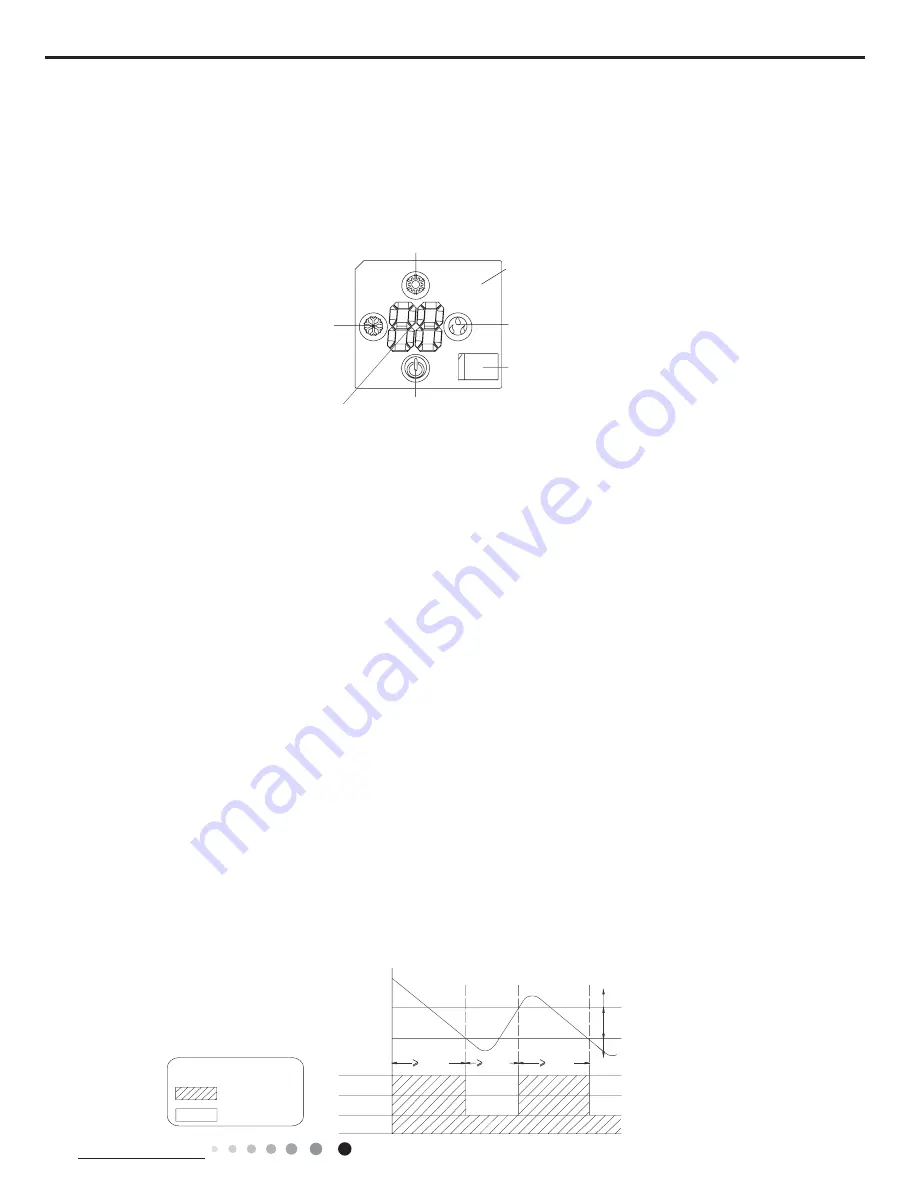
15
Technical Information
Service Manual
6.2 Brief Description of Modes and Functions
1. Summary
(1) Buzzer
When the controller is energized or receives signal from button (emergency operation switch on air conditioner) or remote controller, the
buzzer will give out a beep.
(2) Display
After energization, all icons will be displayed once. Operation icon is in red under standby status. After turning on the unit by remote
controller, operation icon is bright and corresponding set operation mode icon will be displayed (Mode icon include: cooling, heating,
drying).
(3) Temperature parameter
◆
Indoor set temperature (Tpreset)
◆
Indoor ambient temperature (Tamb.)
◆
Inner tube temperature of indoor evaporator (Ttube)
2. Introduction of Basic Mode Function
◆
Once the compressor is energized, there should be a minimum interval of 3 mins between two start-ups.
◆
If the unit is with memory function and is off before power failure, the compressor can be restarted without an interval of 3 mins; if the
◆
unit is on before power failure, the compressor will be restarted with an interval of 3 mins.
Once compressor is started, it won’t stop within 6 mins according to the change of room temp.
(1) Auto mode
①
Operation condition and process for auto mode
Under auto mode, the system will automatically select operation mode (cooling, heating, and fan) according to indoor ambient
temperature. There swill be 30s delayed for protection between mode switchover.
◆
When Tamb. ≥26
℃
, the system operates under cooling mode; Ex-factory set temperature is 25
℃
.
◆
Cool unit: when Tamb. ≤22
℃
, the system operates under fan mode; Ex-factory set temperature is 25
℃
.
◆
Heat pump unit: when Tamb. ≤22
℃
, the system operates under heating mode; Ex-factory set temperature is 20
℃
.
◆
22
℃
<Tamb.<26
℃
: The system operates under fan mode if turn on the unit to enter into auto mode for the first time; If switch to
auto mode from cooling, heating or fan mode, the system keeps previous operation mode; If switch to auto mode from drying mode, the
system operates under fan mode.
②
Display: Operation icon, actual operation mode icon, set temperature (that’s the display content of dual-8 nixie tube)
③
Protection function is same as that under each mode.
(2) Cooling mode
①
Operation condition and process for cooling mode
◆
When Tamb. ≥Tset+1
℃
, the system operates under cooling mode. In this case, the compressor, the ODU fan motor and the IDU fan
motor operates at set speed.
◆
When Tamb. ≤Tset-1
℃
, the compressor and the ODU fan motor stop, while the IDU fan motor operates at set speed.
◆
When Tset-1
℃
<Tamb. <Tset+1
℃
, the system will maintain its previous operation status.
In cooling mode, the 4-way valve is de-energized (4-way valve is not available for cooling only unit). Temperature setting range is
16~30
℃
.
Indicates operation
Indicates stop
T1 ˚C
Tpreset –1 ˚C
Compressor
Outdoor fan motor
Indoor fan motor
Graphic instruction:
(Same as below)
Tamb.
Stop cooling
Start cooling
Original operating status
6 min.
3 min.
6 min.
Set fan speed
Heating icon
Drying icon
Cooling icon
Dual-8 nixie
tube display
Operation icon
Receiver
window
For B2 panel
Display