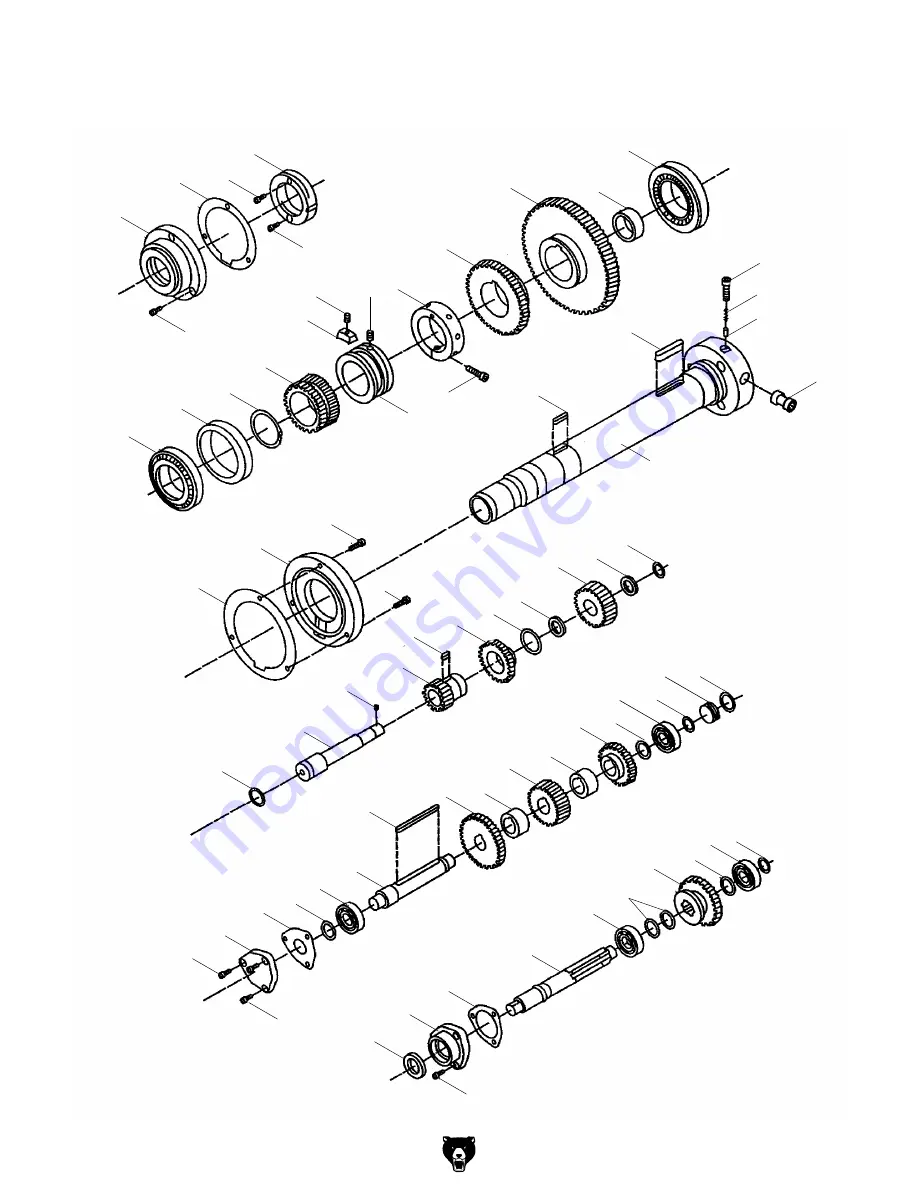
g0554 gear-head Floor lathe
-59-
&&&
&&'
&&(
&&(
&&)
&&%
&%(
H
H
&*-
&&*
&&+
&+&
&+'
&+( &&,
&+%
&&.
&'*
&')
&'(
&'*
&(-
&(.
&)%
&)&
H
&(,
&(+
&()
&)'
8
9
:
*+
-.
.%
&((
-'
&*&
&)(
&)) &)*
&)+
&),
&)- .*
&). &((
&(* &()
&((
&('
&'+
&',
&(&
&(%
&'.
&'-
&'&
&''
&'%
&&-
&*% &)'
&*)
&**
*+
*+
&*(
.+
,)
&*' ,)
&). &((
&*+
Headstock Assembly
Summary of Contents for G0554
Page 61: ...G0554 Gear Head Floor Lathe 57 A A B C E E Headstock Assembly...
Page 62: ...58 G0554 Gear Head Floor Lathe 6 7 Headstock Assembly...
Page 63: ...G0554 Gear Head Floor Lathe 59 H H H 8 9 Headstock Assembly...
Page 66: ...62 G0554 Gear Head Floor Lathe 9 8 7 6 Gearbox Assembly...
Page 67: ...G0554 Gear Head Floor Lathe 63 Gearbox Assembly...
Page 68: ...64 G0554 Gear Head Floor Lathe Gearbox Assembly...
Page 82: ...78 G0554 Gear Head Floor Lathe Stand Breakdown...
Page 84: ...80 G0554 Gear Head Floor Lathe 8 Vc Z ZVg 8 Vc Z ZVg ZVYhidX ZVgWdm End Gear Assembly...
Page 86: ...82 G0554 Gear Head Floor Lathe Steady Follow Rest Assemblies...
Page 93: ......