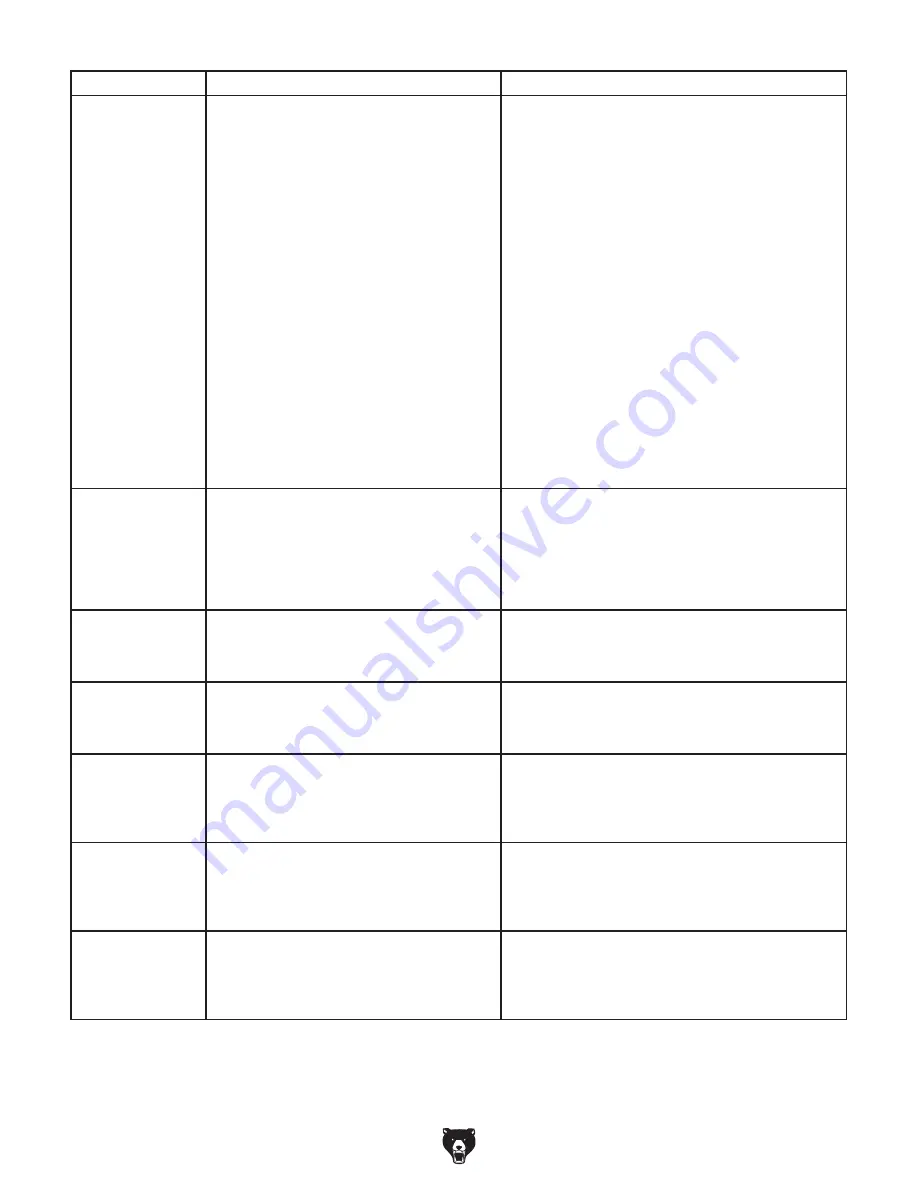
-30-
Model G0727 (Mfg. Since 7/11)
Symptom
Possible Cause
Possible Solution
Machine has
vibration or noisy
operation.
1. Motor or component is loose.
2. Motor-spindle assembly is loose.
3. Arbor/tool is loose.
4. Belt pulley is loose.
5. Motor mount loose/broken.
6. Machine is incorrectly mounted or sits
unevenly.
7. Workpiece is loose.
8. Cutter is at fault.
9. Bit is chattering.
10. Motor bearings are at fault.
1. Inspect/replace stripped or damaged bolts/nuts,
and re-tighten with thread locking fluid.
2. Tighten spindle lock collar cap screw (see
Page 21).
3. Fully seat arbor/tool by tightening drawbar (see
Page 23).
4. Replace shaft, pulley, setscrew, and key as
required.
5. Tighten/replace.
6. Tighten/replace mounting fasteners; relocate/shim
machine.
7. Use the correct holding fixture and re-clamp
workpiece.
8. Replace out-of-round cutter; replace/resharpen
cutter; use appropriate feed rate and cutting
speed.
9. Replace/sharpen bit; index bit to workpiece; use
appropriate feed rate and spindle speed.
10. Test by rotating shaft; rotational grinding/loose
shaft requires bearing replacement.
Tool slips in collet.
1. Collet is not fully drawn up into spindle
taper.
2. Wrong size collet.
3. Debris in collet or in spindle taper.
4. Taking too big of a cut.
1. Fully seat collet by tightening drawbar (see
Page 23).
2. Measure tool shank diameter and match with
appropriate diameter collet.
3. Remove oil or debris from collet and spindle taper.
4. Lessen depth of cut and allow chips to clear.
Breaking tools or
cutters.
1. Spindle speed or feed rate is too fast.
2. Cutting tool getting too hot.
3. Taking too big of a cut.
1. Set correct spindle speed and feed rates.
2. Use coolant fluid; reduce feed rate or spindle
speed.
3. Lessen depth of cut and allow chips to clear.
Machine is loud
when cutting.
Overheats or bogs
down in the cut.
1. Excessive depth of cut.
2. Dull cutting tools.
1. Decrease depth of cut.
2. Use sharp cutting tools.
Workpiece vibrates
or chatters during
operation.
1. Table locks not tight.
2. Workpiece not securely clamped to table
or into mill vice.
3. Spindle speed and feed rate too high.
1. Tighten down table locks.
2. Check that clamping is tight and sufficient for the
job. Make sure mill vice is tight to the table.
3. Use appropriate spindle speed and feed rate for
the job.
Table hard to move. 1. Table locks are tightened down.
2. Chips have loaded up on ways.
3. Ways are dry and in need of lubrication.
4. Gibs are too tight.
1. Make sure table locks are fully released.
2. Frequently clean away chips that load up during
milling operations.
3. Lubricate ways.
4. Adjust gibs (see
Page 32).
Bad surface finish.
1. Wrong spindle speed or feed rate.
2. Dull cutting tool or poor cutting tool selec-
tion.
3. Cutting tool installed incorrectly.
4. Workpiece not securely clamped.
1. Adjust for appropriate spindle speed and feed rate.
2. Sharpen cutting tool or select a better cutting tool
for the intended operation.
3. Properly install cutting tool for spindle direction.
4. Secure properly.
Summary of Contents for G0727
Page 48: ......