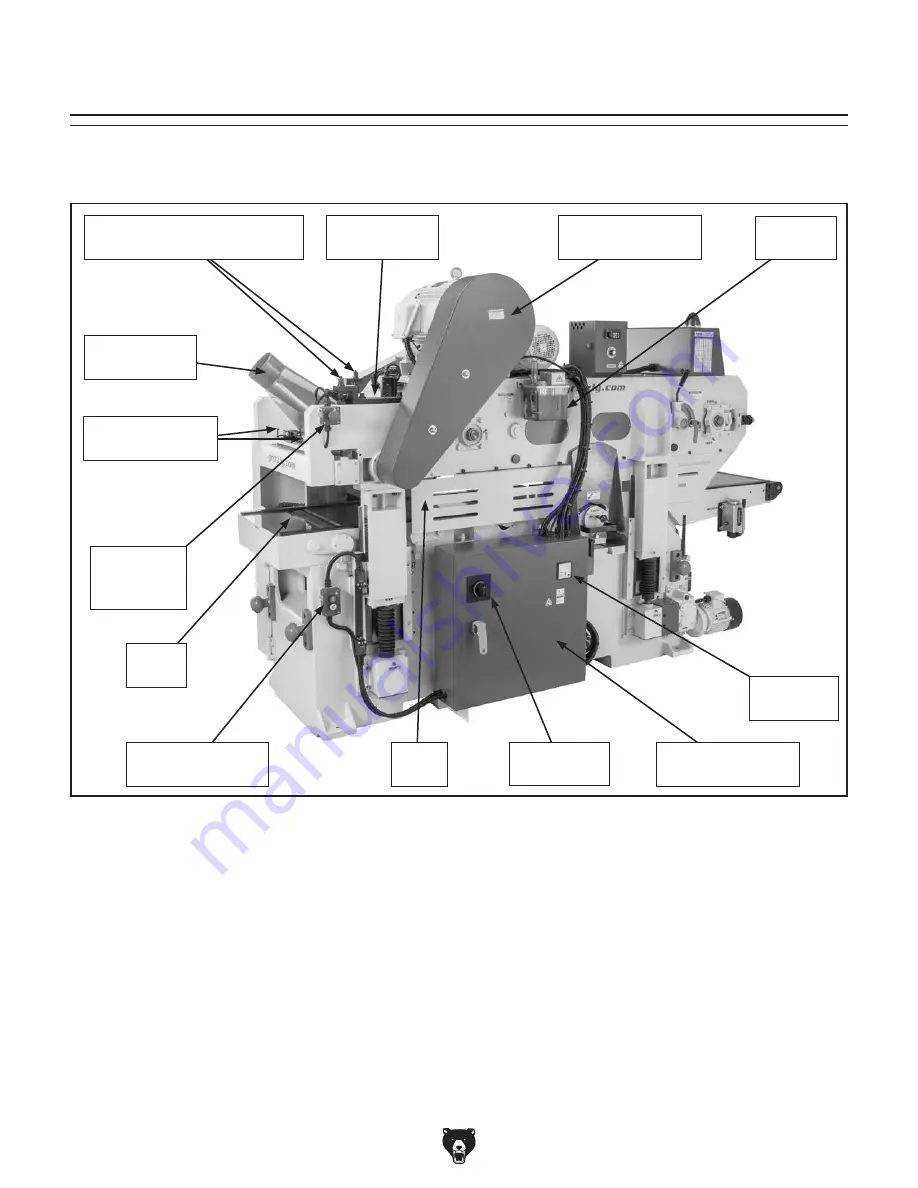
-4-
Model G0841 (Mfd. Since 06/18)
Identification (Rear)
Become familiar with the names and locations of the controls and features shown below to better understand
the instructions in this manual.
Machine
Amp Meter
Planer
Table
Automatic
Oiler
Chip Breaker
Access Cover
Pressure Bar
Adjustment Bolts
Emergency
Stop Button
(1 of 2)
Electrical Panel w/
Lock-Out Handle
Table
Guard
Adjustment Rods for
Serrated & Pressure Rollers
Dust Hood w/
5" Dust Port
Upper Cutterhead
Belt Cover
Headstock Height
Switch (1 of 2)
Main Power
Switch
Summary of Contents for G0841
Page 84: ......