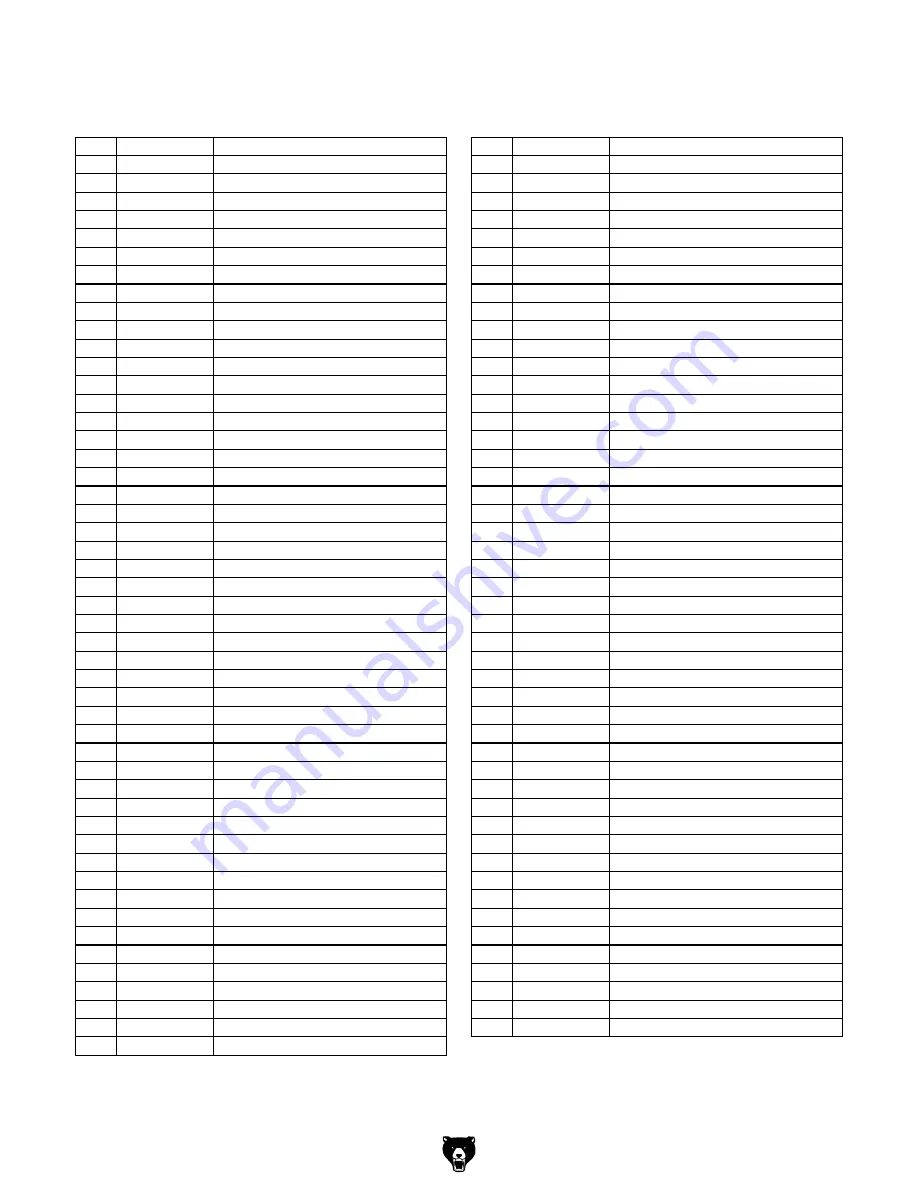
-56-
g0667X high precision Vs Vertical Mill
Head Parts List
REF PART #
DESCRIPTION
REF PART #
DESCRIPTION
101
P0667X0101
KNOB 3/8-16
150
P0667X0137A CLUSTER GEAR SHAFT 18/12T
102
P0667X0102
HANDLE
151
P0667X0137A FEED DRIVE CLUSTER GEAR 23T
103
P0667X0103
HANDLE HUB
152
P0667X0155A NEEDLE BEARING BZ66Z
104
P0667X0104
STEEL BALL 3/16
153
P0667X0153
REVERSE CLUTCH ROD
105
P0667X0105
COMPRESSION SPRING
154
P0667X0155A FEED REVERSE BUSHING
106
PSS05
SET SCREW 5/16-18 X 1/4
155A P0667X0155A FEED REVERSE GEAR ASSEMBLY
107
P0667X0107
PINION SHAFT SCREW
155
P0667X0155A FEED REVERSE BEVEL GEAR
108
P0667X0108
PINION SHAFT HUB SLEEVE
156
P0667X0156
FEED REVERSE CLUTCH
109
PSB33M
CAP SCREW M5-.8 X 12
157
P0667X0157
DOWEL PIN 3 X 20MM
110
P0667X0110
SPRING COVER
158
PR03M
EXT RETAINING RING 12MM
111
P0667X0111
COILED SPRING
159
P0667X0159
FEED WORM SHAFT BUSHING
112
PK155M
KEY 3 X 3 X 18
160
PK39M
KEY 3 X 3 X 10
113
P0667X0113
SPRING PIN
161
PK52M
KEY 3 X 3 X 15
114
P0667X0114
PINION GEAR SHAFT 10/16T
162
P0667X0162
FEED WORM SHAFT
115
PRIV001M
STEEL FLUTED RIVET 2 X 5MM
163
P0667X0163
FEED WORM SHAFT END CAP
116
P0667X0116
DATA PLATE
164
PSB06M
CAP SCREW M6-1 X 25
117
P0667X0117
ZERO SCALE
165
PSS01M
SET SCREW M6-1 X 10
118
P0667X0118
KNOB 1/4-20
166
P0667X0166
FEED GEAR SHIFTER FORK
119
P0667X0119
SHIFT CRANK
167
P0667X0167
CLUSTER GEAR SHIFT CRANK
120
PSS11
SET SCREW 1/4-20 X 1/4
168
P0667X0168
FEED SHIFT ROD
121
P0667X0121
COMPRESSION SPRING
169
P0667X0169
CLUSTER GEAR COVER
122
P0667X0122
INDENT PIN
170
P0667X0170
QUILL PINION SHAFT BUSHING
123
P0667X0123
SHIFT SLEEVE
171
P0667X0171
OVERLOAD CLUTCH GEAR 30T
124
P0667X0124
WORM GEAR CRADLE THROW-OUT
