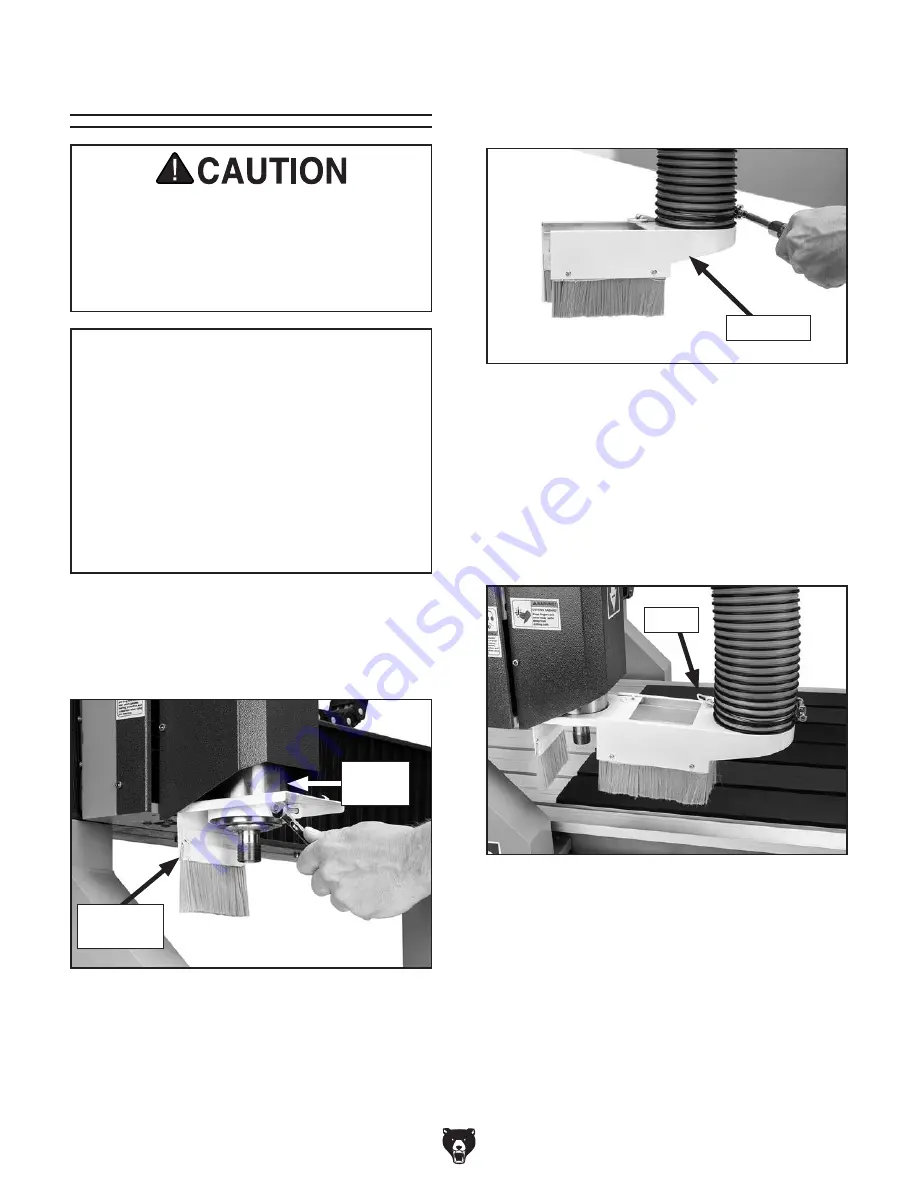
-20-
Model G0894 (Mfd. Since 05/19)
Dust Collection
To connect dust collection system to machine:
1. Attach dust shoe bracket to spindle motor
(see
Figure 15).
Minimum CFM at Dust Port: 400 CFM
Do not confuse this CFM recommendation with
the rating of the dust collector. To determine the
CFM at the dust port, you must consider these
variables: (1) CFM rating of the dust collector,
(2) hose type and length between the dust col-
lector and the machine, (3) number of branches
or wyes, and (4) amount of other open lines
throughout the system. Explaining how to cal-
culate these variables is beyond the scope of
this manual. Consult an expert or purchase a
good dust collection "how-to" book.
This machine creates a lot of wood chips/
dust during operation. Breathing airborne
dust on a regular basis can result in perma-
nent respiratory illness. Reduce your risk
by wearing a respirator and capturing the
dust with a dust-collection system.
2. Fit 4" dust hose over dust shoe, as shown
in
Figure 16, and secure in place with hose
clamp.
Figure 15. Attaching dust shoe bracket.
Spindle
Motor
Dust Shoe
Bracket
3. Tug hose with light/medium force to make
sure it does not easily come off.
Note: A tight fit is necessary for proper per-
formance.
4. Slide dust shoe onto bracket (see Figure 17)
and secure in place with latch.
Figure 16. Tightening dust hose clamp.
Dust Shoe
Figure 17. Dust shoe attached.
Latch
Summary of Contents for G0894
Page 48: ......