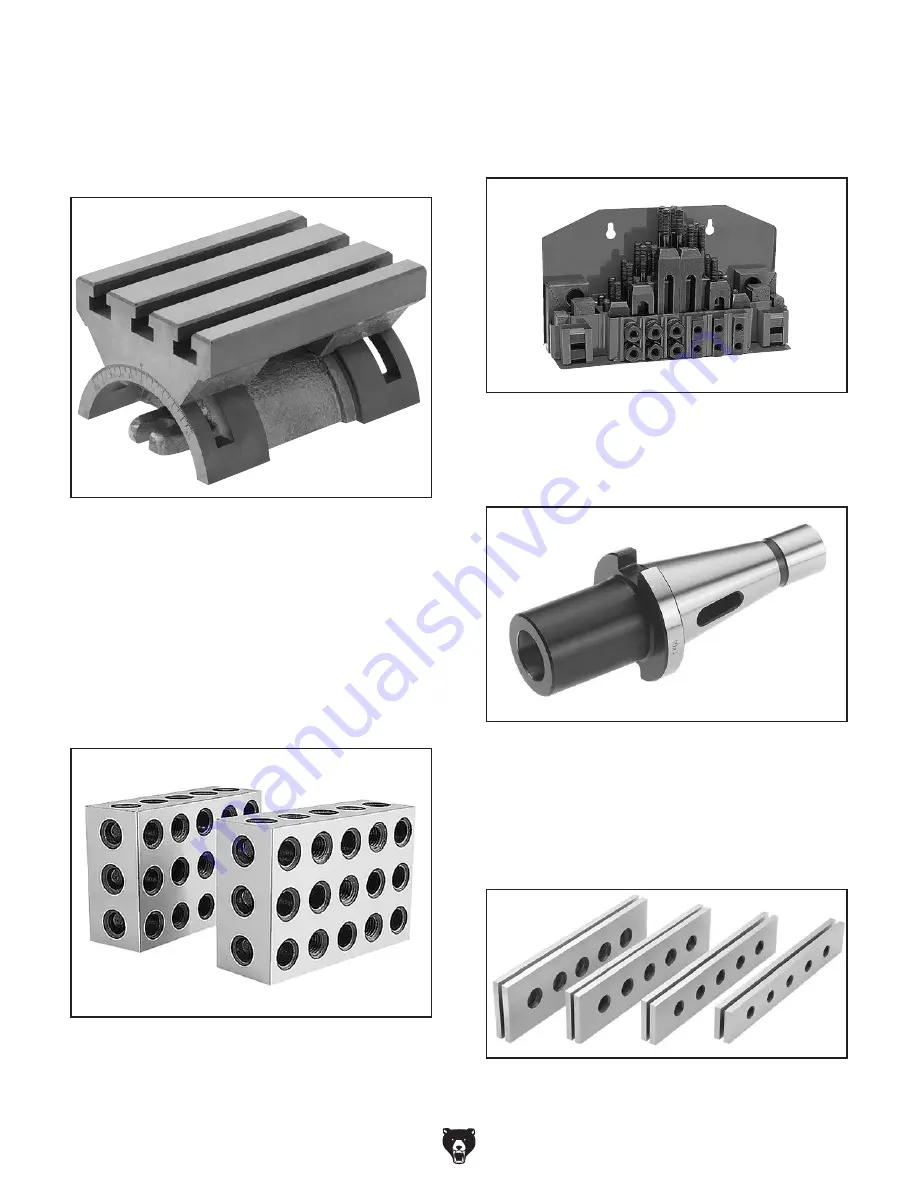
Model G0726 (Mfg. Since 7/11)
-43-
H5802—NT40 to MT#2 Sleeve
H5803—NT40 to MT#3 Sleeve
H8139—NT40 to R8 Adapter
Figure 60. NT40 Sleeves and Adapter.
G5758—5" x 7" Tilt Table
G5759—7" x 10" Tilt Table
Set your work at any angle from –45° to +45° with
these sturdy Tilt Tables. Heavy-duty construction
includes T-slots, two locking screws, and preci-
sion base with a scale.
Figure 57. Tilt Table.
G5641—1-2-3 Blocks
G5642—2-4-6 Blocks
These blocks are extremely handy for layout and
set up work. Matched blocks are hardened and
precision ground so all six sides are square to
within 0.0003". These blocks also feature five
tapped holes and 18 untapped holes for clamping.
Sold in pairs. G5641 tapped holes are
3
⁄
8
"-16, and
overall size is 1" x 2" x 3". G5642 tapped holes are
5
⁄
8
" 11, and overall size is 2" x 4" x 6".
Figure 58. 1-2-3 and 4-5-6 Blocks.
G5678— Steel Parallel Sets
3
⁄
16
" Thickness
G5678— Steel Parallel Sets
1
⁄
2
" Thickness
These ground and hardness sets feature four
pairs of 6" long parallels which are accurate
to within 0.0003" in parallelism and 0.0002" in
height.
G1076—52-PC. Clamping Kit for
5
⁄
8
" T-Slots
This clamping kit includes 24 studs, 6 step block
pairs, 6 T-nuts, 6 flange nuts, 4 coupling nuts, and
6 end hold-downs. The rack is slotted so it can be
mounted close to the machine for easy access.
Figure 59. G1076 52-PC. Clamping Kit.
Figure 61. Steel parallel sets.
order online at
www.grizzly.com
or call
1-800-523-4777