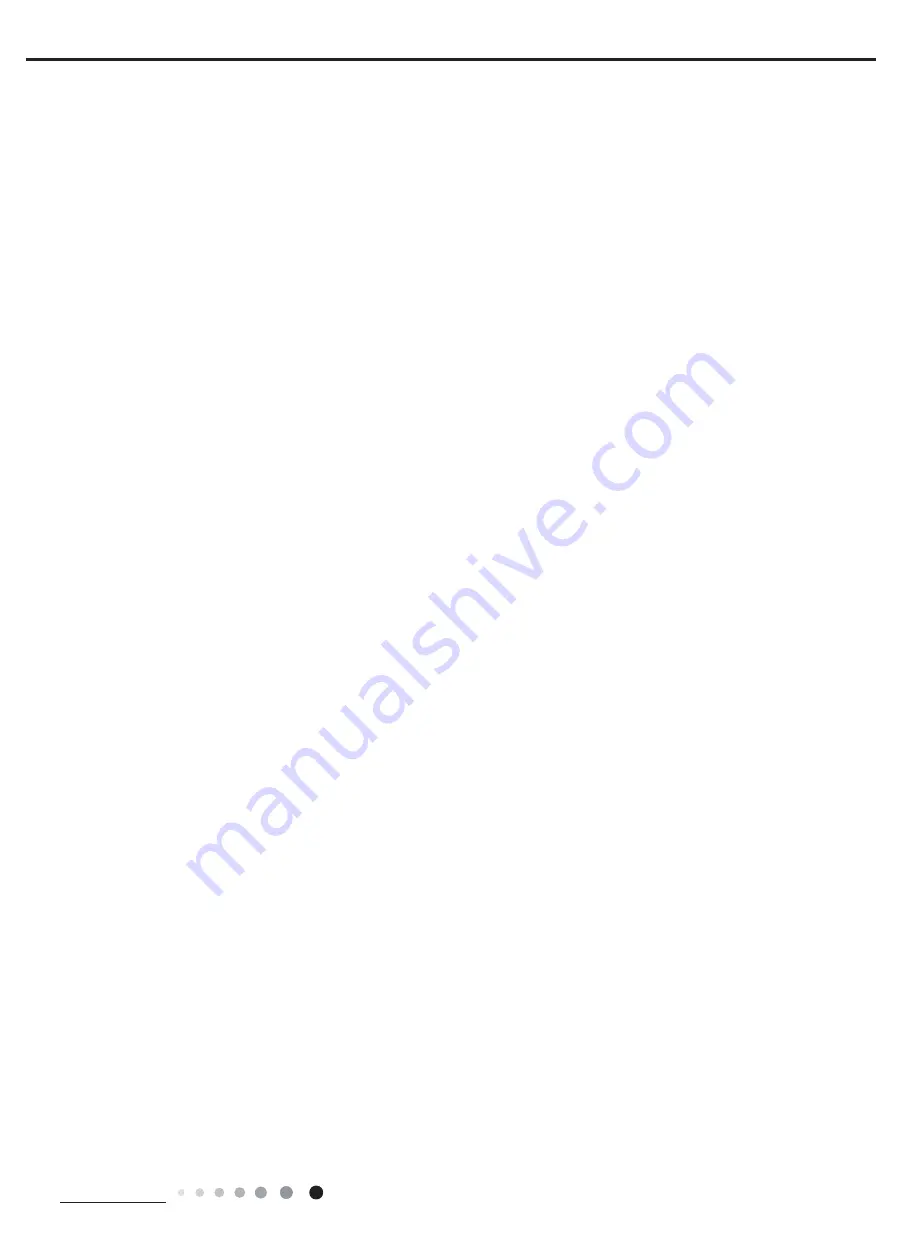
Table of Contents
Service Manual
8.5 Installation of Indoor Unit
....................................................................................37
8.6 Installation of Outdoor Unit
................................................................................40
8.7 Vacuum Pumping and Leak Detection
............................................................41
8.8 Check after Installation and Test Operation
.................................................41
9.2 Procedure of Troubleshooting
..........................................................................48
9.3 Troubleshooting for Normal Malfunction
......................................................61
10. Exploded View and Parts List
..............................................................63
.......................................................................................73
11.1 Removal Procedure of Indoor Unit
................................................................73
11.2 Removal Procedure of Outdoor Unit
.............................................................78
Appendix 1: Reference Sheet of Celsius and Fahrenheit
...............................88
Appendix 2: Configuration of Connection Pipe
.................................................88
Appendix 3: Pipe Expanding Method
.....................................................................89
Summary of Contents for KW09HQ3D6D Series
Page 80: ...77 Installation and Maintenance Service Manual...
Page 96: ...JF00304207...