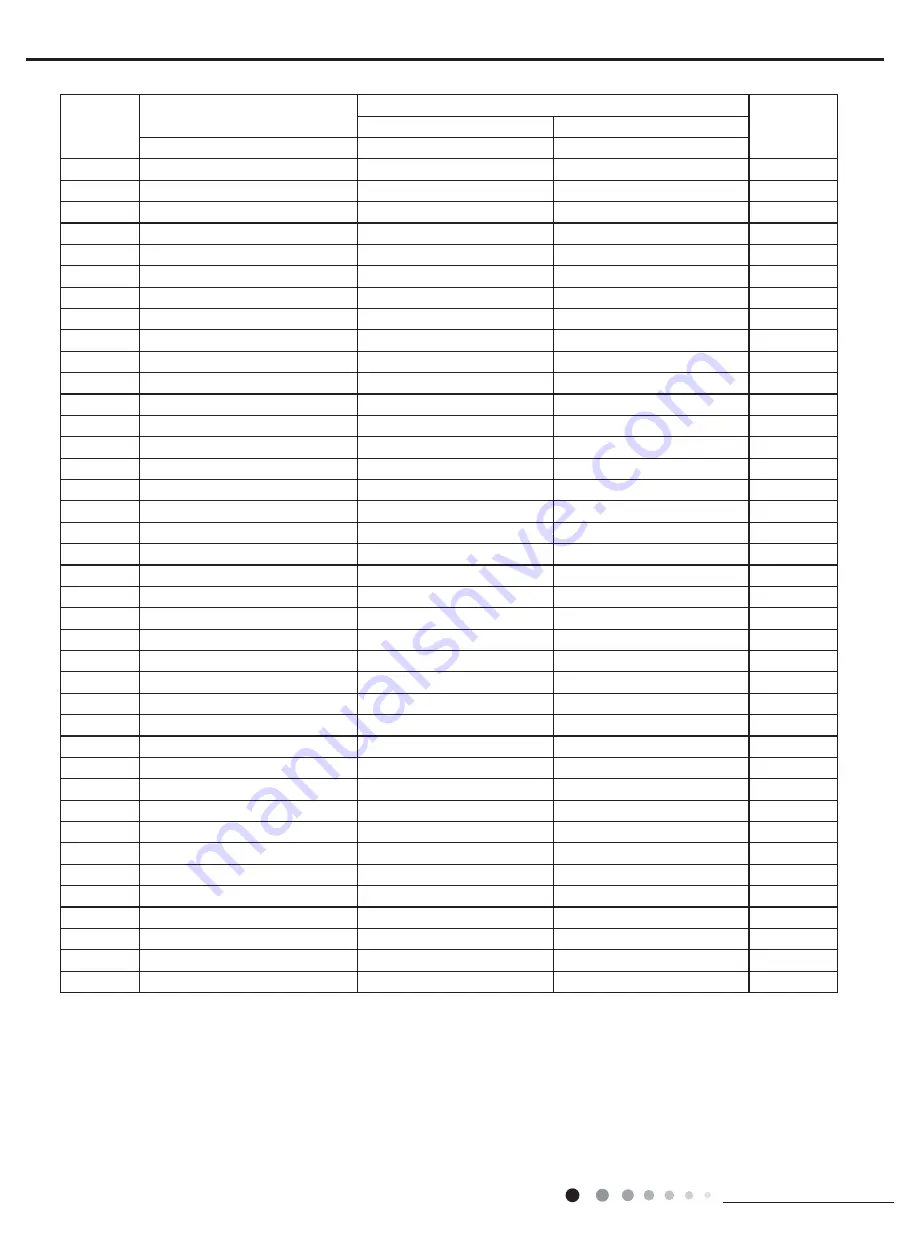
76
Installation and Maintenance
Service Manual
NO.
Description
Part Code
Qty
GWHD(18)NK3FO
GWHD(18)NK3FO
Product Code
CB228W03501
CB228W03500
1
Front Grill
22413025
22413025
1
2
Front Panel
01535013P
01535013P
1
3
Chassis Sub-assy
02803263P
02803302P
1
4
Drainage Connecter
06123401
06123401
1
5
Drainage hole Cap
06813401
06813401
3
6
Gas-liquid Separator Assy
07225017
07225017
1
7
Compressor and Fittings
00105249G
00105249G
1
8
Electric Heater(Compressor)
32003001
32003001
1
9
Tube Connector Sub-assy
06643008
06643008
1
10
Magnet Coil
4300040033
4300040033
1
11
4-Way Valve Assy
03073156
03073156
1
12
Right Side Plate
01303268P
01303268P
1
13
Valve Support Assy
07133845
07133845
1
14
Electronic Expansion Valve assy
07133846
07133846
1
15
Valve Support Sub-Assy
0171312802P
0171312802P
1
16
Cut off Valve
071302391
071302391
1
17
Cut off Valve
07130239
07130239
1
18
Valve Cover
20123029
20123029
1
19
Electric Expand Valve Fitting
43000084
43000084
1
20
Electric Expand Valve Fitting
4300008401
43000084
1
21
Temperature Sensor
3900007301
3900007301
1
22
Temperature Sensor
39000073
39000073
1
23
Wiring Clamp
26115004
26115004
1
24
Temperature Sensor
3900030901
3900030901
1
25
Rear Grill
01473043
01473043
1
26
Condenser Assy
01163938
01163938
1
27
Clapboard Assy
0123315301
0123315301
1
28
Coping
01255005P
01255005P
1
29
Supporting Board(Condenser)
01795010
01795010
1
30
Motor Support Sub-Assy
01705036
01705036
1
31
Fan Motor
1501506402
1501506402
1
32
Left Side Plate
01305093P
01305093P
1
33
Axial Flow Fan
10335008
10335008
1
34
Left Handle
26235401
26235401
1
35
Connecting Cable
4002054026
4002054026
0
36
Electric Box Assy
02613683
02613929
1
37
Electric Box
20113027
20113027
1
38
Radiator
49010252
49010252
1
39
Main Board
30148897
30148876
1
Above data is subject to change without notice.