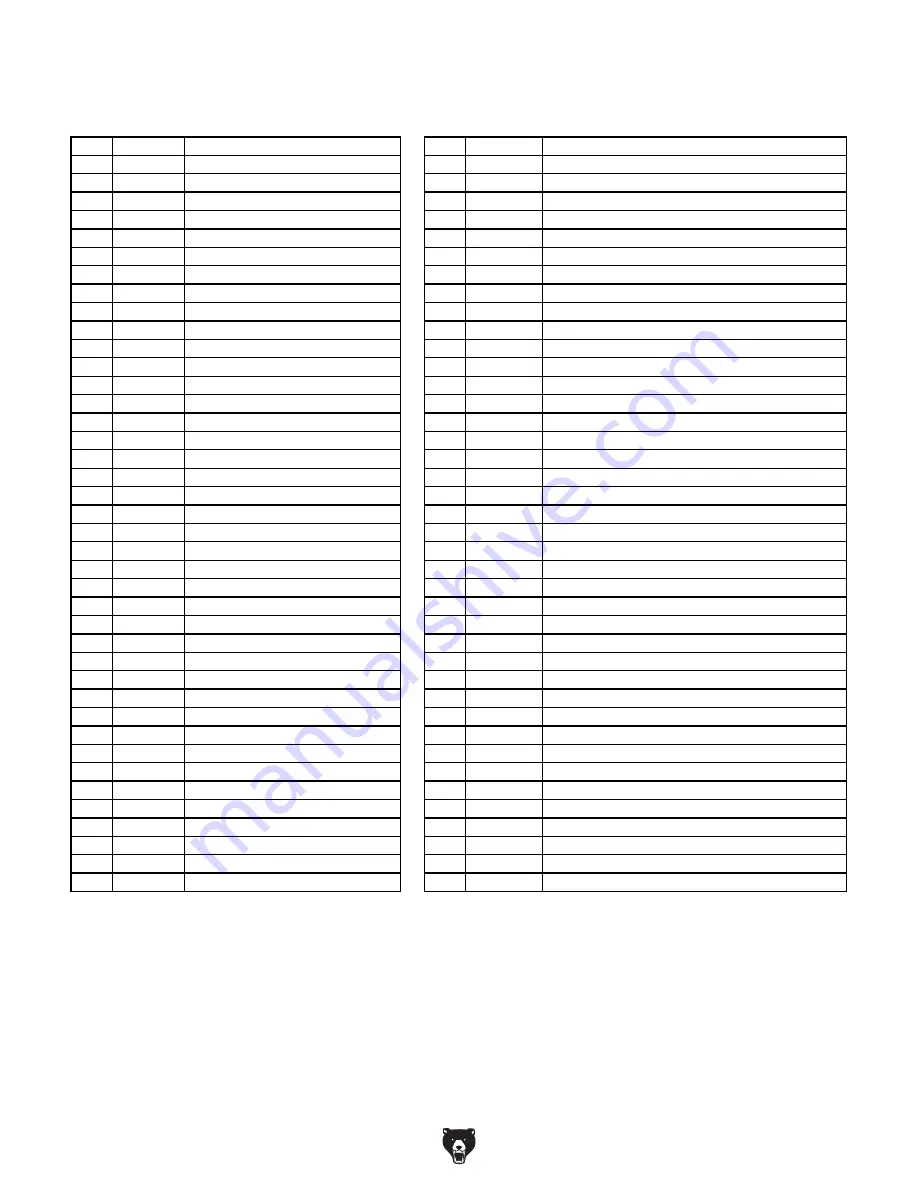
Model G9983 (Mfg. Since 8/09)
-49-
sanding belt drive system parts list
REF PART #
DESCRIPTION
REF PART #
DESCRIPTION
301
P9983301 CONTACT ROLLER BASE
342
PR11M
EXT RETAINING RING 25MM
302
PLW06M
LOCK WASHER 10MM
343
PR25M
INT RETAINING RING 47MM
303
PCAP72M CAP SCREW M10-1.5 X 30
344
P6005ZZ
BALL BEARING 6005ZZ
304
P9983304 SWITCH PLATE
345A P9983345A CONTACT ROLLER ASSEMBLY
305
PW04M
FLAT WASHER 10MM
346
P9983346
ROLLER SHAFT
306
PLW06M
LOCK WASHER 10MM
347
P9983347
SLEEVE
307
PCAP72M CAP SCREW M10-1.5 X 30
348
PR11M
EXT RETAINING RING 25MM
308
P9983308 COVER
349
PR25M
INT RETAINING RING 47MM
309
PS02M
PHLP HD SCR M4-.7 X 12
350
P6005ZZ
BALL BEARING 6005ZZ
310
PLW04M
LOCK WASHER 8MM
351
P9983351
SUPPORT ROLLER
311
PB07M
HEX BOLT M8-1.25 X 25
352
P9983352
ROLLER SHAFT
312
P9983312 FORK
353
P9983353
BUSHING
313
PW03M
FLAT WASHER 6MM
354
P9983354
ROLLER BASE
314
PS14M
PHLP HD SCR M6-1 X 12
355
P9983355
MICROMETER BASE
315
P9983315 CYLINDER ROLLER FRAME
356
PCAP26M
CAP SCREW M6-1 X 12
316
PSS04M
SET SCREW M6-1 X 12
357
P9983357
MICROMETER
317
P9983317 SUPPORT TUBE
358
PSS04M
SET SCREW M6-1 X 12
318
PLW04M
LOCK WASHER 8MM
359
P9983359
MAIN WORM GEAR SHAFT
319
PCAP76M CAP SCREW M8-1.25 X 18
360
P9983360
CONNECTION COUPLING
320
P9983320 TOP ROLLER SUPPORT LH
361
PSS04M
SET SCREW M6-1 X 12
