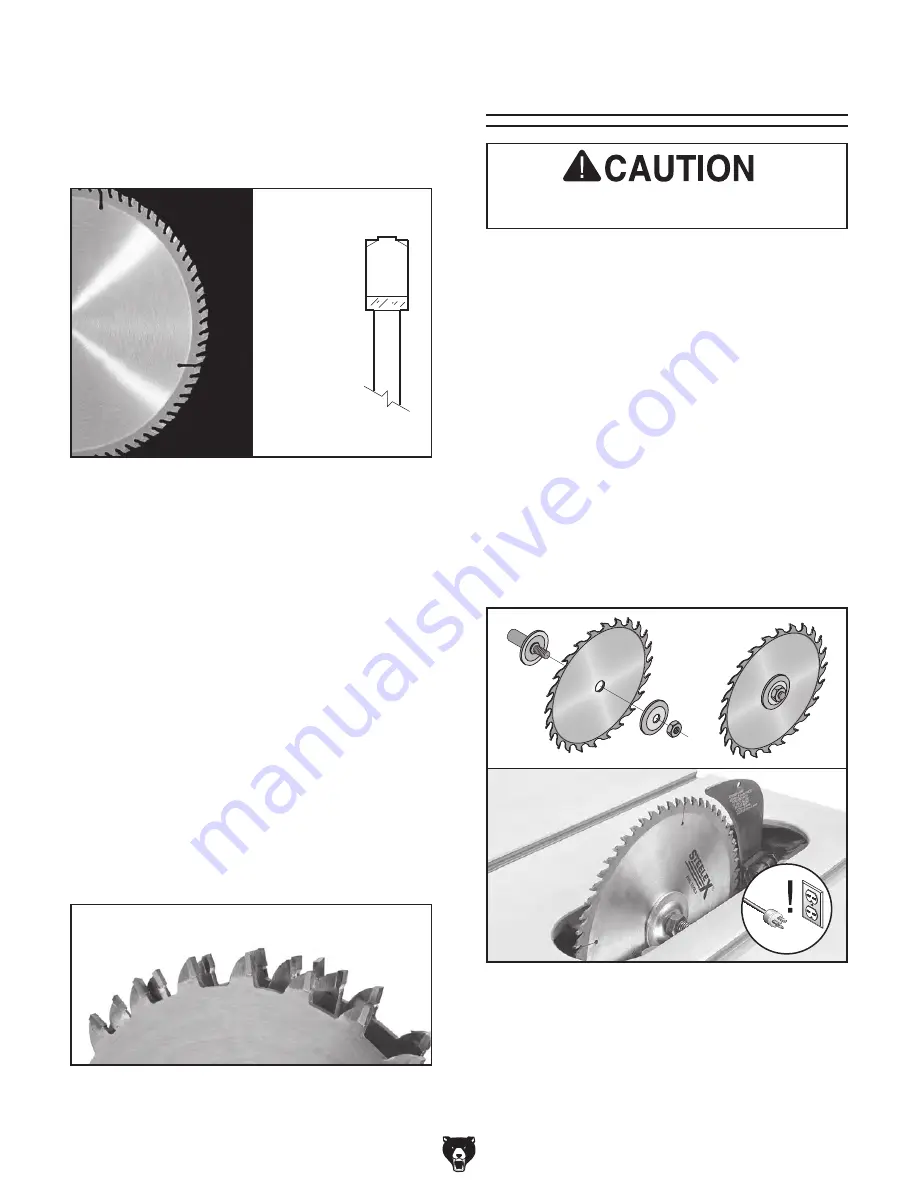
-30-
Model G1023RL Series (Mfd. Since 12/11)
Blade Installation
The saw blade is sharp. Use extra care and
wear gloves when installing the blade.
Figure 37. Laminate blade.
Laminate blade features:
•
Best for cutting plywood or veneer
•
40-80 teeth
•
Triple chip tooth profile
•
Very shallow gullet
Triple
Chip
Blade
Thin Kerf Blade: A blade with thinner kerf than
a standard blade. Since the spreader/riving knife
included with this table saw is sized for standard
blades, thin kerf blades cannot be used on this
saw unless they meet the
Blade Requirements
specified in this manual; otherwise, they will
increase the risk of kickback.
Figure 38. Stacked dado blade.
Dado Blades
Stacked Dado Blade (see below): Multiple
blades are stacked together to control the cutting
width. Stacked dado blades are more expensive
than wobble blades, but typically produce higher
quality results.
Wobble Dado Blade: A single blade mounted at
a slight angle on an arbor hub. The blade angle is
adjustable on the hub, and the width of the dado
cut is controlled by the angle setting of the blade.
To install a new blade:
1. DISCONNECT SAW FROM POWER!
2. Raise the arbor all the way up, and remove
the table insert and blade guard/riving knife,
depending on what is installed.
3. Use the arbor wrenches to loosen and remove
the arbor nut, flange, and blade. The arbor
nut has right hand threads; turn it counter-
clockwise to loosen.
4. Install the new blade and flange on the arbor,
as shown in
Figure 39, with teeth facing the
front of the saw. Securely tighten the arbor
nut.
Figure 39. Blade order of installation and teeth
facing the correct direction.
5. Re-install the blade guard and table insert.