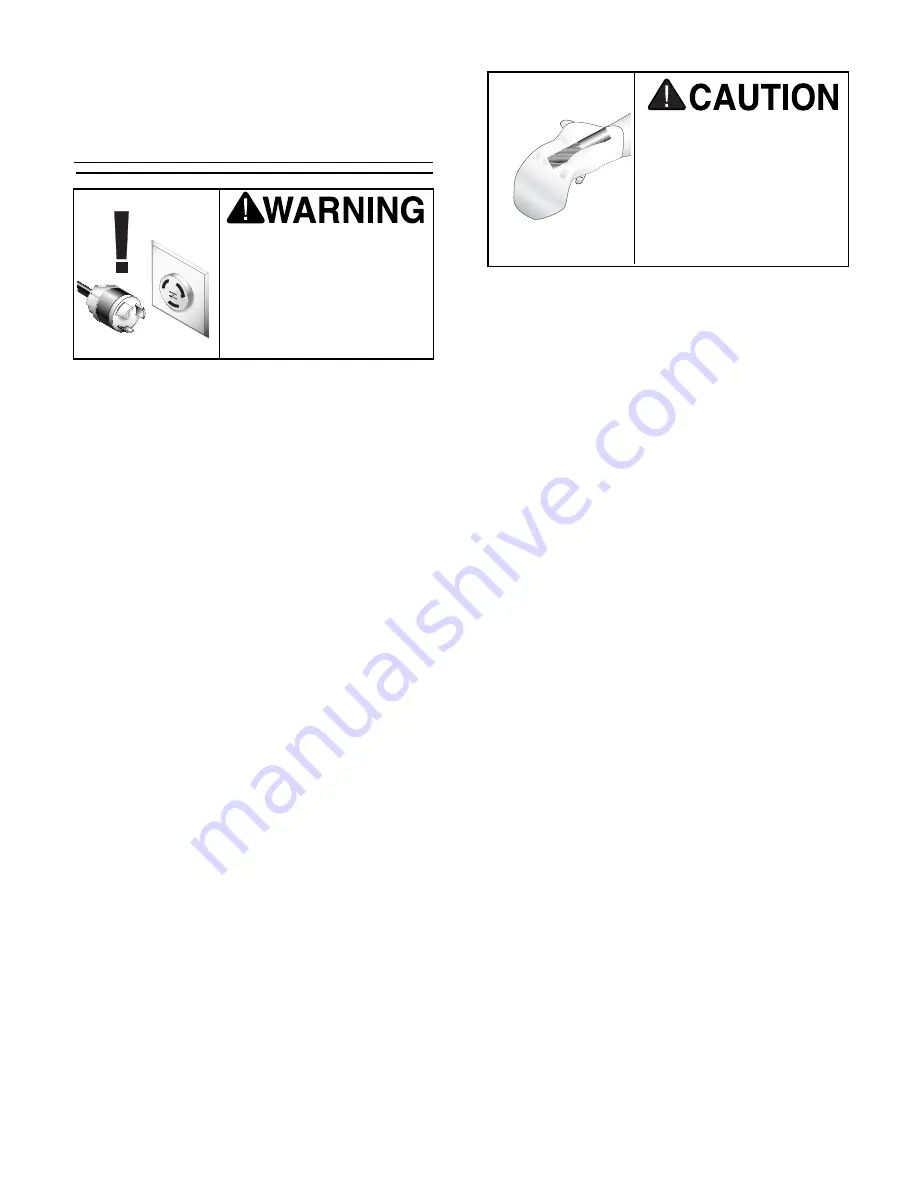
-13
-
4.
Turn the hex head at the top of the drawbar
(located on the top, front of the head) clock-
wise until the threads at the bottom of the
drawbar mesh with the female threads in
the top of the collet or arbor.
5.
When using a collet: Insert the cutter in the
hole at the bottom of the collet and contin-
ue to tighten the drawbar until both the col-
let and cutter are tightly in place.
Do not
over-tighten the collet. Grasp the rim of
the front pulley. Hold it tight while tight-
ening the draw bar.
G9959/G9977 Wood Mill
Cutting tools are sharp!
Be careful when
installing, removing or
handling all cutting
tools. Hold with shop
towel or gloves to avoid
severe cut or injury.
Disconnect the power
before changing collets
o r
a r b o r s
o n
t h e
Model
G9959/G9977.
Serious personal
injury may occur.
Collet or Arbor
Installation
The Model G9959/G9977 feature an R-8 spindle
which accepts any collets and arbors with the R-
8 designation.
To install a collet or an arbor:
1.
Release the latches on the head lid and
open it.
2.
Determine the location of the pin inside the
spindle.
3.
Align the collet keyway to the side where
you found the pin, and insert the collet or
cutting tool’s arbor up into the spindle hous-
ing. Rotate the collet slightly to line up the
key way with the pin in the spindle bore.