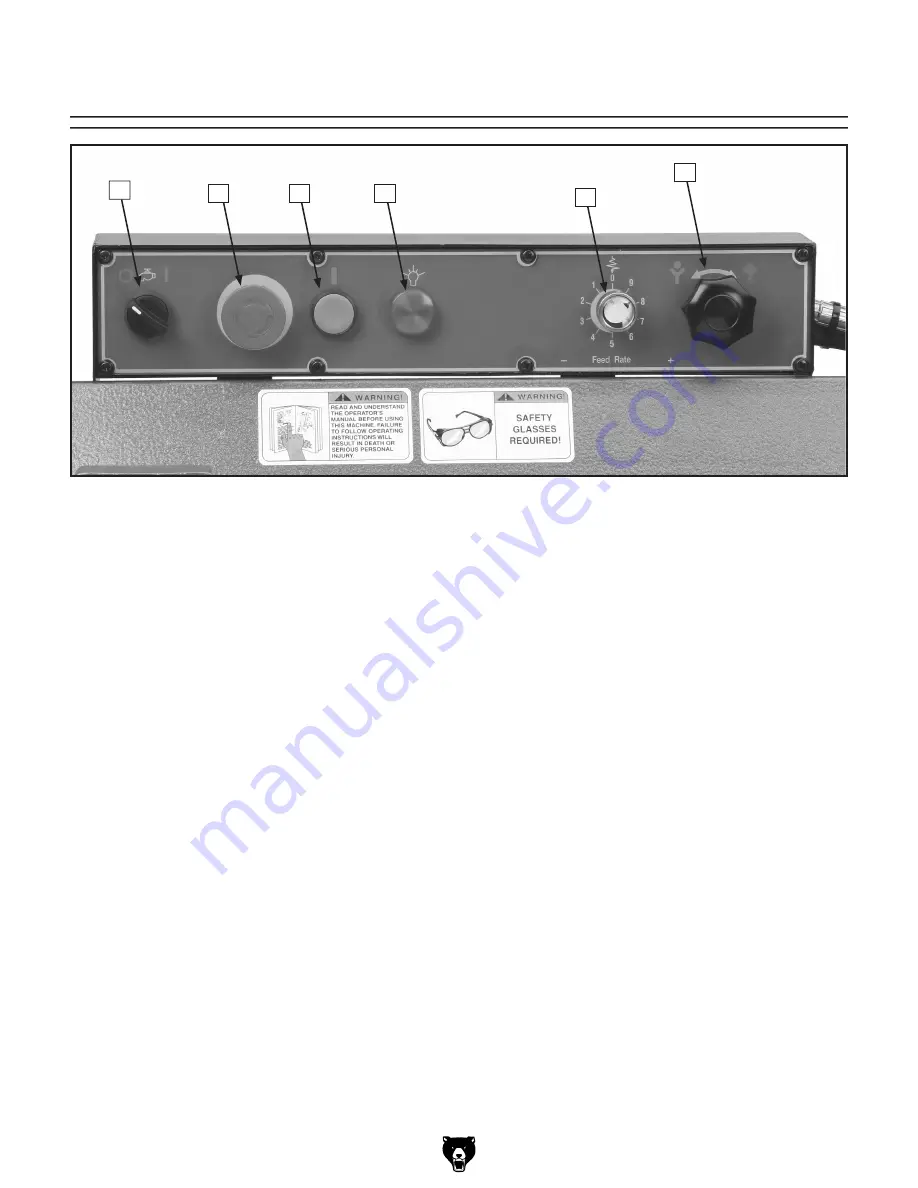
G0592 Metal Cutting Bandsaw
-7-
Control Panel
A. Coolant Pump Switch:
Turns the coolant
pump
ON.
B. EMERGENCY
STOP/OFF Button:
Interrupts
power to the system and turns the motor
OFF
. Twist the button until it pops out to re-
energize the system. Also works as a stan-
dard OFF button.
Note:
The bandsaw has an automatic shut-
off (limit switch) that turns the machine
OFF
at the completion of the cutting arc.
C. START Button:
Turns the motor
ON
and
activates moving parts.
D. Power Light:
When lit, indicates that system
is energized and machine is ready to oper-
ate.
E.
Feed Rate Dial:
Fine tunes the feed rate by
controlling the hydraulic valve. Range is from
1 being slowest to 9 being fastest.
F. Feed Control Knob:
Turning the knob to the
left lowers the bow at the feed rate you have
set. Turning the knob to the right locks the
bow in position.
Figure 2.
G0592 control panel.
A
B
C
D
E
F
Summary of Contents for G0592
Page 2: ... ...
Page 16: ... 14 G0592 Metal Cutting Bandsaw Hardware Recognition Chart ...
Page 41: ...G0592 Metal Cutting Bandsaw 39 Model G0592 220V Wiring Diagram ...
Page 42: ... 40 G0592 Metal Cutting Bandsaw Base Parts Breakdown ...
Page 44: ... 42 G0592 Metal Cutting Bandsaw Swivel Base Parts Breakdown ...
Page 46: ... 44 G0592 Metal Cutting Bandsaw Vise Parts Breakdown ...
Page 48: ... 46 G0592 Metal Cutting Bandsaw Bow Parts Breakdown ...
Page 50: ... 48 G0592 Metal Cutting Bandsaw Blade Tension Motor Parts Breakdown ...
Page 52: ... 50 G0592 Metal Cutting Bandsaw Blade Guides Parts Breakdown ...
Page 54: ... 52 G0592 Metal Cutting Bandsaw Electrical Parts Breakdown ...
Page 57: ... ...
Page 58: ... ...
Page 59: ......
Page 60: ... ...