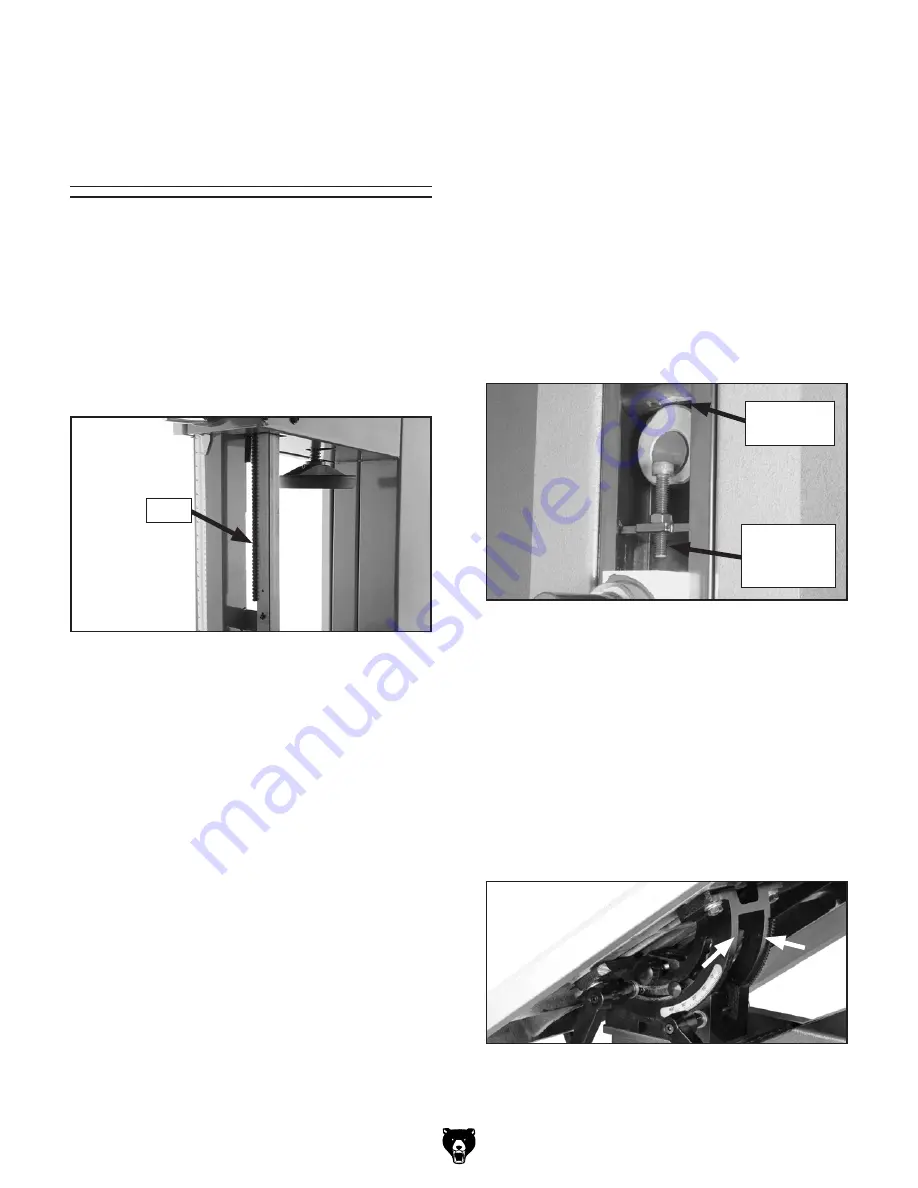
Model g0513X2B (Mfg. since 5/11)
-15-
to lubricate the tension adjustment assem-
bly:
1. disConneCt BAndsAW FroM poWer!
2. open the top wheel cover and look through
the top of the wheel.
3. Wipe off any existing grease and sawdust
buildup on the blade tension adjustment
assembly and tension lever cam.
4. Apply a thin coat of grease to the tension
adjustment assembly and tension lever cam
(see
figure 12).
figure 12. tension adjustment assembly
locations (top wheel removed for clarity).
to lubricate the trunnions:
1. disConneCt BAndsAW FroM poWer!
2. Move the table up until it reaches its maximum
45˚ angle and wipe off all excess grease and
sawdust from the trunnions.
3. Apply a thin coat of light all purpose grease to
the trunnions (see
figure 13).
figure 13. trunnion lubrication location.
4. Move the table down and up to distribute the
grease, then wipe off any excess grease.
to lubricate the blade guide rack and pinion:
1. disConneCt BAndsAW FroM poWer!
2. lower the blade guide until it reaches the
table.
3. Wipe off any existing grease and sawdust
buildup on the rack (see
figure 11).
figure 11. rack lubrication location.
4. Apply a thin coat of light all-purpose grease to
the rack.
5. Move the blade guide up and down several
times to distribute the grease, then remove
any excess grease to help prevent sawdust
buildup.
to lubricate the blade tracking knob:
1. disConneCt BAndsAW FroM poWer!
2. loosen the blade tracking lock lever, then
unscrew the blade tracking knob 5 turns.
3. Wipe off any existing grease and sawdust
buildup on the threads.
4. Apply a few dabs of a light all-purpose grease
to the threads.
5. re-adjust tracking (see blade tracking on
g0513X Manual
page 22).
(Replaces
Lubrication on Page
45)
rack
tension
lever Cam
tension
Adjustment
Assembly
Summary of Contents for EXTREME G0513X2B
Page 30: ......
Page 48: ...18 G0513X G0514X G0514X3 Extreme Series Bandsaw Hardware Recognition Chart...
Page 84: ...54 G0513X G0514X G0514X3 Extreme Series Bandsaw G0513X Wiring Diagram G0513X Wiring Diagram...
Page 86: ...56 G0513X G0514X G0514X3 Extreme Series Bandsaw G0514X Wiring Diagram...
Page 88: ...58 G0513X G0514X G0514X3 Extreme Series Bandsaw G0514X3 Wiring Diagram G0514X3 Wiring Diagram...
Page 89: ...G0513X G0514X G0514X3 Extreme Series Bandsaw 59 G0513X Main Parts...
Page 90: ...60 G0513X G0514X G0514X3 Extreme Series Bandsaw G0513X Fence Guide Parts...
Page 94: ...64 G0513X G0514X G0514X3 Extreme Series Bandsaw G0514X G0514X3 Main Parts...
Page 95: ...G0513X G0514X G0514X3 Extreme Series Bandsaw 65 G0514X G0514X3 Fence Guide Parts...
Page 101: ......
Page 102: ......
Page 103: ......