321
PLW04M
LOCK WASHER 8MM
362
P9983362
SUPPORT WORM GEAR SHAFT
322
PCAP76M CAP SCREW M8-1.25 X 18
363
P9983363
GRAPHITE BASE LH
323
P9983323 TOP ROLLER SUPPORT RH
364
P9983364
GRAPHITE BASE RH
324
PSS04M
SET SCREW M6-1 X 12
365
P9983365
WORM GEAR
325
P9983325 KNOB BOLT M8-1.25 X 80
366
P9983366
GEAR BUSHING
326
P9983326 ECCENTRIC SHAFT
367
PLW04M
LOCK WASHER 8MM
327
PR11M
EXT RETAINING RING 25MM
368
PB03M
HEX BOLT M8-1.25 X 16
328
P6205ZZ
BALL BEARING 6205ZZ
369
P9983369
VERT MICROMETER SCREW M18-2.8 & M10-1.5
329
P9983329 TOP ROLLER
370
P9983370
PLATEN (MALE)
330
P9983330 TOP ROLLER SHAFT
371
PW01M
FLAT WASHER 8MM
331
P9983331 TOP COVER
372
PCAP58M
CAP SCREW M8-1.25 X 12
332
P99796315 GASKET
373
P9983373
PLATEN (FEMALE)
333
PFH02M
FLAT HD SCR M6-1 X 12
374
P9983374
GRAPHITE CLOTH 3-3/8"W X 16-1/4"L
334
P9983334 SPRING COVER
375
P9983375
SET PLATE
335
P9983335 SHAFT
376
PW05M
FLAT WASHER 4MM
336
P9983336 COMPRESSION SPRING D25 X 24
377
PS02M
PHLP HD SCR M4-.7 X 12
337
P9983337 BOTTOM COVER
378
P9983378
LINING
338
PS06M
PHLP HD SCR M5-.8 X 20
379
PLW07M
LOCK WASHER 20MM
339
PR05M
EXT RETAINING RING 15MM
380
PN17M
HEX NUT M20-1.5
340
PN02M
HEX NUT M10-1.5
381
P9983381
SANDING BELT #180 16 X 48"
341
P9983341 OSCILLATION SQUARE
381-1 P9983381-1 SANDING BELT #240 16 X 48"
Summary of Contents for G9983
Page 60: ......