172
PR05M
EXT RETAINING RING 15MM
125
P0667X0125
WORM SHAFT
173A P0667X0173A OVERLOAD CLUTCH ASSEMBLY
126
PSS01M
SET SCREW M6-1 X 10
173
P0667X0173A OVERLOAD CLUTCH NUT
127
PK102M
KEY 4 X 4 X 18
174
P0667X0173A OVERLOAD CLUTCH
128
P0667X0128
WORM GEAR
175
P0667X0175
CLUTCH SPRING
129
P0667X0129
CLUSTER GEAR SHAFT CAP
176
PSS05M
SET SCREW M5-.8 X 10
130
P0667X0130
FEED CLUSTER GEAR 17/28/22T
177
P0667X0173A LOCK COLLAR
131
PR06M
EXT RETAINING RING 16MM
178
P0667X0178
CLUTCH RING
132
P0667X0132
BEVEL GEAR BUSHING
179
P0667X0179
CLUTCH WASHER
133
P0667X0133
BEVEL GEAR THRUST BUSHING
180
PR01M
EXT RETAINING RING 10MM
134
P0667X0134
FEED REVERSE BEVEL PINION
181
P0667X0181
CLUTCH RING SCREW
135
PK53M
KEY 3 X 3 X 45
182
P0667X0182
OVERLOAD CLUTCH TRIP LEVER
136
P0667X0137A FEED ENGAGE PIN
183
PRP03M
ROLL PIN 5 X 20
137A P0667X0137A WORM GEAR CRADLE ASSEMBLY
184
P0667X0184
CLUTCH ARM COVER
137
P0667X0137A WORM GEAR CRADLE
185
PSB79M
CAP SCREW M5-.8 X 35
138
PSS26M
SET SCREW M5-.8 X 6
186
PN05
HEX NUT 1/4-20
139
PSB04M
CAP SCREW M6-1 X 10
187
PSS06
SET SCREW 1/4-20 X 3/4
140
PW03M
FLAT WASHER 6MM
188
P0667X0188
COMPRESSION SPRING
141
P0667X0137A WORM GEAR SPACER
189
P0667X0189
OVERLOAD CLUTCH PLUNGER
142
P0667X0137A FEED DRIVE WORM GEAR 20T
190
P0667X0190
OIL CUP
143
P0667X0137A WORM CRADLE BUSHING
191
P0667X0191
FEED TRIP PLUNGER BUSHING
144
PK103M
KEY 3 X 3 X 12
192
P0667X0192
FEED TRIP PLUNGER
145
P0667X0137A FEED REVERSE BEVEL PINION
193
P0667X0193
FEED TRIP LEVER
146
PSB30
CAP SCREW 5/16-18 X 1/2
194
P0667X0194
FEED TRIP LEVER PIN
147
PW07
FLAT WASHER 5/16
195
PN04M
HEX NUT M4-.7
148
P0667X0137A FEED REVERSE BEVEL GEAR 24T
196
PSS49M
SET SCREW M4-.7 X 16
149
PK03M
KEY 3 X 3 X 8